Abstract
This article delves into the research and application of the YKA2260 Full-CNC Spiral Bevel Gear Milling Machine, highlighting its significance in breaking international technological monopolies and elevating China’s high-end CNC equipment manufacturing capabilities. The article utilizes tables, images, and technical descriptions to fully demonstrate the machine’s performance, technical innovations, and application effects.
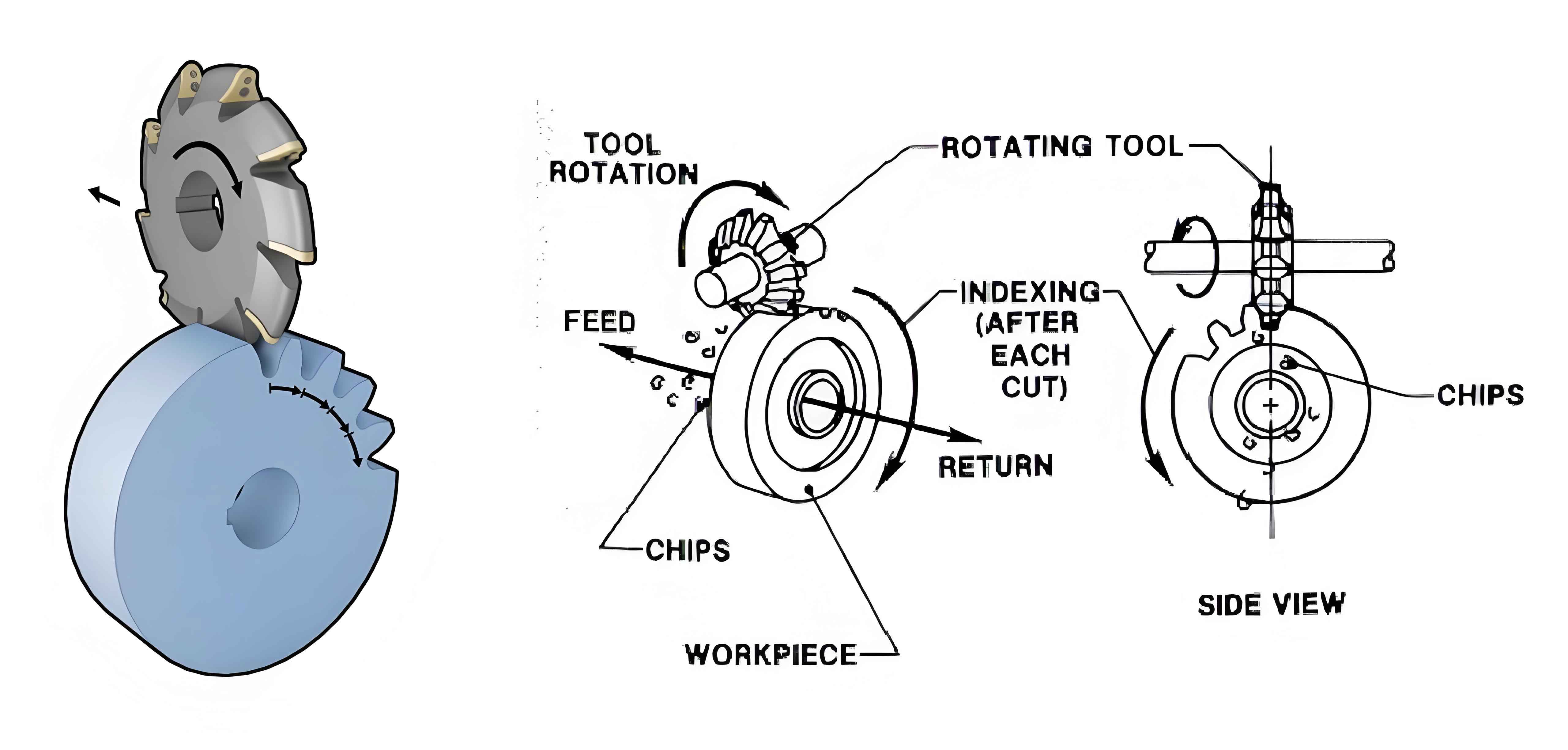
1. Introduction
The drive axle is a crucial component for light vehicles, micro-cars, heavy trucks, large buses, and construction machinery, directly providing driving force to the vehicle. Spiral bevel gears, as the core parts of the drive axle, significantly impact the working performance of the drive axle and thus the overall vehicle dynamics. With the vigorous development of the automotive industry, there is an increasing demand for high-efficiency, high-precision spiral bevel gear processing equipment and complete sets of technologies, along with demands for low-cost and environmentally friendly processing methods. The ability to process spiral bevel gears with high efficiency and precision determines the economic benefits and market position of the automotive industry, and even has a vital impact on China’s comprehensive national strength.
Currently, the international automotive drive axle spiral gear manufacturing industry普遍 adopts high-end CNC machines for dry cutting, offering advantages such as high efficiency, high precision, low cost, and environmental friendliness. However, the majority of spiral gear processing in China still relies on mechanical machines for wet cutting, characterized by high costs, high pollution, and low precision.
China urgently needed dry cutting production lines for automotive spiral bevel gears, which were mostly imported from Klingelnberg or Gleason, consuming huge amounts of foreign exchange and making the development of China’s automotive industry subject to technological monopolies from developed countries. But in 2012, the first domestic full-CNC spiral bevel gear milling machine—YKA2260—successfully came off the production line at Hunan Zhongda Chuangyuan CNC Equipment Co., Ltd., marking the localization of bevel gear dry cutting equipment and breaking the international technological blockade and monopoly.
Table 1: Summary of Domestic and Foreign Dry Cutting Equipment
Manufacturer Name | Equipment Name | Maximum Processing Diameter (mm) |
---|---|---|
Germany Klingelnberg | C27 | 270 |
Germany Klingelnberg | C30 | 300 |
Germany Klingelnberg | C50 | 500 |
USA Gleason | 280HC | 280 |
USA Gleason | 600HC | 600 |
Zhongda Chuangyuan | CY15C | 150 |
Zhongda Chuangyuan | YKA2235 | 350 |
Zhongda Chuangyuan | YKA2260 | 600 |
2. Product Performance Introduction
The YKA2260 is a six-axis, six-simultaneous-motion, dry/wet cutting dual-purpose full-function machine capable of high-rigidity, high-precision, and high-efficiency processing of various spiral bevel gears and hypoid gears with extended outer cycloid teeth and arcuate contracted teeth.
Under normal machining conditions, the milling accuracy reaches Grade 5 according to the accuracy standards for bevel gears and hypoid gears specified in GB11365-89, with a tooth surface roughness of Ra1.6μm.
Technical Features:
- Vertical structure.
- Tool spindle and workpiece spindle driven directly by high-torque motors.
- Self-designed and developed dry cutting tool disc.
- Machine capable of milling extended outer cycloid teeth and arcuate contracted teeth spiral bevel gears.
- High-speed dry cutting function.
- 6-axis simultaneous motion CNC machine, utilizing Siemens 840D SL CNC system.
- Equipped with spiral bevel gear HCS machining control software integrated into the 840D SL CNC system.
- Full closed-loop control mode with high-precision linear gratings for all linear axes and high-precision angular encoders for all rotary axes.
- Automatic door opening and closing function.
- Small footprint.
- Especially suitable for mass production of spiral bevel gears for passenger and commercial vehicles.
- Convenient tool disc loading and unloading.
- Infinitely adjustable milling speed.
- Machine adopts disc spring clamping and hydraulic release clamping system with clamping detection function.
- Automatic tool setting and milling allowance distribution function.
- Fault prompt with help system.
- Comprehensive safety protection (including emergency retraction, power-off retraction, power protection, temperature protection, etc.).
- Equipped with an automatic loading and unloading system for fully automatic processing without attendance.
Table 2: Main Technical Parameters
Specification Name | Unit | Value |
---|---|---|
Milling Tool Disc Specification | Φ(7.5~18)"R(88~200)mm | |
Machined Parts | Maximum Gear Ratio | 10:1 |
Maximum End Face Modulus | mm | 14 |
Teeth Number | 5~200 | |
Maximum Pitch Diameter | mm | 600 |
Stroke | X-axis Stroke | mm |
Y-axis Stroke | mm | 0~-220 |
Z-axis Stroke | mm | +200~+640 |
B-axis Stroke | ° | ±90 |
Machine Total Power | kW | 120 |
Net Weight | kg | 35,000 |
Total Footprint (including Material Bin) | mm | 7700×5930 |
3. Application of New Technologies
3.1 Structural Design
Due to the large cutting volume, high tool linear speed, and the absence of cutting fluid cooling in high-speed dry cutting, the machine is required to have high static stiffness, dynamic stiffness, and thermal stiffness. The machine does not accumulate iron chips and has fast chip removal, quickly discharging the high temperature on the iron chips from the machine. The high processing accuracy and tooth surface quality of the YKA2260 are attributed to its high dynamic accuracy and thermal compensation function equipped on the spindle. The machine also has the following advantages:
- Small gantry structure with high stiffness, simple structure, and total machine accuracy not easily disturbed.
- Both spindles are suspended, with no components below the processing space, allowing chips to fall directly into the chip conveyor for quick removal, reducing thermal deformation of the machine column.
- To control tooth surface errors, the machine must have high dynamic performance. The YKA2260 workpiece spindle and tool spindle both adopt a direct drive structure with high-torque motors, and each axis is equipped with Heidenhain high-precision gratings for real-time position feedback and closed-loop control by the Siemens 840DSL CNC system.
- Zero-distance loading and unloading with convenient tool changes.
- Easy observation of the machining point.
3.2 Research and Application of Machine Thermal Balance Design Technology
During the machine design stage, heat generation from heat sources is reduced, and heat dissipation of the system is enhanced. Based on the optimal design theory of machine thermal characteristics, the design scheme is theoretically evaluated to achieve the design goal of reducing machine thermal errors. During the manufacturing and use of the machine, thermal errors of the system are compensated.
Technical Route Feasibility and Specific Implementation Plan for Machine Thermal Balance Design:
- Research on Reducing Spindle System Heat Generation
- Main measures include minimizing intermediate transmission links, shortening the transmission chain length to zero by directly adopting built-in motor electric spindles, and adopting permanent magnet spindle motors to reduce rotor heat generation compared to induction motors.
- Constant temperature water cooling is applied to the permanent magnet motor to ensure the motor temperature does not vary with load changes.
- Research on Reasonable Lubrication Methods
- Although experiments show that the temperature rise of bearings using oil-air lubrication is 5~8℃ lower than that using grease lubrication and 9~16℃ lower than that using oil mist lubrication, the cooling effect becomes more significant as the value increases.
- Simultaneously, ensuring constant motor cooling water flow, maintaining constant motor temperature, and appropriately increasing the compressed air flow rate of the spindle axial air seal achieves stable spindle temperature.