
According to the accurate modeling idea of spur gear pair, the meshing stiffness calculation can be calculated by the inductive flow chart.Select a pair of engagement spur gear pairs.In order to further verify the correctness of the mathematical model, the finite element discrete calculation model (Figure 1) with the same parameters is established at the same time. The two calculation TVMS results are shown in Figure 2. From Figure 2, it can be seen that the calculation results of the finite element and the mathematical model basically coincide, which effectively verifies the correctness of the accurate modeling of engagement stiffness proposed in this paper.
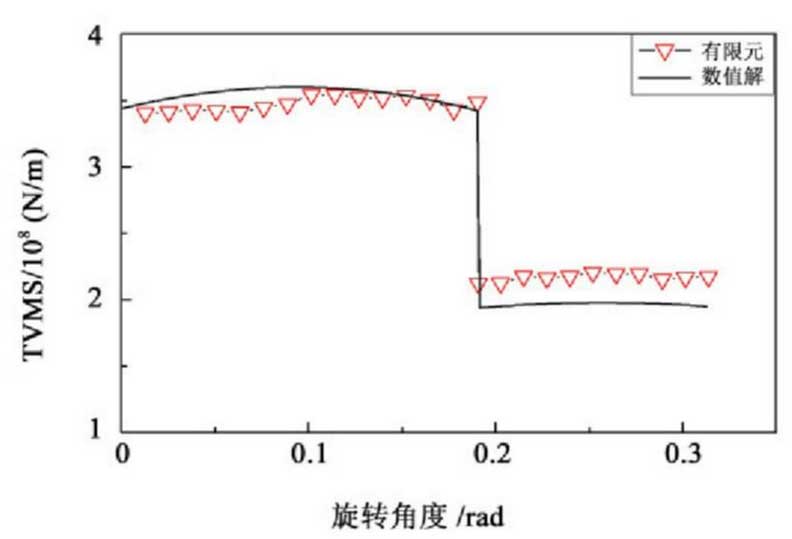
Figure 3 shows the curve of the real-time engagement angle of the main-slave gear meshing point with rotation angle. The engagement angle of the gear pair increases or decreases nonlinearly from the meshing point of the main-slave gear face to the meshing point of the gear pair (point B2) to the meshing point B1, and the intersection point P of the two curves is the pressure angle of the joint (20 degrees).
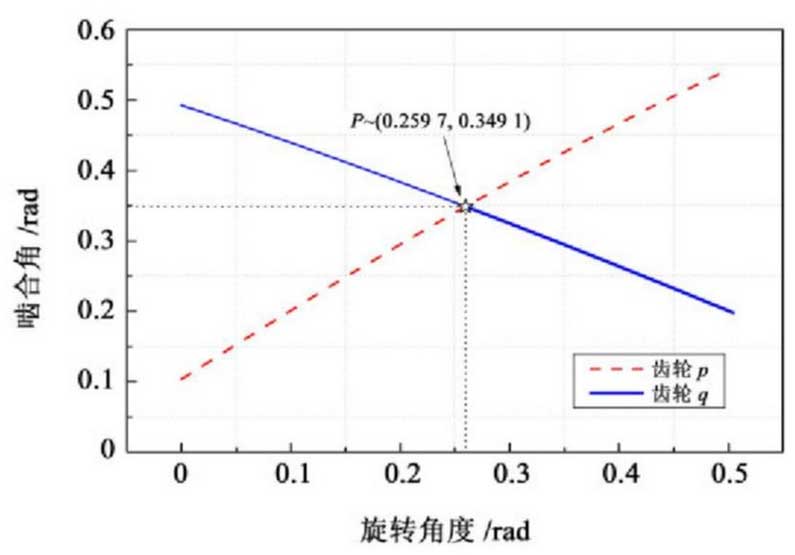
TVMS curves of gear pairs with different tooth widths are shown in Figure 4. The meshing stiffness of single-double meshing area increases with the increase of tooth width, and the alternating stiffness difference of single-double meshing area also increases.From the angle of strength design and dynamics analysis and prediction, when designing gears, the tooth width should be reasonably selected to meet the allowable range of design load, so as to reduce the rodent/rodent impact caused by single and double engagement alternation, thus improving the running smoothness of gear transmission system and reducing the vibration and noise of the system.
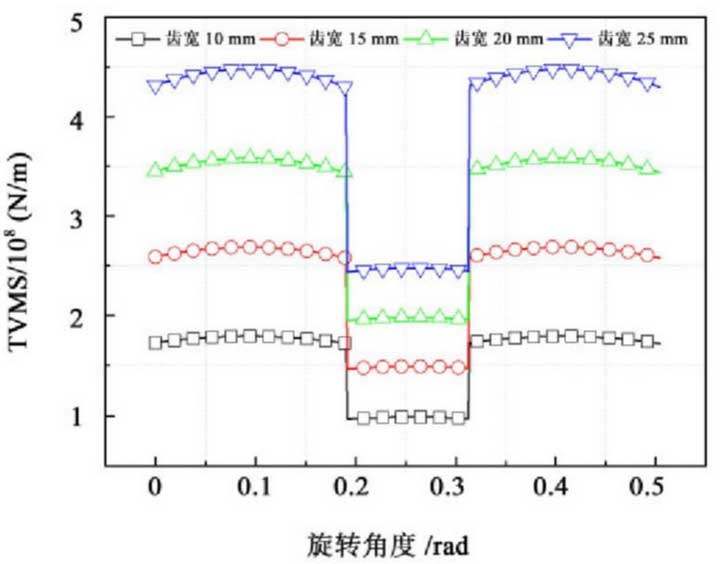
Under the determination of gear design parameters, different shaft diameters will change the rigidity of gear base and influence the meshing rigidity. Due to the diversity of shaft-gear assembly methods and the complexity of boundary condition simulation, it is assumed that fixed assembly method is used for shaft and gear (there is no relative displacement between the two interfaces).
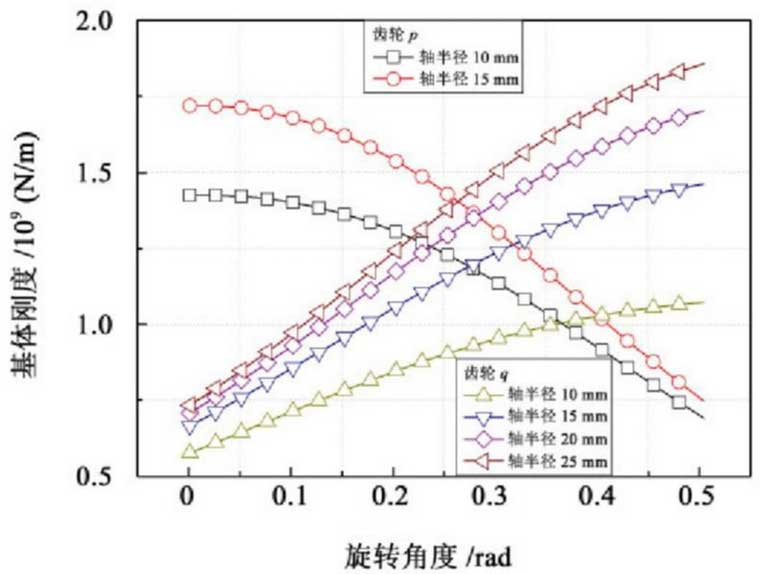
The influence of different axle radii on the base rigidity of main and slave gears and the meshing rigidity of gear pairs are analyzed respectively. The calculation results are shown in Fig. 5 and Fig. 6.As can be clearly seen in Figure 5, the relationship between the base stiffness and the axial radius is non-linear with the meshing rotation angle, and the difference of stiffness decreases gradually from the root to the top along the tooth profile.
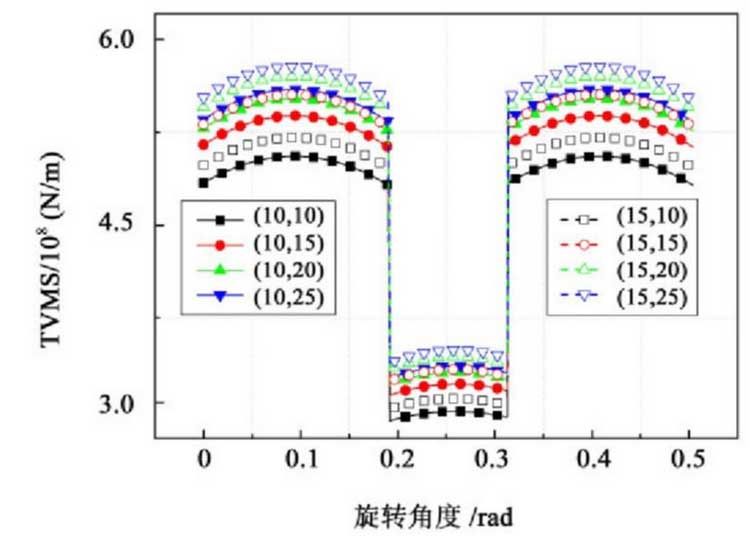
The meshing stiffness combination calculation will be carried out by selecting different main and slave gear shaft radius. TVMS increases nonlinearly with the increase of shaft radius (Figure 6). It can be seen that the meshing stiffness of gear system can be adjusted slightly by changing the shaft radius of main and slave gears. The increase of shaft radius also further improves the anti-deflection performance and speed smoothness of the rotor.
Accurately simulating and calculating time-varying meshing stiffness (TVMS) of gear pair is very important for analyzing dynamic performance response indexes such as vibration and noise of gear transmission system.Based on geometry and potential energy method, an accurate modeling method for calculating spur gear pair is put forward and an example is analyzed. The main research contents and results are as follows:
(1) Based on the space engagement theory of spur gear pair, the geometric motion model of gear engagement is constructed, and the range of double-single-double engagement and the engagement critical point of engagement of meshing teeth on the engagement action line from meshing to rodging are deduced in detail. The engagement limit boundary conditions of standard involute profile are analyzed effectively and real-time, and the TVMS mathematical calculation and analysis model is constructed by combining potential energy method.
(2) A pair of meshing spur gear pairs are selected for application analysis, TVMS calculation is carried out by numerical algorithm, and corresponding finite element model is established to verify the results, which basically agree with each other.With the increase of toothed width, the difference of alternating stiffness in single-double engagement area also increases; the axial radius shows a non-linear relationship with TVMS; the calculation of TVMS data curve shows that under the allowable range of design load and the determination of gear parameters, reasonable selection of toothed width and axial radius dimensions can present a small adjustment effect of engagement stiffness, thus optimizing the meshing stiffness of gears and improving the meshing stiffness of gears.The anti-deflection performance of high rotor is the basic application research for dynamic calculation of gear system.