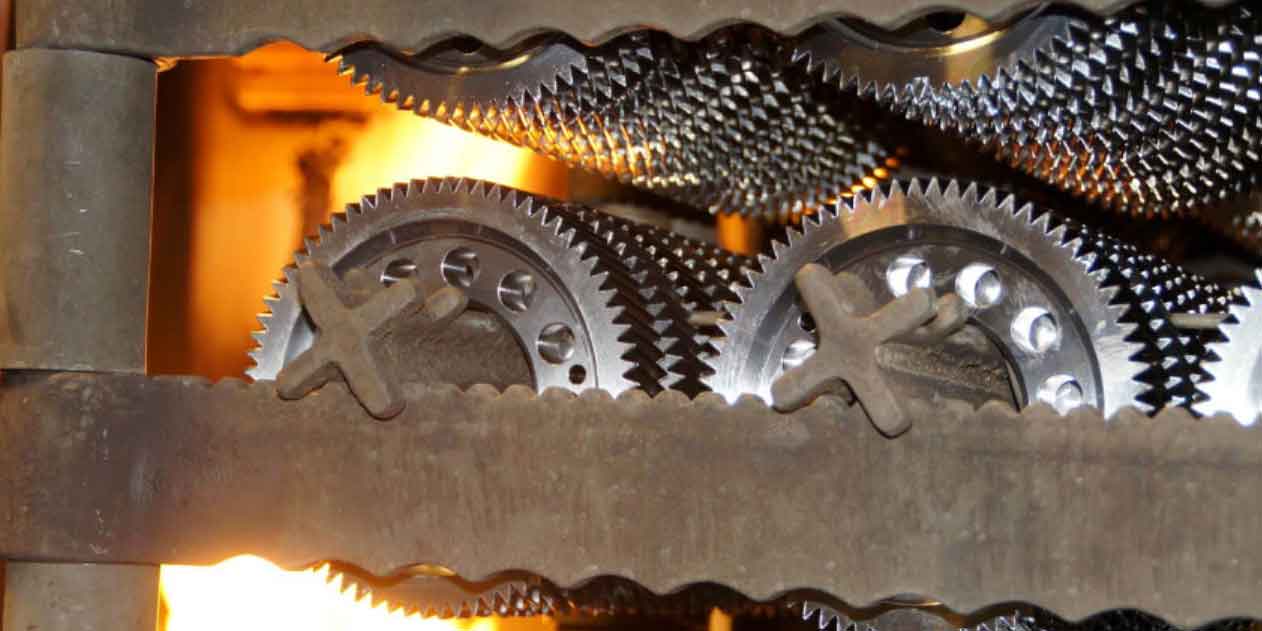
Gear forgings have emerged as a game-changer in the field of gear manufacturing, offering a myriad of benefits that contribute to the success of various industries. From enhanced performance and reliability to cost-effectiveness and design flexibility, gear forgings have revolutionized the way gears are produced. This article explores the benefits of gear forgings and their impact on the success of diverse applications.
I. Superior Strength and Durability:
Gear forgings are renowned for their exceptional strength and durability. The forging process, which involves compressive forces and controlled deformation, refines the grain structure of the metal, resulting in gears with high tensile and fatigue strength. This strength allows gear forgings to withstand heavy loads, shock loads, and harsh operating conditions, ensuring long-lasting performance and minimizing the risk of gear failure.
II. Enhanced Performance and Efficiency:
Gear forgings contribute to enhanced performance and efficiency in various applications. The precise dimensional accuracy achieved through forging ensures proper gear meshing and reduces power losses due to friction and misalignment. The uniform grain structure of gear forgings minimizes stress concentrations, reducing the risk of wear, fatigue, and noise. By optimizing gear performance, gear forgings enable systems to operate with improved efficiency, resulting in energy savings and increased productivity.
III. Reliability and Longevity:
The reliability and longevity of gear forgings are crucial factors in the success of any application. Gear forgings undergo rigorous testing and inspection to ensure high-quality standards. The absence of internal defects, such as porosity and voids, and the uniform grain structure contribute to the gear’s reliability and resistance to wear, abrasion, and impact. Gear forgings are designed to withstand the demands of heavy-duty applications, providing extended service life and reducing maintenance and replacement costs.
IV. Customizability and Design Flexibility:
Gear forgings offer unparalleled customizability and design flexibility. The forging process allows for the creation of complex gear geometries, specific tooth profiles, and tailored features to meet the unique requirements of different applications. Engineers can optimize gear designs for load distribution, torque transmission, and system performance. The flexibility of gear forgings empowers designers to create gears that are precisely tailored to the application, resulting in optimized performance and improved overall success.
V. Cost-Effectiveness:
Gear forgings offer long-term cost-effectiveness despite their initial investment. The precision shaping achieved through forging reduces the need for extensive machining and minimizes material waste. The inherent strength and durability of gear forgings result in reduced maintenance and replacement costs over the gear’s lifespan. Additionally, the enhanced performance and efficiency of gear forgings contribute to energy savings, making them a cost-effective choice in the long run.
VI. Wide Range of Applications:
Gear forgings find applications in diverse industries, including automotive, aerospace, industrial machinery, power generation, and more. The versatility of gear forgings allows them to excel in applications that demand high performance, reliability, and efficiency. Gear forgings have become the preferred choice for critical components in these industries, playing a crucial role in the success of their products and operations.
Gear forgings unleash a multitude of benefits that are instrumental in the success of various applications. With their superior strength, durability, enhanced performance, reliability, customizability, cost-effectiveness, and versatility, gear forgings have transformed gear manufacturing. By incorporating gear forgings, industries can achieve optimal performance, reduce downtime, improve efficiency, and enhance overall success in their applications. Gear forgings have truly unlocked the potential of gear manufacturing and continue to pave the way for future advancements in the field.