When selecting the right gear type for your application, it is important to consider the specific requirements and constraints. Worm gears offer unique advantages and characteristics that differentiate them from other gear types. Let’s compare worm gears with some other commonly used gear types to help you make an informed decision:
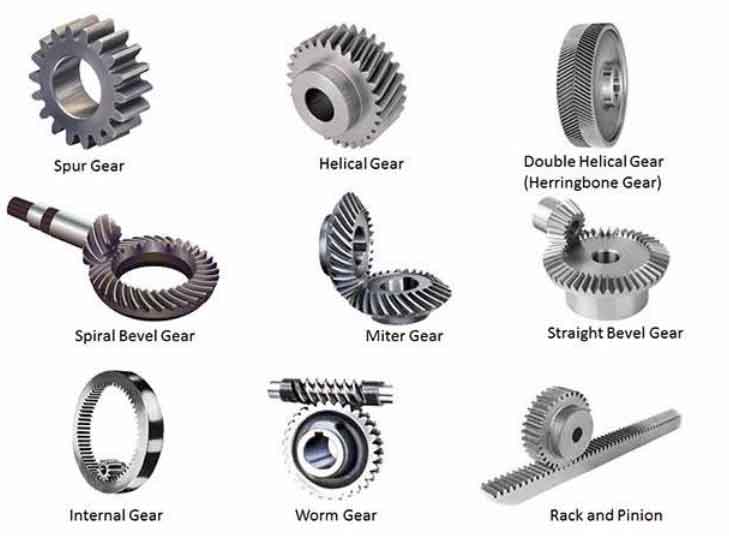
- Worm Gears vs. Spur Gears:
- Gear Reduction: Worm gears provide high gear reduction ratios, making them suitable for applications requiring significant speed reduction. Spur gears, on the other hand, typically offer lower gear reduction ratios.
- Self-Locking: Worm gears have a self-locking capability, meaning they resist back-driving and can hold a load in position without the need for additional braking mechanisms. Spur gears do not have inherent self-locking properties.
- Compactness: Worm gears have a compact design, often requiring less axial space compared to spur gears.
- Efficiency: Spur gears generally have higher efficiency due to their rolling contact, whereas worm gears have sliding contact, leading to slightly lower efficiency.
- Worm Gears vs. Helical Gears:
- Gear Reduction: Similar to worm gears, helical gears can provide high gear reduction ratios, but worm gears often have higher ratios.
- Efficiency: Helical gears typically have higher efficiency compared to worm gears due to their rolling contact and improved load distribution across the tooth profile.
- Noise and Vibration: Helical gears operate with less noise and vibration compared to worm gears due to their helical tooth engagement, which results in a smoother meshing action.
- Backlash: Helical gears generally have more backlash compared to worm gears, which can impact precision and positioning accuracy.
- Worm Gears vs. Bevel Gears:
- Power Transmission: Worm gears are suitable for transmitting power between non-parallel and perpendicular shafts, while bevel gears are commonly used for power transmission between intersecting shafts.
- Gear Ratio Range: Worm gears typically offer higher gear reduction ratios than bevel gears.
- Efficiency: Bevel gears generally have higher efficiency due to their rolling contact, while worm gears have sliding contact and lower efficiency.
- Backlash: Bevel gears typically have less backlash compared to worm gears.
- Worm Gears vs. Planetary Gears:
- Gear Reduction: Planetary gears offer a wide range of gear reduction ratios, similar to worm gears.
- Efficiency: Planetary gears can achieve higher efficiencies compared to worm gears due to their rolling contact and multiple gear meshings.
- Compactness: Planetary gears have a more compact design compared to worm gears, as they offer multiple gear stages within a single housing.
- Load Distribution: Worm gears distribute the load over a larger surface area compared to planetary gears, which can be advantageous for certain applications.
Ultimately, the choice between worm gears and other gear types depends on factors such as the required gear reduction ratio, self-locking capability, compactness, efficiency, noise level, backlash tolerance, and specific application requirements. It is important to carefully evaluate these factors and consult with gear engineering experts to select the most suitable gear type for your application.