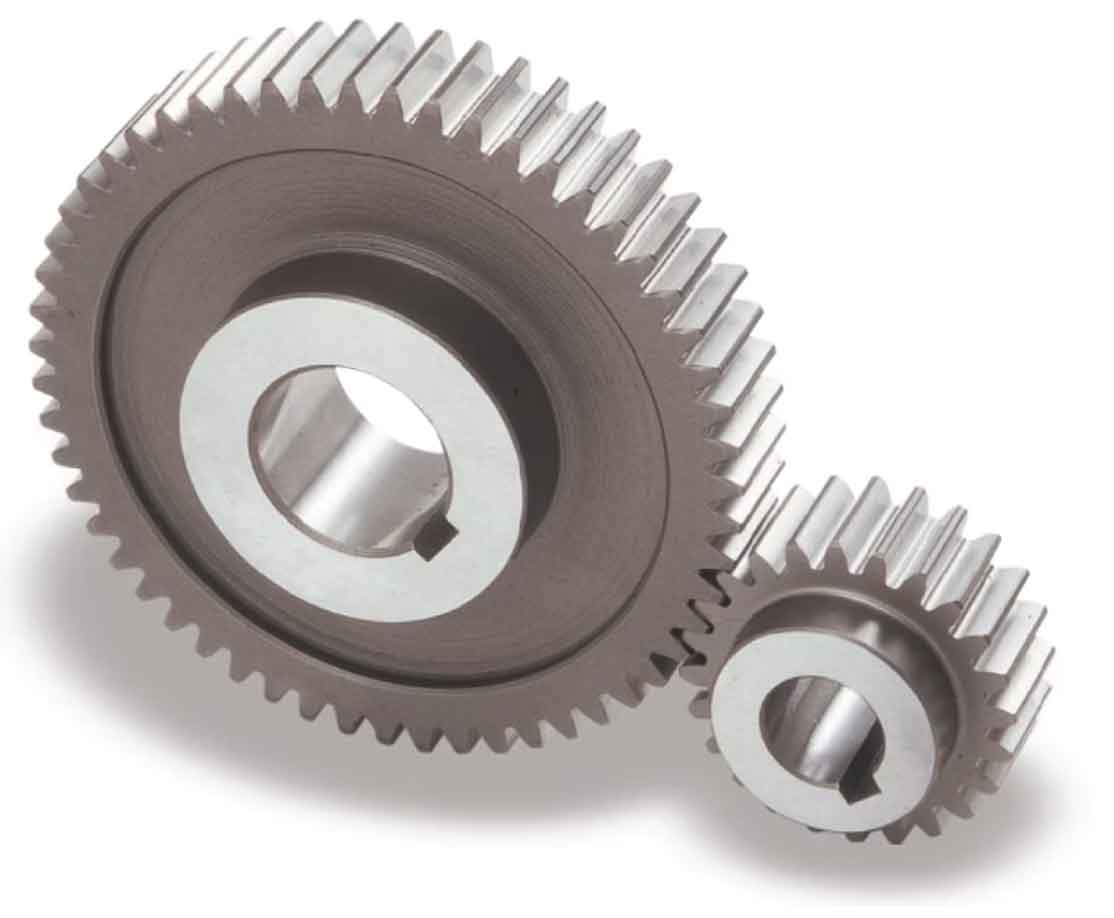
Introduction
Spur gears are one of the most common types of gears used in mechanical systems and machinery. They belong to the category of cylindrical gears, which means their teeth are cut on the surface of a cylinder. These gears have straight teeth that run parallel to the gear’s axis of rotation. They are widely used in various applications due to their simplicity, efficiency, and ease of manufacturing.
Chapter 1 : The Key Features of Spur Gears
Spur gears are a type of cylindrical gears with straight teeth that are parallel to the gear axis. They are one of the most common and straightforward types of gears used for power transmission between parallel shafts. The key features of spur gears include:
- Straight Teeth: Spur gears have straight teeth that are cut perpendicular to the gear’s axis. The teeth run parallel to the gear’s rotational axis, making them easy to manufacture.
- Efficient Power Transmission: Spur gears provide efficient power transmission between parallel shafts, making them suitable for applications where high-speed reduction or increase is not required.
- Constant Speed Ratio: The teeth on spur gears maintain a constant speed ratio, which results in consistent angular velocity between the gear pair.
- Simple Design: The straight teeth and simple construction of spur gears make them easy to design and manufacture, reducing production costs.
- Low Noise: The straight tooth engagement of spur gears results in lower noise levels compared to some other gear types, such as helical gears.
- High Efficiency: Spur gears have relatively high efficiency due to their rolling contact between teeth, resulting in minimal power loss during gear operation.
- Wide Range of Sizes: Spur gears are available in a wide range of sizes, making them versatile for various applications.
- Inexpensive: Spur gears are generally less expensive to produce compared to more complex gear types.
- Axial Thrust: Spur gears may generate axial thrust forces along the gear axis, which need to be properly managed in the gear system’s design.
- Backlash: Spur gears can have backlash, which is the amount of play or clearance between meshing teeth. Backlash can affect the precision and accuracy of gear systems.
- Limited Application for Non-Parallel Shafts: Spur gears are suitable for power transmission between parallel shafts but are not ideal for applications where the shafts intersect or are at an angle to each other.
Spur gears find numerous applications in various industries, including machinery, automotive, appliances, and consumer electronics, where smooth and efficient power transmission is essential. Their simplicity and reliability make them a popular choice for many mechanical systems that require constant speed ratio and moderate load capacity.
Chapter 2 : The Applications of Spur Gears
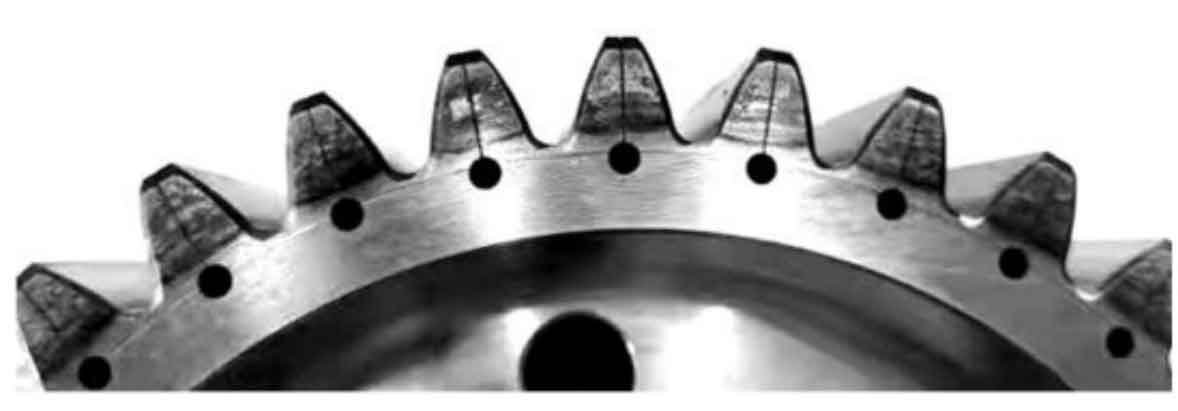
Spur gears are widely used in various applications due to their simplicity, efficiency, and cost-effectiveness. Some common applications of spur gears include:
- Automotive Industry: Spur gears are used in automotive transmissions, differential systems, and power steering mechanisms.
- Industrial Machinery: Spur gears are employed in various industrial machines, including pumps, compressors, conveyors, and machine tools.
- Consumer Electronics: Spur gears can be found in household appliances like washing machines, printers, and scanners.
- Power Tools: Spur gears are used in power tools such as drills, saws, and grinders.
- Clocks and Watches: Spur gears are used in the gear train of mechanical clocks and watches to provide accurate timekeeping.
- Printing Machinery: Spur gears are used in printing machines for paper feed and other mechanical movements.
- Agricultural Equipment: Spur gears are used in agricultural machinery like tractors and combines.
- Robotics: Spur gears are employed in robotics for various motion control and positioning applications.
- Marine Equipment: Spur gears can be found in marine equipment like boat winches and marine engines.
- Medical Devices: Spur gears are used in medical equipment for precise motion control and positioning in medical devices.
- Aviation and Aerospace: Spur gears are used in certain aircraft systems and aerospace equipment.
- Construction Machinery: Spur gears are used in construction equipment such as cranes and excavators.
- Mining Equipment: Spur gears are used in mining machinery like crushers and conveyors.
- Material Handling Equipment: Spur gears are used in material handling equipment such as forklifts and conveyor systems.
- Textile Machinery: Spur gears are employed in textile machinery for various functions like controlling yarn tension and thread guidance.
- Packaging Machinery: Spur gears are used in packaging machinery to control the movement and positioning of packaging materials.
- HVAC Systems: Spur gears can be found in heating, ventilation, and air conditioning (HVAC) systems for fan and blower control.
Spur gears are versatile and can be adapted to a wide range of applications, particularly those requiring simple speed reduction or increase between parallel shafts. Their straightforward design, ease of manufacturing, and reliability make them a popular choice in various industries for power transmission and mechanical motion control.
Chapter 3 : How Spur Gears Work
Spur gears work by transmitting rotational motion and power between two parallel shafts with straight teeth that run perpendicular to the gear’s axis. The teeth of one gear mesh with the teeth of another gear, and when one gear rotates, it causes the other gear to rotate as well. Here’s how spur gears work:
- Meshing of Teeth: Spur gears are placed in close proximity to each other, with their teeth meshing together. The teeth of one gear interlock with the teeth of the other gear.
- Contact Ratio: The contact ratio of spur gears refers to the number of teeth that are in contact at any given time. For spur gears, the contact ratio is typically 1, meaning that only one pair of teeth is in contact at a time.
- Rolling Contact: When the gears are in motion, the teeth of one gear roll over the teeth of the other gear, resulting in rolling contact between the teeth. This rolling contact minimizes friction and wear, making spur gears more efficient.
- Transmission of Motion: As one gear is rotated (called the driver gear), its teeth push against the teeth of the other gear (called the driven gear). This transmission of force causes the driven gear to rotate in the opposite direction of the driver gear.
- Constant Speed Ratio: The teeth of spur gears maintain a constant speed ratio, which means that the angular velocity of the driven gear remains proportional to the angular velocity of the driver gear.
- Direction of Rotation: Spur gears can change the direction of rotation between the driver and driven shafts. For example, if the driver gear rotates clockwise, the driven gear will rotate counterclockwise.
- Backlash: Spur gears may have a small amount of backlash, which is the clearance or play between meshing teeth. Backlash can affect the precision of gear systems and is often minimized in high-precision applications.
- Load Distribution: The teeth of spur gears distribute the load evenly across the teeth, helping to handle high loads and torque.
- Efficiency: Spur gears are relatively efficient due to their rolling contact and simple design.
Spur gears are commonly used in applications where a constant speed ratio, parallel shafts, and simplicity are essential. However, they may generate axial thrust forces, which need to be managed in the gear system’s design. Additionally, the lack of helix angle in spur gears can lead to higher noise levels compared to other gear types, such as helical gears. Nevertheless, spur gears are widely used in various industries for power transmission and mechanical motion control.
Chapter 4 : How Spur Gears are Manufactured
Spur gears are manufactured using various processes, and the specific method depends on factors like the gear size, material, precision requirements, and production volume. Here are some common methods used for manufacturing spur gears:
- Gear Hobbing: Gear hobbing is the most common and efficient method for mass-producing spur gears. In this process, a gear hob (a cutting tool with straight teeth) is used to cut the gear teeth into the gear blank as it rotates. The gear hob’s shape generates the desired tooth profile.
- Gear Shaping: Gear shaping is another popular method for manufacturing spur gears, especially for larger gears or those requiring high precision. In gear shaping, a gear-shaped cutting tool called a shaper cutter is used to generate the gear teeth on the gear blank.
- Gear Milling: Gear milling is a machining process where a gear cutter with straight teeth is used to create spur gear teeth by removing material from the gear blank. Gear milling can be performed on specialized gear milling machines or CNC machining centers.
- Gear Grinding: Gear grinding is used to achieve high precision and surface finish on spur gears after they have been hobbed or shaped. Gear grinding removes any imperfections and ensures precise tooth profiles.
- Broaching: Broaching is a single-pass machining process used to create internal gear teeth in spur gears. A broaching tool with straight teeth is passed through the gear blank, cutting the internal gear teeth in one stroke.
- Lapping: Lapping is used to achieve superior surface finish and high precision on gear teeth. It involves using abrasive particles in a slurry to lap the gear teeth, resulting in smooth and accurate tooth profiles.
- Electrochemical Machining (ECM): ECM is a non-conventional machining process used for high-precision and complex gear profiles. In ECM, an electrically conductive tool and workpiece are immersed in an electrolyte, and material is removed through controlled electrochemical reactions.
- Stamping: For small and simple spur gears, stamping can be an economical method for high-volume production. A metal blank is stamped with a die to create the gear teeth.
- Powder Metallurgy: Powder metallurgy is used to produce spur gears from metal powders by compacting and sintering the powder in the shape of the gear.
The manufacturing process of spur gears requires precision machinery, skilled operators, and often involves post-machining processes such as heat treatment, surface coating, and quality inspection to ensure the gears meet the required specifications. The choice of manufacturing method depends on factors like the gear’s size, complexity, production volume, and required precision.
Chapter 5 : Spur Gear Machining
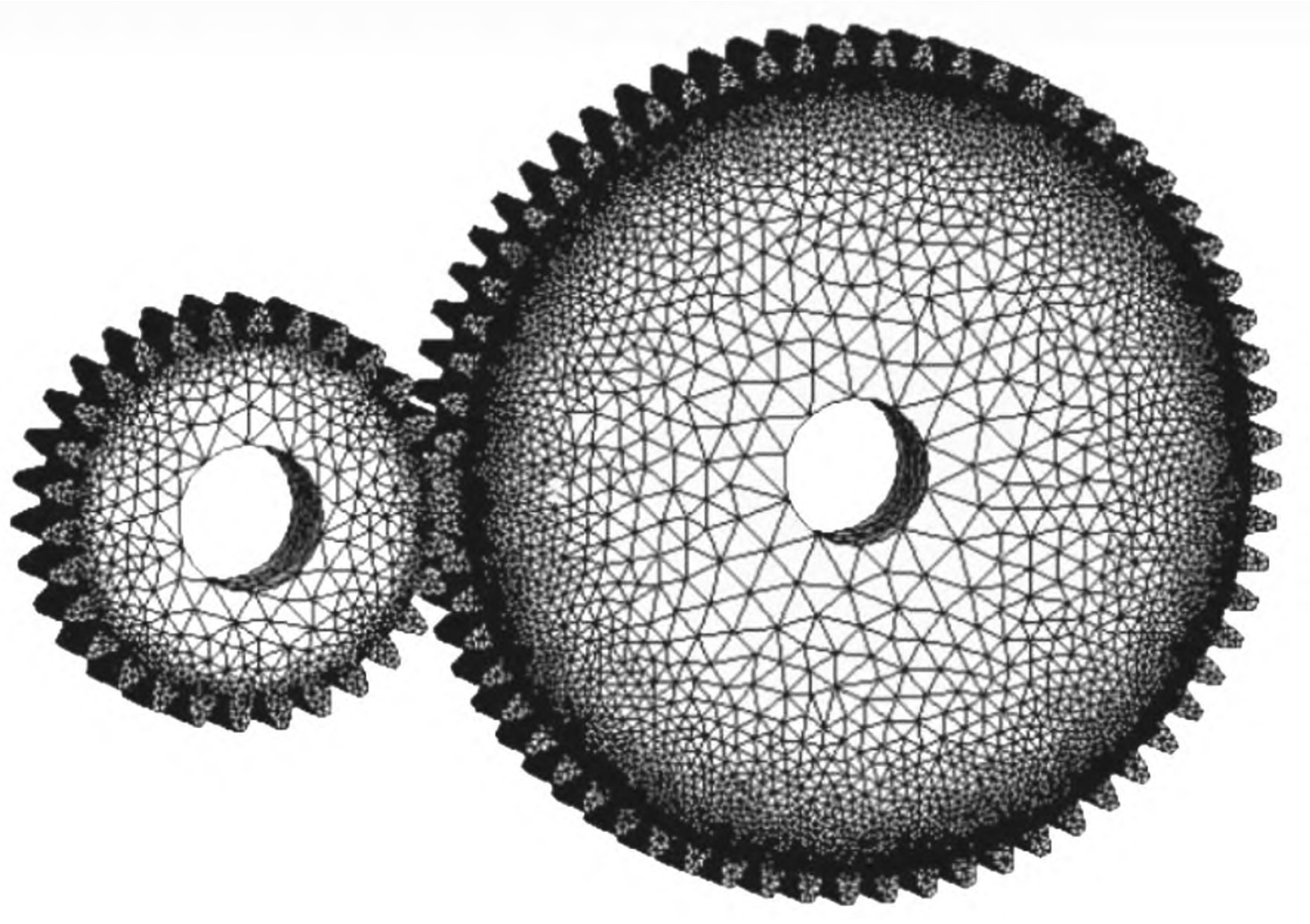
Spur gear machining is the process of producing spur gears using various machining techniques. Spur gears are cylindrical gears with straight teeth that run parallel to the gear axis. The main methods used for spur gear machining are gear hobbing, gear shaping, and gear milling. Here’s an overview of each method:
- Gear Hobbing: Gear hobbing is a widely used method for mass-producing spur gears. In this process, a gear hob (a cutting tool with straight teeth) is used to cut the gear teeth into the gear blank as it rotates. The hob’s helix angle generates the desired tooth profile. Gear hobbing machines can produce spur gears efficiently and accurately in large quantities.
- Gear Shaping: Gear shaping is another common method for manufacturing spur gears, especially for larger gears or those requiring high precision. In gear shaping, a gear-shaped cutting tool called a shaper cutter is used to generate the gear teeth on the gear blank. The shaper cutter reciprocates in a vertical motion to cut the gear teeth one at a time.
- Gear Milling: Gear milling is a machining process where a gear cutter with straight teeth is used to create spur gear teeth by removing material from the gear blank. Gear milling can be performed on specialized gear milling machines or CNC machining centers. It is commonly used for smaller production quantities and for gears with complex tooth profiles.
- Broaching: Broaching is a single-pass machining process used to create internal gear teeth in spur gears. A broaching tool with straight teeth is passed through the gear blank, cutting the internal gear teeth in one stroke. Broaching is suitable for small, high-precision gears.
- Gear Grinding: After the gears have been hobbed, shaped, or milled, gear grinding can be employed to achieve high precision and surface finish. Gear grinding removes any imperfections and ensures precise tooth profiles. Gear grinding is commonly used for gears that require high precision and noise reduction.
Spur gear machining requires skilled operators, precision machinery, and careful quality control to ensure the gears meet the required specifications. Advanced CNC technology has significantly improved the accuracy and repeatability of spur gear machining, allowing for efficient production and high-quality gears. Additionally, post-machining processes such as heat treatment, surface coating, and quality inspection are essential to ensure the gears’ durability and performance.
Chapter 6 : Types of Spur Gears
Spur gears are classified into various types based on their specific features, applications, and designs. Some common types of spur gears include:
- External Spur Gears: These are the most common type of spur gears, where the teeth are located on the outer circumference of the gear. They mesh with other external spur gears or with pinions (small gears) to transmit power between parallel shafts.
- Internal Spur Gears: Internal spur gears have teeth on the inside circumference of the gear. They mesh with other internal gears or pinions to transmit power between parallel shafts with the gear teeth inside the gear.
- Ground Spur Gears: Ground spur gears are precisely machined using gear grinding to achieve high accuracy and surface finish. They are used in applications that require tight tolerances and minimal noise.
- Cast Spur Gears: Cast spur gears are produced by pouring molten metal into a gear mold. They are cost-effective and suitable for applications that do not require high precision.
- Fabricated Spur Gears: Fabricated spur gears are made by cutting and welding individual gear teeth onto a gear blank. They are often used for custom or low-volume applications.
- Hubless Spur Gears: Hubless spur gears have no central hub and are fully flat on both sides. They are used in applications where space constraints are critical.
- Rack and Pinion Gears: A rack is a linear spur gear with teeth along a straight bar, while a pinion is a small spur gear that meshes with the rack. Rack and pinion gears are used to convert rotational motion into linear motion or vice versa.
- Compound Spur Gears: Compound spur gears have two or more sets of teeth with different diameters on the same gear. They allow for different gear ratios and are used in some automotive applications.
- Ring Gears: Ring gears are large external spur gears with teeth on the inside circumference. They are often used in applications such as planetary gear systems.
- Gear Racks: Gear racks are long, straight spur gears with teeth along their length. They are used with pinion gears to convert rotational motion into linear motion.
Each type of spur gear has its specific advantages and applications. The selection of the appropriate type depends on factors such as load requirements, space limitations, precision needs, and cost considerations.
Chapter 7 : The Advantages and Disadvantages of Spur Gears
Spur gears offer several advantages and disadvantages, which make them suitable for certain applications while limiting their use in others. Here are the key advantages and disadvantages of spur gears:
Advantages:
- Simple Design: Spur gears have a straightforward design with straight teeth running parallel to the gear axis, making them easy to manufacture and assemble.
- Efficient Power Transmission: Spur gears provide efficient power transmission between parallel shafts, making them suitable for applications where high-speed reduction or increase is not required.
- Constant Speed Ratio: The teeth of spur gears maintain a constant speed ratio, resulting in consistent angular velocity between the gear pair.
- Wide Range of Sizes: Spur gears are available in a wide range of sizes, making them versatile for various applications.
- Inexpensive: Spur gears are generally less expensive to produce compared to more complex gear types.
- High Torque Capacity: Spur gears can handle high torque loads due to the larger contact area between the teeth.
- Low Noise: The straight tooth engagement of spur gears results in lower noise levels compared to some other gear types, such as helical gears.
- Axial Space Efficiency: Spur gears have compact axial dimensions, making them suitable for applications with limited space.
Disadvantages:
- Axial Thrust: Spur gears may generate axial thrust forces along the gear axis, which need to be properly managed in the gear system’s design.
- Backlash: Spur gears can have backlash, which is the amount of play or clearance between meshing teeth. Backlash can affect the precision and accuracy of gear systems.
- Noisy at High Speeds: At high speeds, spur gears can produce significant noise and vibration due to the abrupt tooth engagement.
- Limited Application for Non-Parallel Shafts: Spur gears are suitable for power transmission between parallel shafts but are not ideal for applications where the shafts intersect or are at an angle to each other.
- Limited Load Distribution: Spur gears distribute load over a small number of teeth at a time, leading to higher stress concentration in some applications.
- Limited Speed Reduction Ratio: Spur gears are not well-suited for high-speed reduction applications due to the noise and wear that can occur at high rotational speeds.
Despite their limitations, spur gears are widely used in various industries for power transmission and mechanical motion control where constant speed ratio and moderate load capacity are required. Careful consideration of the application requirements and gear design can help mitigate some of the disadvantages and make the most of the advantages offered by spur gears.
Chapter 8 : The Applications of Spur Gears
Spur gears find applications in a wide range of industries and mechanical systems due to their simplicity, efficiency, and versatility. Some common applications of spur gears include:
- Automotive Industry: Spur gears are used in automotive transmissions, differential systems, and steering mechanisms.
- Industrial Machinery: Spur gears are employed in various industrial machines, including pumps, compressors, conveyors, and machine tools.
- Consumer Electronics: Spur gears can be found in household appliances like washing machines, printers, and scanners.
- Power Tools: Spur gears are used in power tools such as drills, saws, and grinders.
- Clocks and Watches: Spur gears are used in the gear train of mechanical clocks and watches to provide accurate timekeeping.
- Printing Machinery: Spur gears are used in printing machines for paper feed and other mechanical movements.
- Agricultural Equipment: Spur gears are used in agricultural machinery like tractors and combines.
- Robotics: Spur gears are employed in robotics for various motion control and positioning applications.
- Marine Equipment: Spur gears can be found in marine equipment like boat winches and marine engines.
- Medical Devices: Spur gears are used in medical equipment for precise motion control and positioning in medical devices.
- Aviation and Aerospace: Spur gears are used in certain aircraft systems and aerospace equipment.
- Construction Machinery: Spur gears are used in construction equipment such as cranes and excavators.
- Mining Equipment: Spur gears are used in mining machinery like crushers and conveyors.
- Material Handling Equipment: Spur gears are used in material handling equipment such as forklifts and conveyor systems.
- Textile Machinery: Spur gears are employed in textile machinery for various functions like controlling yarn tension and thread guidance.
- Packaging Machinery: Spur gears are used in packaging machinery to control the movement and positioning of packaging materials.
- HVAC Systems: Spur gears can be found in heating, ventilation, and air conditioning (HVAC) systems for fan and blower control.
Spur gears are versatile and can be adapted to a wide range of applications, particularly those requiring simple speed reduction or increase between parallel shafts. Their straightforward design, ease of manufacturing, and reliability make them a popular choice in various industries for power transmission and mechanical motion control.