Spiral bevel gear is type of bevel gear with helical teeth. They are used to transmit power between shafts that are intersecting and non-parallel. The geometry of spiral bevel gear is crucial for their proper functioning. Here are some key aspects of their geometry:
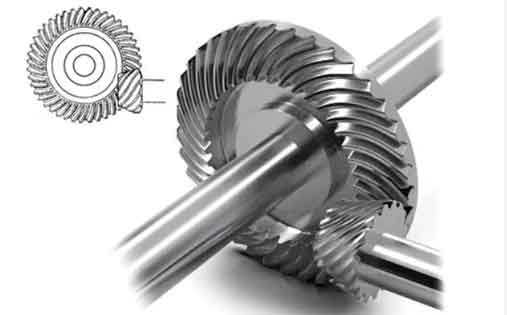
- Pitch Diameter: The pitch diameter is the theoretical diameter of spiral bevel gear where the teeth mesh. It is calculated at a specific point along the height of spiral bevel gear tooth. The pitch diameter is important for determining gear ratio and tooth contact.
- Pitch Angle: The pitch angle is the angle between the tooth trace and a plane perpendicular to spiral bevel gear axis. In spiral bevel gears, the pitch angle varies along the height of the tooth due to the helical shape of the teeth.
- Helix Angle: The helix angle is the angle between the tooth trace and a plane parallel to spiral bevel gear axis. It is constant for a given gear and determines the helical shape of the teeth.
- Tooth Profile: The tooth profile of a spiral bevel gear is a complex curve that results from the combination of the helical shape and the involute profile. The involute profile ensures smooth and gradual engagement and disengagement of the teeth, reducing wear and noise.
- Backlash: Backlash is the clearance between mating teeth in spiral bevel gear system. It is essential to allow for smooth operation and to prevent binding. However, excessive backlash can lead to reduced efficiency and increased noise.
- Tooth Contact Pattern: The tooth contact pattern is the area on the tooth where contact occurs between mating gears. It is crucial for distributing load evenly across the teeth and ensuring smooth operation. Adjustments to spiral bevel gear geometry, such as tooth thickness and spiral bevel gear alignment, can influence the contact pattern.
- Gear Ratio: The gear ratio of spiral bevel gear system is determined by the number of teeth on spiral bevel gear. For spiral bevel gear, the gear ratio also depends on the pitch and helix angles. The spiral bevel gear ratio determines the speed and torque relationship between the input and output shafts.
Understanding the geometry of spiral bevel gear is essential for designing and manufacturing gear that operate efficiently and reliably. It involves complex mathematical calculations and considerations to ensure proper tooth engagement, load distribution, and noise reduction.