Worm gears and rack and pinion systems are two popular gear types used in various mechanical applications. While both serve the purpose of converting rotational motion into linear motion (or vice versa), they have distinct characteristics and advantages. Let’s analyze and compare them in terms of their design, operation, efficiency, applications, and considerations.
- Design and Operation:
- Worm Gears: A worm gear consists of a threaded cylindrical gear (the worm) that meshes with a toothed gear (the worm wheel or worm gear). The worm is typically driven by a motor, while the worm wheel is connected to the driven mechanism. The motion is transferred between the axes at a right angle. Worm gears can achieve high gear ratios, making them suitable for speed reduction applications.
- Rack and Pinion: A rack and pinion system consists of a linear toothed rack and a pinion gear. The rack is a straight bar with teeth running along its length, while the pinion is a small gear meshing with the rack. The pinion is driven by a motor, causing the rack to move linearly. Rack and pinion systems provide direct linear motion and are commonly used in applications requiring high speed and precise positioning.
- Efficiency:
- Worm Gears: Worm gears often exhibit lower efficiency compared to rack and pinion systems. This is due to the sliding action between the worm and worm wheel, which introduces more friction and potential energy losses. The efficiency can vary depending on factors such as the helix angle, gear quality, lubrication, and load conditions.
- Rack and Pinion: Rack and pinion systems generally offer higher efficiency because they operate through rolling contact between the teeth. This rolling action reduces friction and improves power transmission efficiency. With proper lubrication and well-matched components, rack and pinion systems can achieve high efficiency levels.
- Applications:
- Worm Gears: Worm gears are commonly used in applications that require high gear reduction ratios and torque transmission. They are often found in machinery such as lifts, conveyor systems, winches, and automotive steering systems. Their ability to provide significant speed reduction makes them suitable for applications where precise control and high torque are required.
- Rack and Pinion: Rack and pinion systems find widespread use in various applications, including steering mechanisms in vehicles, CNC machines, robotics, linear actuators, and many industrial automation systems. They excel in applications that demand precise linear motion, high speed, and compact design.
- Considerations:
- Backdriveability: Rack and pinion systems are typically backdriveable, meaning the driven load can drive the pinion and generate rotational motion. This feature can be advantageous in certain applications, such as manual adjustments or safety mechanisms. In contrast, worm gears are usually not backdriveable without additional mechanisms to prevent reverse motion.
- Precision and Reversibility: Rack and pinion systems provide accurate and reversible linear motion, which is advantageous in applications that require precise positioning or bidirectional movement. Worm gears may have a slight degree of non-reversibility due to the self-locking nature of the gear arrangement, which can be advantageous in applications where preventing backdriving is desired.
- Space Constraints: Worm gears offer compact designs due to their high gear reduction capabilities. They can achieve substantial speed reduction in a small package. Rack and pinion systems, on the other hand, require more space due to the linear nature of their motion.
Both worm gears and rack and pinion systems have their unique characteristics and applications. Worm gears excel in high torque and speed reduction applications, while rack and pinion systems offer precise linear motion and high efficiency. Choosing the appropriate gear type depends on the specific requirements of the application, including speed, torque, positional accuracy, reversibility, and cost considerations. It is essential to carefully evaluate these factors to select the most suitable gear type for a given application.
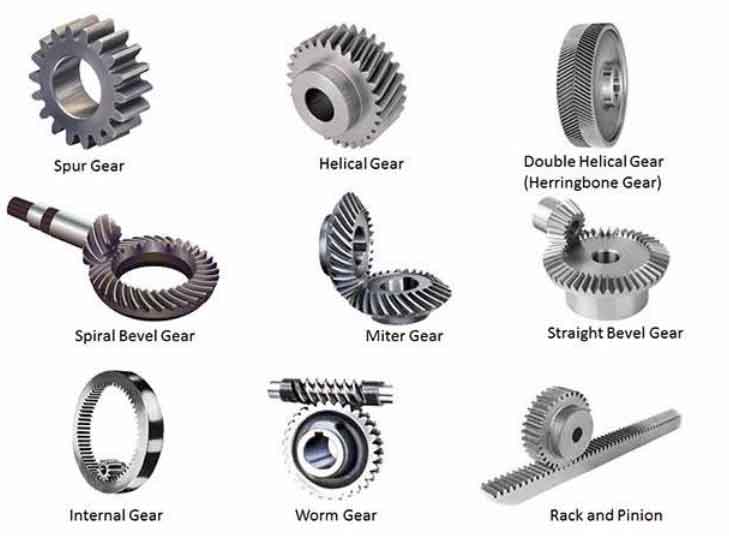
When deciding between worm gears and rack and pinion systems, consider the following:
- Speed and Torque Requirements: If the application requires significant speed reduction and high torque transmission, a worm gear may be more suitable. Worm gears can achieve high gear ratios, allowing for powerful torque output. Rack and pinion systems, on the other hand, are better suited for applications that demand high linear speed and precise positioning.
- Efficiency: If efficiency is a critical factor, rack and pinion systems generally offer higher efficiency due to their rolling action. However, it’s important to consider the specific gear design, quality, and operating conditions to accurately assess efficiency levels.
- Precision and Reversibility: Rack and pinion systems provide accurate linear motion and bidirectional movement, making them ideal for applications that require precise positioning and reversible motion. If precision and reversibility are important factors, a rack and pinion system would be a better choice. However, if preventing backdriving is desired, a worm gear’s self-locking nature can be advantageous.
- Space Constraints: Consider the available space for the gear system. If the application has limited space and requires a high gear reduction ratio, a compact worm gear design might be more suitable. Rack and pinion systems require more space due to their linear motion.
- Backdriveability: If the application requires the driven load to backdrive the gear system, such as in manual adjustments or safety mechanisms, a rack and pinion system’s backdriveability can be advantageous. Worm gears generally require additional mechanisms to prevent reverse motion.
- Cost: Cost considerations are vital when selecting a gear type. Worm gears tend to be more expensive due to their complex design and manufacturing process. Rack and pinion systems are often more cost-effective, especially for simpler applications.
Ultimately, the choice between worm gears and rack and pinion systems depends on the specific requirements of the application, including speed, torque, precision, space limitations, backdriveability, and cost. Careful analysis of these factors will help determine the most appropriate gear type for optimal performance and efficiency.