Abstract:
This paper focuses on the vibration characteristics of the hypoid gear transmission system in a drive axle. By considering various excitations such as time-varying mesh stiffness, damping, transmission errors, and impacts, a multi-variable coupling vibration model is established based on the lumped mass method. The vibration differential equations are derived according to Newton’s second law and solved using the Runge-Kutta (RK) method. The vertical, torsional, and axial vibrations of the driving and driven gears before and after modification are compared, and the influence of input speed and load torque on the vibration characteristics is discussed.
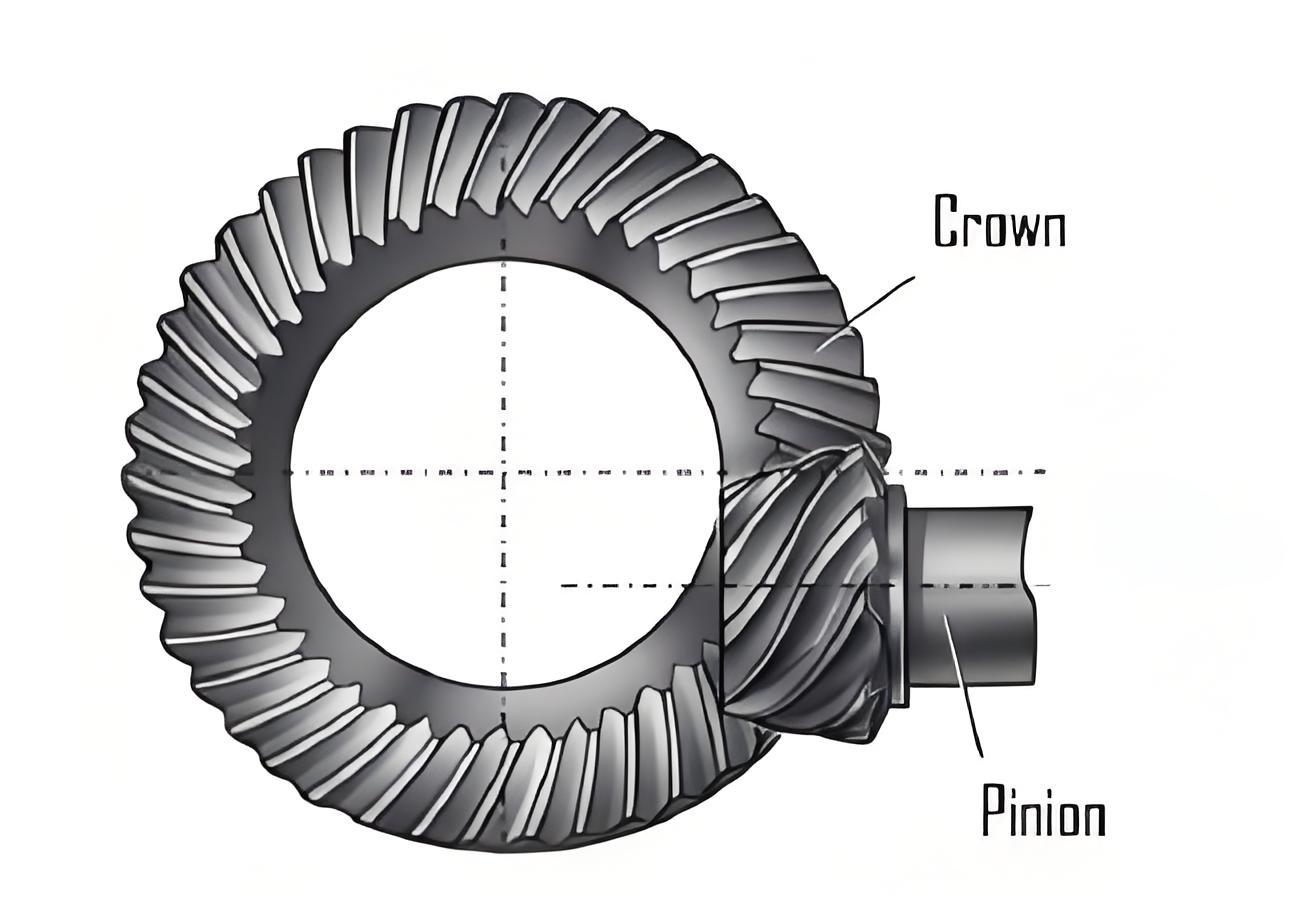
Keywords: hypoid gear; lumped mass method; vibration characteristics; chaotic motion; dynamic performance
1. Introduction
With the trend of lightweighting in the global automotive industry and stringent emission regulations, automotive transmission devices are evolving towards lightweight, high efficiency, low noise, and high reliability. The drive axle, as one of the core components of the micro-vehicle transmission system, bears complex loads and directly affects the vehicle’s safety, comfort, and power performance. In particular, vibration and noise significantly impact the vehicle’s Noise, Vibration, and Harshness (NVH) performance.
2. Literature Review
Previous research on vibration and noise in drive axle gear transmission systems has considered various basic parameters but often neglected some nonlinear time-varying factors. The vibration characteristics have not been thoroughly studied, and some work lacks experimental data. Table 1 summarizes some key research findings in this area.
Author | Key Contributions |
---|---|
Wang et al. | Analyzed the influence of nonlinear supports, stiffnesses, and dynamic forces on gear vibration models. |
Zhu et al. | Conducted meshing contact analysis of hypoid gears and studied the effects of meshing mechanisms and nonlinear excitations. |
Yang et al. | Investigated the effects of mesh stiffness and asymmetry on gear dynamic response considering backlash and asymmetric meshing. |
Wang et al. | Studied the dynamic characteristics of hypoid gears with nonlinear time-varying parameters, revealing the effects of gyroscopic effects, shaft stiffness, and light torque loads. |
Yavuz et al. | Proposed a modal superposition method to study the nonlinear dynamics of multi-gear meshing transmission systems. |
Others | Summarized recent research on gear vibration considering multiple nonlinear factors and analyzed the coupling effects of random parameters. |
3. Vibration Model Establishment
The drive axle gear transmission system’s multi-factor coupling vibration model is established by considering the transmission errors caused by manufacturing and installation, represented by a harmonic function:
em(t)=er0+ersin(2πt/Tc+φ)
where er0 and er are the constant and amplitude of the gear error, respectively; Tc is the gear meshing period; ω is the angular velocity; Z is the number of teeth; and φ is the error phase angle.
4. Dynamic Excitations
The main internal dynamic excitations in the gear meshing process include:
- Impact due to tooth profile errors or uneven tooth surface wear.
- Pulsating forces along the normal line of meshing caused by gear deformation under load.
- Eccentric masses of various rotating parts within the internal system.
5. Vibration Characteristic Analysis
The basic parameters of the transmission components in the drive axle system are shown in Table 2.
Parameter | Value |
---|---|
Input speed | 1500 r/min |
Input torque | 273 N·m |
Time-varying mesh stiffness | Fitted |
Mesh error | Fitted |
Mesh impact | Considered |
By solving the vibration differential equations, the vertical, torsional, and axial vibration values of the driving and driven gears, as well as the vibration characteristics at the centroid of other rotating parts, are obtained.
6. Results and Discussion
6.1. Vibration Characteristics Before and After Modification
The vertical vibration displacement and frequency spectrum of the driving gear before and after modification are shown in Figure 1. The vertical vibration displacement peaks before and after optimization are 13.56 and 7.54 µm, respectively, with a corresponding frequency of 257.8 Hz.
6.2. Influence of External Excitations
The influence of input speed and load torque on the vibration characteristics is analyzed. Figures 2-4 show the vibration displacement, velocity phase diagrams, and acceleration of the driving and driven gears at different input speeds (500, 1000, and 2000 r/min).
The results indicate that:
- The vertical and axial vibrations of the driving and driven gears are more complex than the torsional vibrations.
- Torsional vibrations exhibit quasi-periodic motion.
- Axial vibrations are highly complex, approaching chaotic motion.
- Input speed and load torque have the greatest impact on axial vibrations, followed by vertical vibrations, and the smallest impact on torsional vibrations.
7. Conclusion
This paper conducted a vibration characteristic analysis of the hypoid gear transmission system for a drive axle. By considering various excitations and establishing a multi-variable coupling vibration model, the vibration characteristics of the system were studied. The results show that optimized gear profiles reduce vibration and that input speed and load torque significantly affect axial and vertical vibrations. These findings provide a theoretical basis for subsequent dynamic optimization design, vibration, and noise prediction.