China is a big country in automobile manufacturing. Under the background of rapid social and economic development in China, the demand for automobile gears is increasing. It is common to use the five-tool method to process circular arc shrinkage bevel gears for automobile gears in China. However, foreign countries have explored to implement the full-process method of gear milling, and then use the UMC method of gear grinding through the heating process to process high-precision circular arc shrinkage bevel gears.
Compared with the traditional five-tool machining method, this method has the following advantages:
First, improve processing efficiency and reduce costs. Because this method reduces the times of machine tool adjustment and cutter head replacement, the cutting time of each pair of bevel gears can be reduced by one third. Therefore, it can effectively reduce the number of adjustments and greatly improve the production efficiency when processing batch workpieces. This method belongs to the cutter head system of the whole dry cutting process, and the cost can also be greatly reduced compared with the wet cutting tool.
Second, ensure that the geometric accuracy of bevel gears of the same batch is consistent. When the full-process method is used for gear cutting, the big wheel and the small wheel are clamped at the same time, and two sides are machined at one time, which effectively ensures the geometric accuracy of the same batch of bevel gears and makes the precision stability of the finished bevel gears better.
Third, the strength of bevel gear pair is improved and the tool life is extended. When using the five-tool method to process the circular arc contraction bevel gear, the cutter head of gear cutting needs to cut from one end of the tooth slot to the other end, and the minimum width of the tooth slot of the tool limits the width of the tool tip. When the bevel gear is processed by the full process method, the grooves of the big wheel and the small wheel have a fixed width in the rectangular direction of the bevel gear.
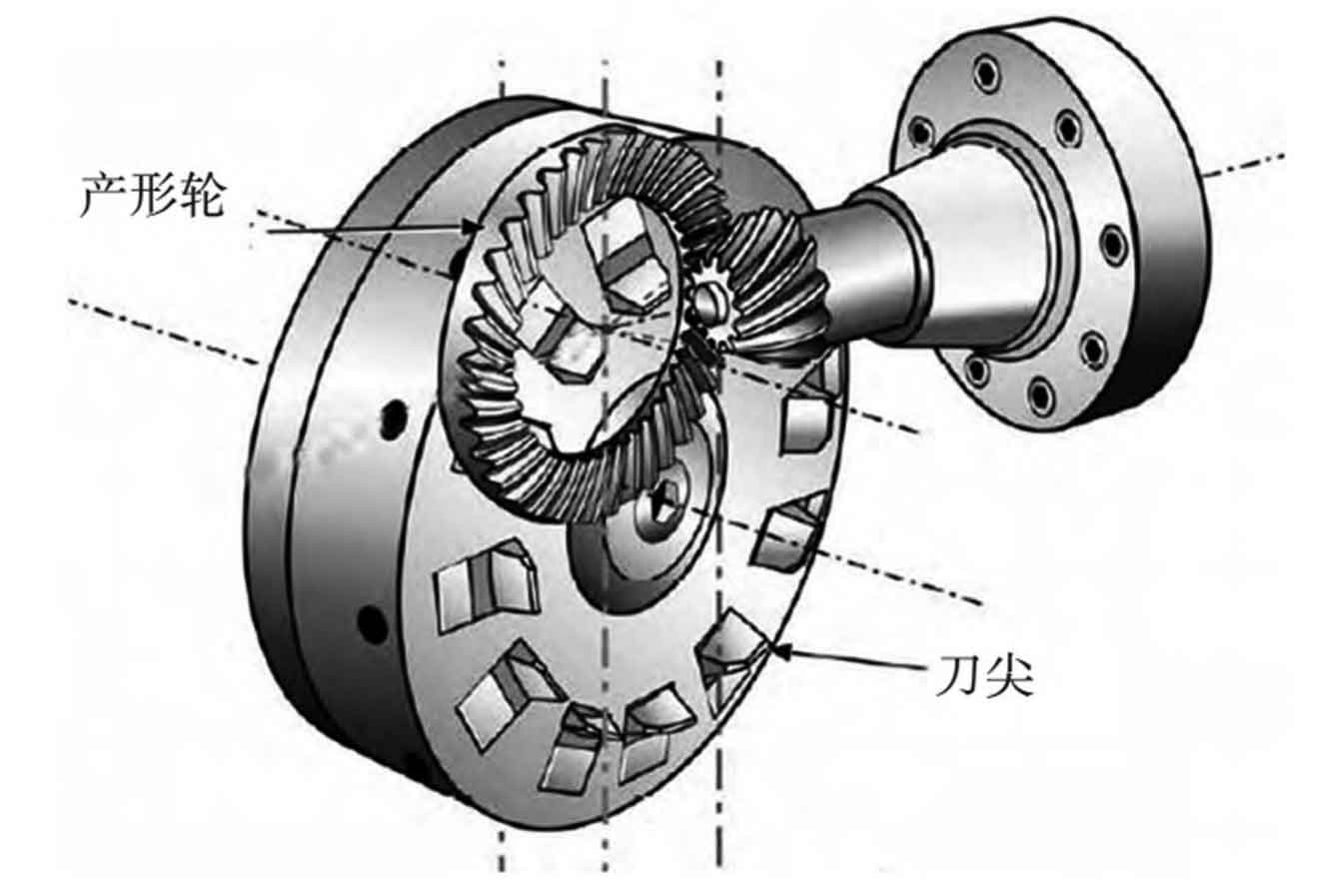
This equal slot width ensures that the maximum tool tip distance and the maximum fillet radius of the tool tip can avoid tool wear and prolong tool life during gear cutting. In addition, when processing the fillet of the tooth root and the bottom surface of the tooth, it can improve the smoothness of the connection and promote the strength of the bevel gear. Fourth, it can realize dry cutting and gear grinding. The five-knife method requires three cutter heads, which is not really dry cutting from the perspective of modern machining theory. The whole process processing can realize the dry cutting of modern processing. The cycloid contour bevel gear cannot be grinded, and the high-precision bevel gear cannot be grinded by the cycloid contour tooth processing method. However, the milling tooth used by the full-process method and the arc shrinkage tooth grinded after the heating process can produce high-quality and high-precision bevel gears.