Worm gears and spiral gears are two different types of gears that are used in various applications. While both serve the purpose of transmitting rotational motion between two shafts, they have distinct design features and functional characteristics. Let’s compare worm gears and spiral gears in terms of their design, efficiency, load capacity, backlash, and applications.
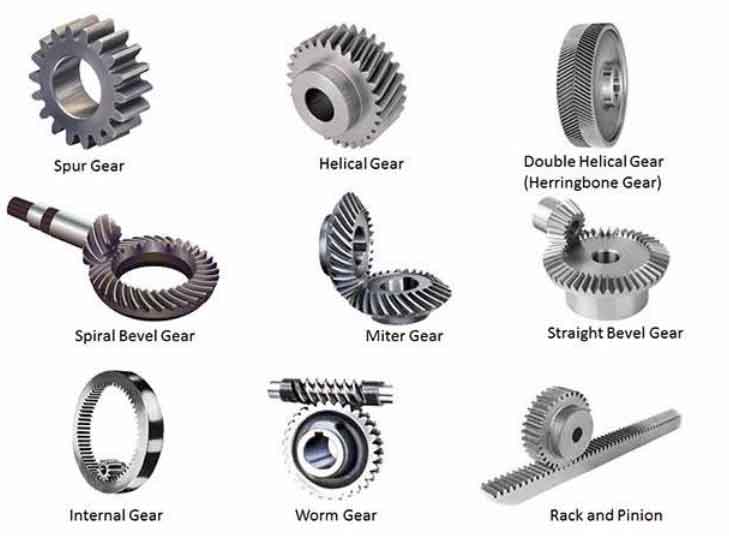
- Design:
- Worm Gears: A worm gear consists of a screw-like gear called the worm and a toothed wheel called the worm wheel or worm gear. The worm has a helical thread that meshes with the teeth of the worm wheel. The worm typically has one tooth, resulting in a large gear reduction ratio.
- Spiral Gears: Spiral gears, also known as helical gears, have angled teeth that are cut in a helical pattern around the gear. This helix angle allows for gradual tooth engagement, resulting in smoother and quieter operation compared to straight-cut gears.
- Efficiency:
- Worm Gears: Worm gears are known for their high gear reduction ratios, making them suitable for applications where a large speed reduction is required. However, due to the sliding action between the worm and the worm wheel, worm gears tend to have lower efficiency compared to other gear types.
- Spiral Gears: Spiral gears offer higher efficiency compared to worm gears. The gradual tooth engagement and increased tooth contact area minimize sliding friction and improve power transmission efficiency.
- Load Capacity:
- Worm Gears: Worm gears can handle high loads because the load is distributed over multiple teeth along the length of the worm wheel. They have excellent load-carrying capabilities and are often used in heavy-duty applications.
- Spiral Gears: Spiral gears also have good load-carrying capacity, although they may not be able to handle the same level of loads as worm gears. However, their higher efficiency can compensate for the reduced load capacity in many applications.
- Backlash:
- Worm Gears: Worm gears typically have more backlash compared to spiral gears. Backlash refers to the slight play or clearance between the mating teeth of the gears, which can result in a loss of precision in motion transfer.
- Spiral Gears: Spiral gears can be designed to minimize backlash due to their helical tooth profile. This makes them suitable for applications that require accurate positioning and reduced backlash, such as in precision machinery and robotics.
- Applications:
- Worm Gears: Worm gears find applications in various industries, including automotive, industrial machinery, conveyors, and lifts. They are commonly used in situations where high gear reduction ratios, high torque transmission, and self-locking capabilities are required.
- Spiral Gears: Spiral gears are widely used in automotive transmissions, machine tools, gear pumps, and other applications where smooth operation, high efficiency, and moderate torque transmission are important.
Worm gears and spiral gears have different design features and performance characteristics. Worm gears excel in high reduction ratio applications with heavy loads and self-locking capabilities but may have lower efficiency and increased backlash. Spiral gears offer higher efficiency, smoother operation, and reduced backlash, making them suitable for applications that require precision and moderate torque transmission. The choice between these gear types depends on the specific requirements of the application and the trade-offs between factors such as load capacity, efficiency, backlash, and cost.