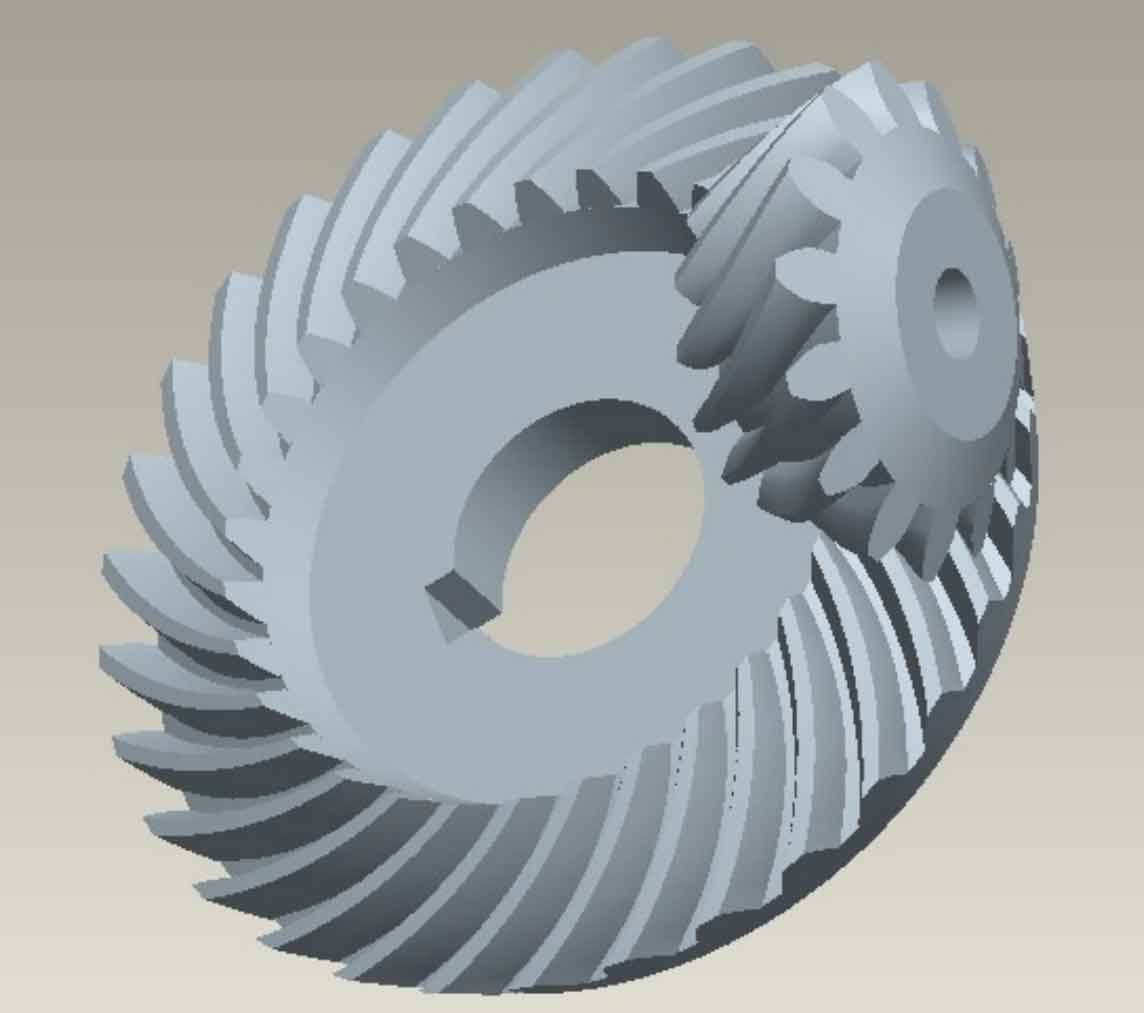
Hypoid gear is widely used in vehicle main reducer. With the development of spiral bevel gear towards high speed and heavy load, strength, vibration and noise have become the bottleneck affecting product quality. The tooth surface of spiral bevel gear is complex, and some achievements have been made in modal analysis, vibration stability and dynamic response. The dynamic model mainly considers the influence of error, time-varying meshing stiffness, backlash, friction and other factors, and the establishment of the dynamic model is mainly based on the force analysis of the reference point, including the pure torsion model, the bending torsion axis coupling model, and the bending torsion axis pendulum coupling model. Based on the theory of multi-body dynamics and the method of hysteretic contact dynamics, a three-dimensional contact dynamic model and dynamic analysis method of spiral bevel gear considering the dynamic contact relationship of the whole tooth surface are proposed. The geometric parameters and stiffness of the meshing position are obtained by combining the tooth surface contact analysis (TCA) and tooth surface load-bearing contact analysis (LTCA). It shows that the multi speed dynamic meshing force of the tooth surface of the spiral bevel gear with high-order transmission error decreases more obviously than that of the tooth surface with second-order transmission error. In fact, it is because the tooth surface adaptation of the high-order transmission error is small, that is, the coincidence degree is large. The above research has contributed to the theoretical research and engineering application of spiral bevel gear dynamics. However, due to the complexity of tooth surface geometry, the research on the vibration and noise reduction technology of spiral bevel gear is still rare.
Tooth surface modification is an effective way to reduce the vibration and noise of gear transmission system. It is widely used in cylindrical gears, and has been deeply studied from the aspects of dynamics and statics. Statics mainly takes the minimum value of load transmission error (ALTE) as the optimization objective, and dynamics mainly takes the minimum root mean square acceleration of meshing line vibration as the optimization objective. When the static performance is optimal, the modification parameters may not make the dynamic performance of the system optimal. It is mainly considered that the modification changes the gear tooth contact clearance and then changes the meshing stiffness excitation, or the stiffness is regarded as a constant. It is mainly considered that the modification changes the gear tooth transmission error to generate the meshing line displacement excitation. Through the comparison with the modification of the finite element method, it shows that the stiffness excitation model is more accurate. It can be seen that the key of dynamic tooth surface modification design is to correctly describe the influence of modification parameters on the meshing stiffness and meshing error of the system. The stiffness model of helical gear modified by slice method is established, the stiffness model of modified spur gear considering the actual motion state is established, and the influence of modification parameters on the vibration response of the system is studied. The stiffness calculation method is only applicable to cylindrical gears with simple tooth surface geometry and their tooth profile modification.
Based on the finite element method, the meshing stiffness and static transmission error of the modified spur gear are obtained, and introduced into the dynamic analysis model to measure the gear modification. The finite element method needs accurate tooth surface model and time-consuming calculation, which is difficult to be popularized in engineering applications. Hypoid gears are machined by using the local conjugate principle, which has embodied the concept of tooth modification. The local synthesis method and the study of high-order transmission error tooth surface have effectively solved the problem of stress concentration at the edge of the tooth surface, but caused excessive mismatch of the gear pair, resulting in the increase of vibration and noise. In order to control the tooth surface modification amount, the relative conjugate tooth surface modification method, namely the tooth surface ease off modification method, has become a research hotspot in the tooth surface design and machining of spiral bevel gears. However, it mainly focuses on the ease off modification tooth surface design with the minimum Alte, the reverse calculation of the processing parameters of the ease off modification tooth surface, the TCA simulation of the ease off modification tooth surface and the simulation verification of the finite element software LTCA. Because of the complexity of the geometry of the ease off modified hypoid gear, it is very difficult to determine the parameters such as the comprehensive error of the tooth surface and the meshing stiffness, and the optimal design of the dynamic vibration reduction modification of the spiral bevel gear is rare.
In order to further improve the quality of automobile drive axle, based on the generation principle of tooth clearance and tooth surface normal clearance, the ease off modification tooth surface design of small wheel is carried out; Combined with TCA and LTCA methods, the comprehensive meshing stiffness of gear teeth is accurately obtained. Based on the force analysis of meshing position, an 8-DOF lumped mass dynamics model of hypoid gear with bending torsion axis coupling is established; Taking the minimum root mean square of normal vibration acceleration as the objective, the optimal ease off modified tooth surface is determined through optimization, and the influence of the stiffness waveform and amplitude change caused by the modification on the dynamic characteristics of the system is discussed.