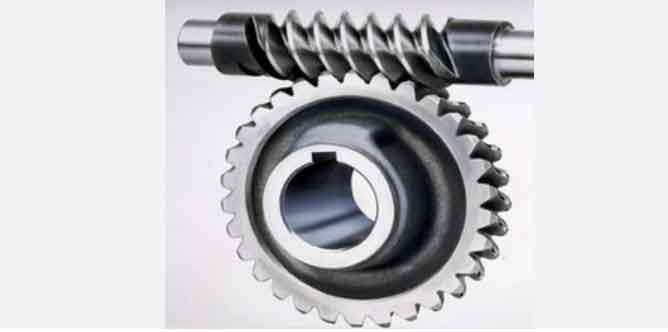
Worm gears are a type of mechanical power transmission system that have been used for centuries to transmit rotational motion between non-intersecting shafts. Despite their ancient origins, worm gears remain a highly effective and widely used technology in modern engineering. Here are the basics of worm gears:
1. Worm Gear Components:
A worm gear system consists of two main components:
- Worm: The worm is a cylindrical gear with a screw-like thread called the helix. It is typically driven by a motor or another power source.
- Worm Wheel (Gear): The worm wheel, also known as the worm gear, is a toothed wheel that meshes with the helical thread of the worm. It is connected to the driven shaft and transmits rotational motion.
2. Helical Design:
The key feature of worm gears is their helical design, which consists of a continuous thread wrapped around the worm. This helical configuration enables the worm gear to transmit motion at a right angle to the axis of the worm. The helix angle determines the lead of the worm, which affects the gear ratio and efficiency of the system.
3. High Gear Ratio: One of the primary advantages of worm gears is their ability to achieve high gear ratios in a compact form. A single worm gear system can have a relatively large gear ratio, making it useful for reducing rotational speed while increasing torque. This property makes worm gears ideal for applications where significant speed reduction is required.
4. Self-Locking Feature:
Worm gears possess a self-locking property, meaning that the worm can prevent the worm wheel from turning the worm back. This characteristic provides inherent braking and holding capabilities, which are useful in applications requiring load holding and safety functions.
5. Efficiency Considerations:
While worm gears offer high gear ratios, they generally exhibit lower efficiency compared to other gear types due to sliding friction between the worm and the worm wheel. However, advancements in materials and lubrication have improved their efficiency in modern applications.
6. Applications:
Worm gears find widespread use in various industries and applications, including:
- Automotive steering systems
- Conveyor systems
- Lifts and elevators
- Machine tools
- Packaging machinery
- Robotics
7. Lubrication and Maintenance:
Proper lubrication is critical for worm gear systems to reduce friction and wear. Regular maintenance, such as checking for wear, proper alignment, and lubrication, ensures the optimal performance and longevity of the system.
Worm gears remain an essential and effective power transmission system, offering distinct advantages in specific applications. Their unique design and self-locking feature make them invaluable in scenarios where precise motion control, high gear ratios, and load holding capabilities are required.