When it comes to choosing the right gear solution for a particular application, it’s essential to consider various factors such as torque requirements, efficiency, speed, noise, and space constraints. Worm gears are one type of gear that offers distinct advantages and disadvantages compared to other gear types. Let’s compare worm gears with some other common gear types to help you make an informed decision.
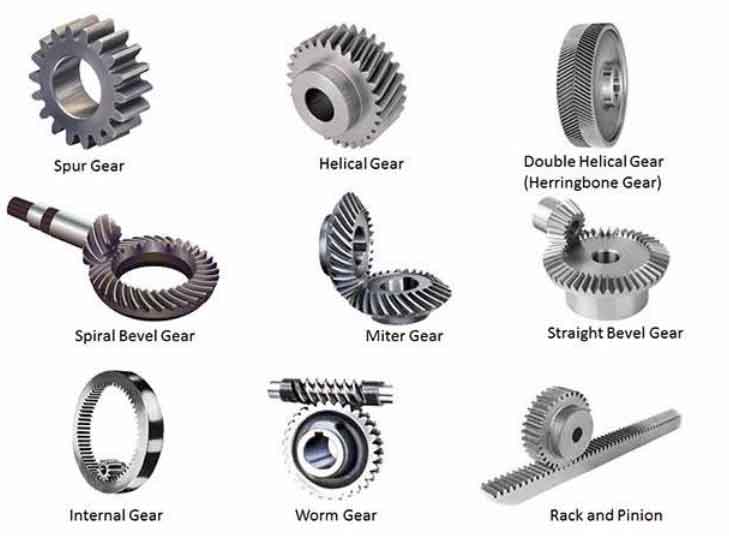
- Spur Gears: Spur gears are the simplest and most common type of gear. They have straight teeth that are parallel to the gear’s axis. Spur gears are highly efficient and offer high-speed capabilities. However, they produce more noise compared to worm gears due to their teeth engagement characteristics. They are suitable for applications that require high-speed rotation and moderate torque.
- Helical Gears: Helical gears have angled teeth that are not parallel to the gear axis. This angled tooth design allows for smooth and gradual tooth engagement, resulting in reduced noise and vibration compared to spur gears. Helical gears offer high efficiency and are capable of handling high loads. They are commonly used in industrial machinery and automotive applications.
- Bevel Gears: Bevel gears are used when the direction of rotation needs to change. They have conical-shaped teeth and are commonly used in applications where power transmission is required between intersecting shafts. Bevel gears are durable, compact, and capable of transmitting high torque. However, they may not be as efficient as spur or helical gears.
Now, let’s focus on worm gears and their unique characteristics:
- High Gear Ratio: Worm gears offer high gear reduction ratios, allowing for large speed reductions in a single stage. This makes them suitable for applications where a high reduction ratio is required, such as in heavy machinery and conveyor systems.
- Compact Design: Worm gears have a compact design, which makes them suitable for applications with limited space.
- Self-Locking: Worm gears have a self-locking property, meaning the worm can hold its position without requiring a brake or additional locking mechanism. This makes them useful in applications where the load needs to be held in position when the driving force is removed.
However, there are some considerations to keep in mind when using worm gears:
- Lower Efficiency: Worm gears are generally less efficient compared to other gear types. This is due to the sliding action between the worm and the gear, which results in higher friction and energy losses. If efficiency is a critical factor for your application, you may want to consider other gear types.
- Limited Speed: Worm gears typically operate at lower speeds compared to other gears due to the sliding contact between the worm and the gear. High-speed applications may require alternative gear solutions.
- Axial Thrust: Worm gears generate significant axial thrust due to the helical angle of the worm. This thrust needs to be properly managed, especially when dealing with large loads.
In summary, worm gears offer unique advantages such as high gear ratios, compact design, and self-locking capabilities. However, they may have lower efficiency, limited speed capabilities, and generate axial thrust. Consider the specific requirements of your application, including torque, speed, space limitations, and the need for self-locking or high reduction ratios, to determine if worm gears are the right solution or if another gear type would be more suitable.