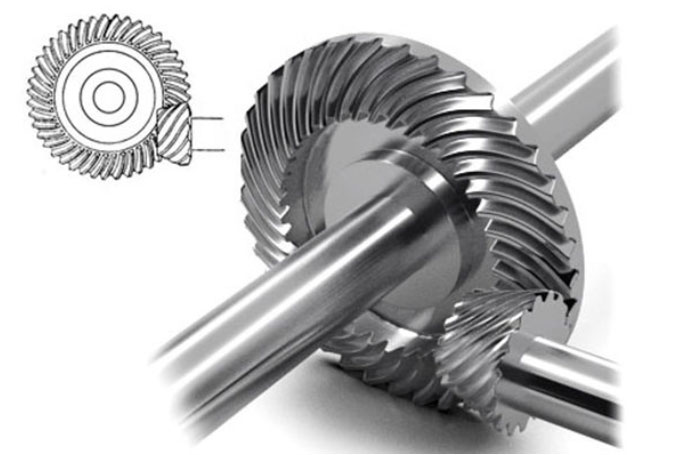
Hypoid gears are chosen in various applications when specific performance requirements and operating conditions call for their unique characteristics. Here are some situations when and why hypoid gears may be selected:
- High Torque Applications: Hypoid gears are capable of transmitting high torque due to their large contact area and optimized tooth profiles. They are often chosen in applications where high torque is required, such as in heavy-duty machinery, industrial equipment, and automotive drivetrains.
- Space Constraints: Hypoid gears offer a compact design compared to other gear types, making them suitable for applications with limited space. Their offset pinion design allows for a more compact and efficient gear arrangement, making them valuable in applications where space optimization is crucial.
- High-Speed Applications: Hypoid gears can handle high rotational speeds due to their improved tooth engagement and reduced sliding friction compared to other bevel gear types. They are commonly used in applications that require both high torque and high speed, such as power transmission systems and automotive differentials.
- Noise and Vibration Reduction: Hypoid gears exhibit smoother operation with reduced noise and vibration levels compared to straight bevel gears. The offset pinion and unique tooth geometry contribute to improved tooth contact and reduced sliding action, resulting in quieter gear operation. They are often preferred in applications where noise reduction is essential, such as automotive drivetrains and industrial gearboxes.
- Axial Load Capability: Hypoid gears can handle significant axial loads due to their offset pinion design and optimized contact pattern. This makes them suitable for applications that experience both radial and axial loads, such as rear differentials in automobiles and heavy machinery.
- Gearbox Efficiency: Hypoid gears can provide higher overall gearbox efficiency compared to other gear types, thanks to their optimized tooth geometry and reduced sliding friction. This efficiency improvement translates into energy savings, reduced heat generation, and improved system performance.
When selecting hypoid gears, it is essential to consider factors such as torque requirements, speed range, space constraints, noise considerations, axial load capacity, and overall system efficiency. Additionally, it’s crucial to collaborate with gear manufacturers or engineering experts who can provide guidance and ensure that the selected hypoid gears meet the specific application requirements.