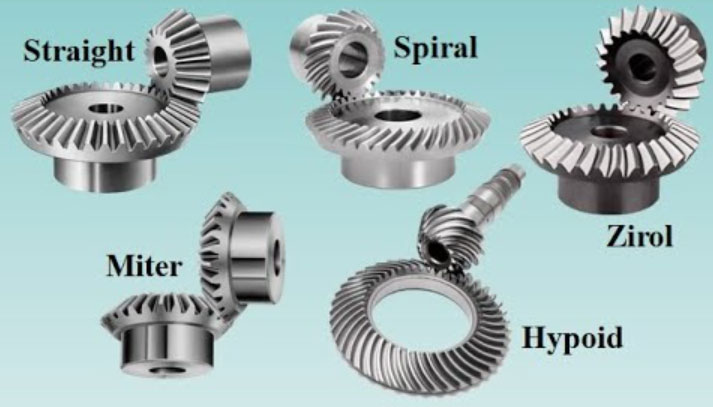
The geometry and tooth profiles of bevel gears are essential aspects that determine their functionality and performance. The tooth profiles of bevel gears are designed to ensure smooth and efficient power transmission between intersecting or non-intersecting shafts at various angles. Let’s delve into the geometry and tooth profiles of bevel gears:
1. Conical Shape:
Bevel gears have a conical shape, with the teeth formed on the surface of a cone. The gear’s conical form allows for the transmission of power and motion between shafts that intersect or have different orientations.
2. Pitch Cones:
The geometry of bevel gears is defined by pitch cones. Pitch cones are imaginary cones that represent the ideal contact between the mating gears. The apex of each pitch cone is located at the intersection point of the gear axes.
3. Pitch Angle:
The pitch angle, also known as the cone angle, is the angle formed by the generatrix line of the pitch cone and the gear axis. It determines the ratio between the rotational speed and torque transmitted by the bevel gears.
4. Tooth Profile:
The tooth profile of bevel gears is determined by the intersection of the gear teeth with the pitch cones. The most common tooth profiles for bevel gears are straight tooth and spiral tooth profiles.
- Straight Tooth Profile: In straight bevel gears, the tooth profile is a straight line on the tooth surface. Straight tooth bevel gears are typically used in low-speed applications and have higher noise levels compared to spiral bevel gears.
- Spiral Tooth Profile: Spiral bevel gears have curved teeth that are shaped like a spiral on the tooth surface. The spiral tooth profile provides smoother engagement, reduced noise, and improved load distribution. Spiral bevel gears are commonly used in high-speed applications and systems that require precision and low noise levels.
5. Tooth Surface Contact:
In bevel gears, the tooth contact occurs along a line called the tooth contact line. The contact line is the portion of the tooth surfaces where they come into contact during operation. It is essential to ensure proper tooth contact and alignment to minimize wear, noise, and maximize power transmission efficiency.
6. Tooth Engagement:
The engagement of bevel gear teeth is crucial for smooth and efficient power transmission. Proper tooth engagement ensures the load is distributed evenly across the gear teeth, minimizing stress concentration and improving the overall performance and durability of the gears.
The geometry and tooth profiles of bevel gears are designed to optimize power transmission efficiency, minimize noise, and ensure reliable operation. The choice between straight tooth and spiral tooth profiles depends on the specific application requirements, including speed, torque, precision, and noise considerations. By understanding the geometry and tooth profiles of bevel gears, engineers can design and select the most suitable gear types for their intended applications, ensuring optimal performance and functionality.