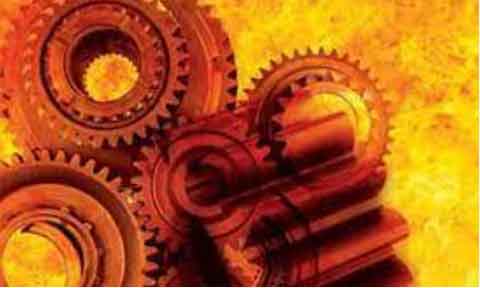
Heat treatment is a critical process in enhancing the properties of materials, but it can also introduce internal defects that are not visible on the surface. These hidden defects can compromise the structural integrity and performance of heat-treated components. Identifying and addressing these internal defects is essential to ensure the reliability and safety of the final products. In this article, we will explore common types of internal defects that can occur in heat-treated components and discuss methods for uncovering and mitigating these hidden dangers.
1.Internal Cracks:
- Cause: Internal cracks can develop during heat treatment due to factors such as improper quenching, rapid cooling rates, high thermal gradients, or residual stresses.
- Detection Methods:
- Non-destructive testing (NDT) techniques such as ultrasonic testing (UT), magnetic particle testing (MPT), or liquid penetrant testing (LPT) can be used to detect internal cracks.
- Radiographic testing (RT) or computed tomography (CT) can provide detailed images of internal structures to identify cracks.
- Mitigation Strategies:
- Optimize the quenching process to minimize thermal stresses and control cooling rates.
- Implement stress-relief heat treatments or tempering processes to reduce residual stresses and improve the component’s resistance to cracking.
2.Internal Inclusions:
- Cause: Inclusions, such as non-metallic particles or foreign substances, can be present in the material before or during the heat treatment process.
- Detection Methods:
- Ultrasonic testing, X-ray imaging, or microstructural analysis can help identify internal inclusions.
- Metallographic examination, including optical microscopy, can reveal the presence of inclusions within the material’s microstructure.
- Mitigation Strategies:
- Ensure proper material selection and quality control to minimize the presence of inclusions.
- Implement effective cleaning and surface preparation techniques before heat treatment to remove potential contaminants.
3.Internal Porosity:
- Cause: Porosity refers to voids or air pockets within the material, which can result from gas entrapment during solidification or inadequate degassing.
- Detection Methods:
- Ultrasonic testing and X-ray imaging can detect internal porosity by identifying areas of reduced material density.
- Metallographic examination can reveal the presence of voids or porosity in the material’s microstructure.
- Mitigation Strategies:
- Optimize casting or manufacturing processes to minimize gas entrapment and ensure proper degassing.
- Implement vacuum or controlled atmosphere heat treatment processes to reduce the likelihood of internal porosity formation.
4.Internal Decarburization:
- Cause: Internal decarburization occurs when the carbon content near the component’s core is reduced during heat treatment, leading to a gradient in hardness and compromised mechanical properties.
- Detection Methods:
- Metallographic examination, including microhardness testing, can reveal the extent of decarburization within the material’s cross-section.
- Mitigation Strategies:
- Control the heat treatment atmosphere to minimize oxygen ingress and carbon loss.
- Implement proper temperature and time controls to ensure uniform carbon distribution and minimize decarburization.
Uncovering internal defects in heat-treated components is crucial to ensure their structural integrity and performance. By employing appropriate non-destructive testing methods and implementing mitigation strategies tailored to specific defects, manufacturers can detect and address hidden dangers. It is important to maintain strict process control, optimize heat treatment parameters, and adhere to industry standards and specifications to minimize the occurrence of internal defects and produce high-quality heat-treated components.