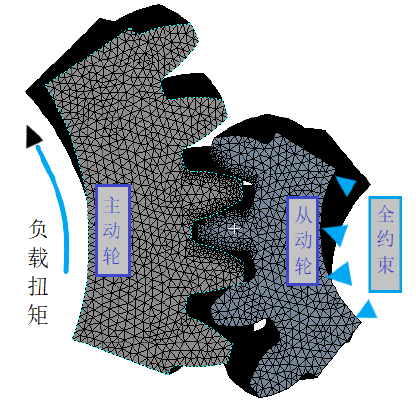
In order to study the time-varying meshing stiffness of helical gears, a three-dimensional model is established by three-dimensional software, and static contact analysis is carried out by using finite element software. In order to simplify the calculation model, only part of tooth pairs are reserved for contact analysis. The simplified model is shown in Figure 1 below As shown in Fig. 1, the meshing of the contact part of the gear tooth is refined, in which the driving gear tooth surface is the contact surface, and the passive gear tooth surface is the target surface. The penalty function method is used to solve the problem. The passive wheel is fully constrained, and the torque applied to the driving wheel is 3.34 × 108n · mm, and the degrees of freedom in other directions are fully constrained 43 groups of data, the time-varying meshing stiffness curve of helical gear is obtained by using the following formula, as shown in Figure 2. The maximum, minimum and average value of time-varying meshing stiffness obtained by the solution are counted.
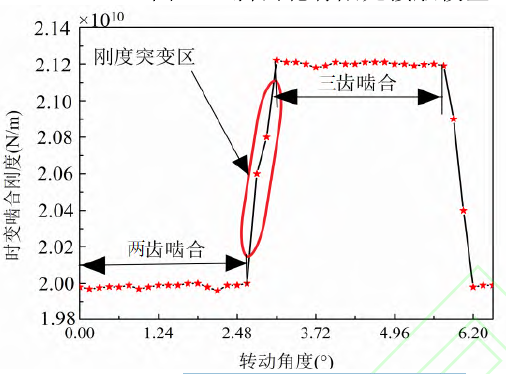
The contact deformations of a pair of gears at the meshing positions are δ 1 and δ 2, respectively
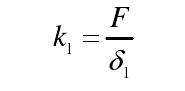
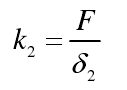
Therefore, the total meshing stiffness can be expressed as follows:
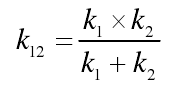