Hypoid gear is type of spiral bevel gear whose axis does not intersect the meshing gear axis, creating a non-intersecting shaft configuration. This specialized gear setup is particularly useful in various applications, most notably in the automotive industry for rear axle drives. Let’s explore the advantages and common applications of hypoid gears in modern machinery:
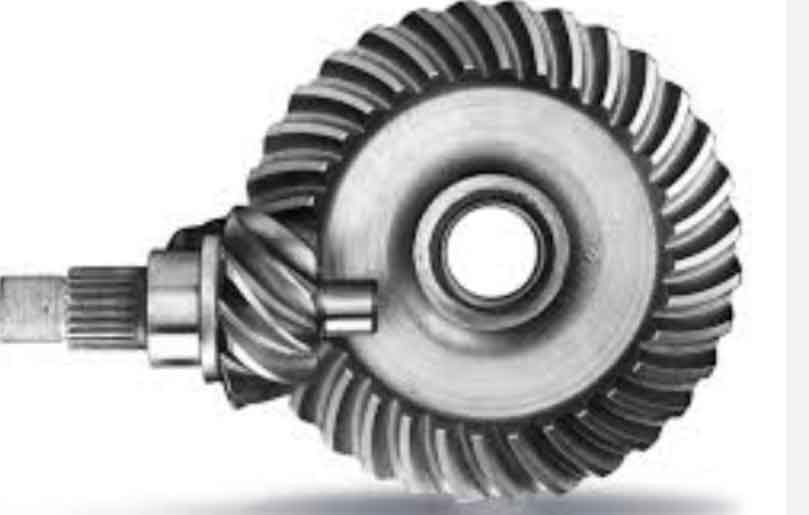
Advantages of Hypoid Gear
- Increased Smoothness and Quiet Operation: Hypoid gear offer smoother and quieter operation compared to spiral bevel gears due to their improved sliding between the teeth. This results in less vibration and noise, which is crucial for applications requiring low-noise environments, such as in passenger vehicles.
- High Torque Transmission: Due to their unique geometry, hypoid gear can transmit higher torques at right angles. The hypoid gear design allows for more gear teeth to engage at any given time, which distributes the load more evenly and allows for the transmission of greater forces.
- Durability and Longevity: The increased surface contact and gradual engagement of the teeth in hypoid gear reduce stress and wear on each tooth, leading to increased durability and a longer lifespan of the gear system.
- Compact Design: Hypoid gear enable a more compact gear system layout. In automotive applications, this allows for a lower floor in the vehicle and more space for other uses because the drive shaft can be positioned lower relative to the axes of the wheels.
- Improved Efficiency: While hypoid gear do have higher frictional losses than some other types of gears, advancements in lubrication technologies and gear design have significantly improved their efficiency, making them suitable for high-performance applications.
Applications of Hypoid Gear
- Automotive Industry: Hypoid gear is predominantly used in the rear axles of cars and trucks. They are especially prevalent in vehicles with rear-wheel drive, where they facilitate the transmission of power from the engine to the wheels at a 90-degree angle, optimizing space and performance.
- Aerospace and Aviation: In the aerospace sector, the compact and efficient design of hypoid gear is advantageous for various systems within aircraft, where space is at a premium and reliability is critical.
- Heavy Machinery: In heavy-duty applications such as construction and mining equipment, hypoid gear is used due to their ability to withstand high torque and rough operating conditions.
- Marine Equipment: The robustness and efficiency of hypoid gear make them suitable for marine applications, including in the propulsion systems of boats and ships.
- Power Tools and Robotics: In robotics and power tools, hypoid gear is often used for their compact size and ability to transmit significant amounts of power relative to their size, which is crucial in tightly integrated electronic and mechanical systems.
Continuing from the applications and moving into further details, hypoid gear not only serve a critical function in a variety of industries but also drive innovations in gear technology and machinery design. Here’s more on how their unique properties are applied in various scenarios and what future trends might look like.
Further Applications
- Wind Turbines: Hypoid gear can also be found in wind turbines, where they are used in the azimuth adjustment mechanism that aligns the turbine blades with the wind to maximize efficiency. Their ability to handle high torque loads and operate quietly makes them ideal for this application.
- Agricultural Machinery: In agriculture, hypoid gear is used in machinery such as tractors and combines. These gears help to transmit power efficiently in machines that require robust performance under variable loads and conditions.
Advantages in Maintenance and Installation
- Ease of Maintenance: The durability of hypoid gear reduces the frequency and complexity of maintenance. Although they require good lubrication to manage friction and heat, modern synthetic lubricants and precise manufacturing have greatly extended the intervals between maintenance.
- Installation Flexibility: The configuration of hypoid gear allows for more flexibility in the design and installation of machinery. This is particularly advantageous in complex systems where space constraints require creative solutions for power transmission pathways.
Technological Advancements
- Materials Science: Innovations in materials science have led to the development of stronger and more wear-resistant materials for hypoid gear. These materials can withstand higher temperatures and loads, further increasing the efficiency and lifespan of these gears.
- Precision Engineering: Advances in CNC machining and precision engineering have enhanced the accuracy with which hypoid gear is produced. This improvement in manufacturing precision not only boosts performance but also reduces noise and increases the overall efficiency of the gear system.
- Computational Fluid Dynamics (CFD): The use of CFD in designing hypoid gear helps optimize the shape and angle of the gears for maximum efficiency and minimum noise, taking into account the complex interactions between the gear surfaces and lubricants.
Future Trends
- Electric Vehicle (EV) Drivetrains: As the automotive industry shifts towards electric vehicles, hypoid gear is expected to play a crucial role in the design of compact, efficient drivetrains that maximize cabin space and extend battery range.
- Sustainable Manufacturing Practices: There is a growing trend towards sustainability in manufacturing, which includes making hypoid gear. This includes using environmentally friendly lubricants and recycling worn-out gears.
- Smart Gearing Systems: The integration of sensors and IoT technology into hypoid gearing systems could lead to ‘smart gears’ capable of predictive maintenance, where the system can monitor its condition and schedule maintenance only when necessary, thereby reducing downtime and operational costs.
Integration with Advanced Control Systems
- Active Load Balancing: Advanced control systems can dynamically adjust the load distribution across hypoid gear teeth in real-time, enhancing performance under varying operating conditions. This can extend the lifespan of the gears and reduce maintenance needs.
- Vibration Reduction Technologies: Integration of active vibration control systems with hypoid gear can further reduce noise and increase the longevity of machinery. This is particularly important in precision applications such as in aerospace or sensitive scientific instruments.
Expansion into New Industries
- Renewable Energy Systems: Beyond wind turbines, hypoid gear could find new applications in other renewable energy technologies such as hydroelectric and tidal energy converters. Their ability to handle high torque and shock loads efficiently makes them ideal for the variable and harsh operating environments often encountered in renewable energy applications.
- Healthcare Equipment: In the medical field, hypoid gear could be used in equipment requiring precise and quiet operation, such as MRI machines or robotic surgery tools. Their compact size and efficient power transmission are crucial for the densely packed and sensitive machinery used in medical diagnostics and treatments.
Future Research and Development
- Nano-Tribology: Research into nano-tribology—the study of friction, wear, and lubrication at the nanoscale—could lead to breakthroughs in hypoid gear lubrication systems. Developing lubricants that can effectively reduce friction and wear at a microscopic level would drastically increase the efficiency and durability of hypoid gears.
- 3D Printing of Gears: The potential for 3D printing technologies to create complex gear shapes like those of hypoid gear could revolutionize their manufacturing process. This would not only reduce costs but also allow for the rapid prototyping of customized gears for specific applications, enhancing design flexibility and experimentation.
Challenges and Opportunities
- Material Limitations and Innovation: One of the primary challenges in advancing hypoid gear technology is the limitation imposed by current materials. Developing new, more resilient materials that can handle even greater loads and speeds is crucial. This also opens up opportunities for material scientists and engineers to innovate solutions that could redefine what’s possible with gear technology.
- Environmental Impact: As industries seek more sustainable manufacturing and operational practices, hypoid gear will need to adapt to these changes. This includes not only the materials and lubricants used but also the processes by which they are manufactured, aiming to reduce environmental impact while maintaining or improving performance.
- Cost-Benefit Analysis: While hypoid gear offer many advantages, their design and manufacturing are often more complex and costly than other gears. Balancing these costs with the benefits in terms of enhanced performance and durability will be key, especially as markets become more cost-sensitive.
Hypoid gear, with their unique blend of durability, efficiency, and compact design, continue to be at the forefront of mechanical engineering innovations, adapting to new technologies and demands in various industries. They are a perfect example of how traditional mechanical components evolve alongside cutting-edge technologies to meet the changing needs of modern machinery.In conclusion, hypoid gear is highly valued in modern machinery for their unique characteristics, including their ability to transmit high levels of torque smoothly and quietly while occupying less space. This makes them indispensable in many of today’s high-performance and space-constrained applications.