Precision forging is a manufacturing technique that holds immense power in transforming metal into high-quality components with superior strength, accuracy, and reliability. This article delves into the various aspects of precision forging and highlights its potential in revolutionizing the manufacturing industry.
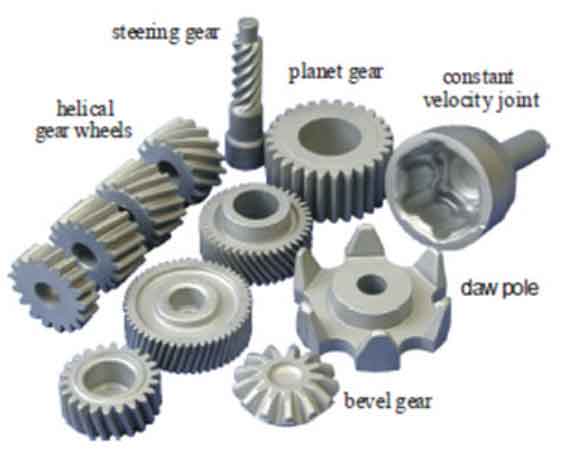
I. Superior Strength and Structural Integrity:
Precision forging excels in producing components with exceptional strength and structural integrity. The controlled deformation of metal during the forging process aligns the grain structure, eliminating weak points and enhancing the material’s mechanical properties. The resulting components exhibit superior load-bearing capacity, resistance to fatigue, and improved durability compared to components manufactured through other methods.
II. Complex Geometries and Design Flexibility:
Precision forging empowers manufacturers to create components with complex geometries and intricate designs. The versatility of precision forging allows for the production of parts with high dimensional accuracy, tight tolerances, and intricate shapes that are difficult to achieve through alternative manufacturing techniques. This design flexibility enables the development of innovative products with enhanced functionality and performance.
III. Material Optimization and Cost Efficiency:
Precision forging optimizes material usage, reducing waste and maximizing the utilization of raw materials. By shaping the metal into the desired form, precision forging minimizes the need for excessive machining or material removal, resulting in cost savings and improved efficiency. Furthermore, the strength and durability of precision-forged components reduce the need for frequent replacements or repairs, leading to long-term cost efficiency.
IV. High Production Output:
Precision forging is capable of achieving high production output, making it suitable for large-scale manufacturing. With the use of automated forging machines and optimized production processes, manufacturers can produce components at a faster rate without compromising quality. This scalability makes precision forging a viable solution for industries that require high volumes of components within tight timelines.
V. Enhanced Surface Finish and Consistency:
Precision forging yields components with superior surface finish and reduced surface porosity compared to other manufacturing techniques. The controlled deformation of metal during forging minimizes surface imperfections, resulting in parts with improved aesthetics and reduced post-processing requirements. The consistency achieved in precision forging ensures that every component meets the desired specifications, enhancing quality control and reducing variability.
VI. Wide Range of Industry Applications:
Precision forging finds applications across various industries, including automotive, aerospace, energy, and heavy machinery. In the automotive industry, precision-forged components are used in engine parts, transmission systems, steering mechanisms, and suspension components, enhancing performance and reliability. In aerospace, precision forging is critical for manufacturing turbine blades, landing gear components, and structural parts that withstand extreme conditions. The energy sector benefits from precision-forged components in turbines, power transmission systems, and oil and gas equipment, ensuring efficient and reliable operations.
Precision forging is a powerful manufacturing technique that unlocks numerous benefits for industries seeking high-quality, durable, and cost-effective components. Its ability to produce parts with superior strength, complex geometries, and excellent surface finish makes it a valuable asset in the manufacturing industry. By harnessing the potential of precision forging, manufacturers can elevate the performance, efficiency, and reliability of their products, leading to significant advancements in various sectors.