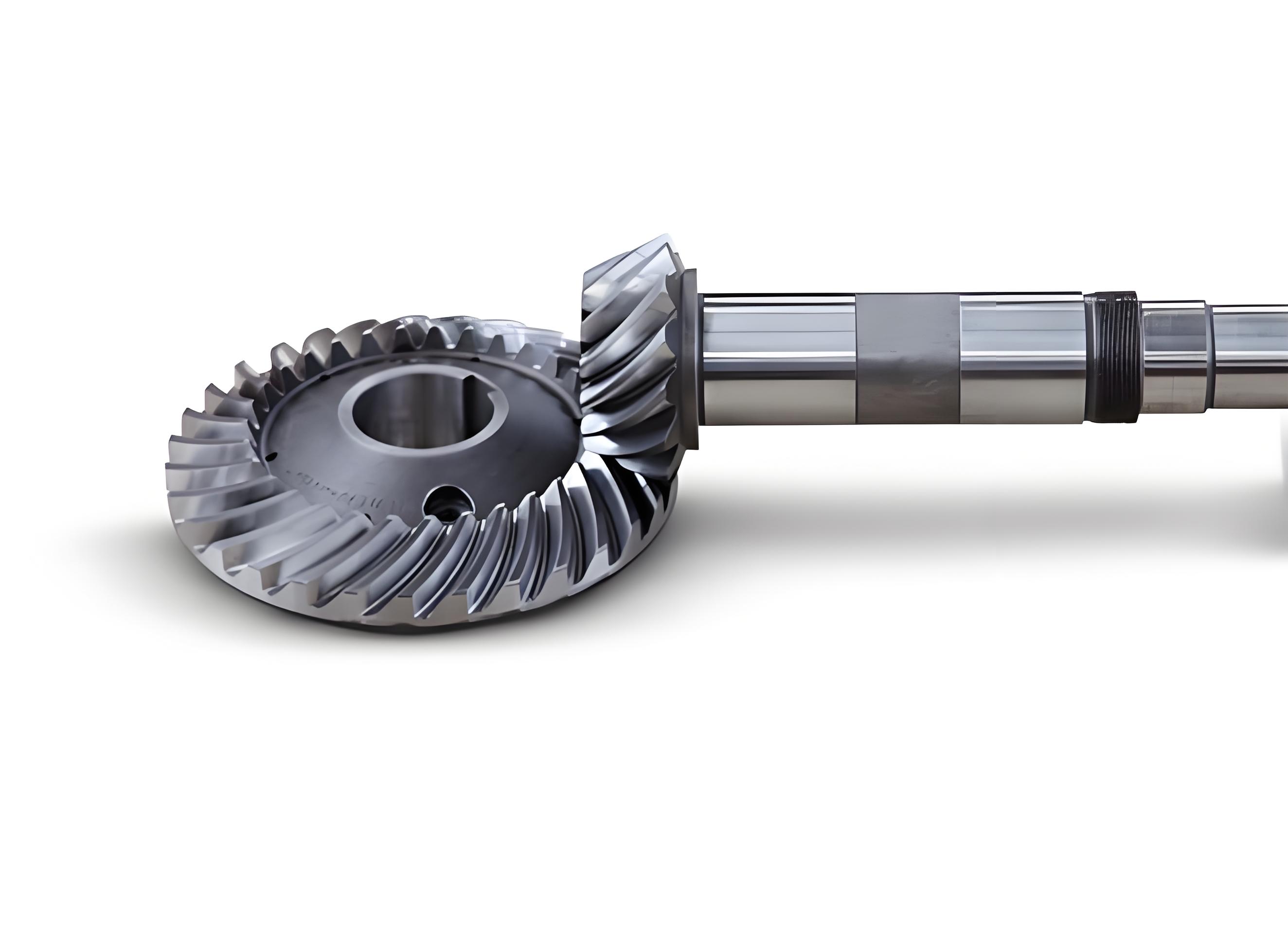
Abstract
Additive manufacturing (AM), including 3D printing, offers innovative solutions for producing custom spiral bevel gear with enhanced performance, reduced lead times, and increased design flexibility. This review explores the applications, benefits, and challenges of using additive manufacturing techniques in the production of custom spiral bevel gear.
Introduction
The complexity and precision required for manufacturing spiral bevel gear make traditional manufacturing methods time-consuming and expensive. Additive manufacturing provides an alternative approach that allows for rapid prototyping, customization, and production of complex geometries. This review examines how AM technologies are applied in the design and production of custom spiral bevel gear, focusing on material choices, process advantages, and potential challenges.
Additive Manufacturing Technologies
- Selective Laser Melting (SLM)
- Process: Uses a high-power laser to fuse metal powder layer by layer to create complex geometries.
- Benefits: High precision and the ability to produce intricate details and internal structures.
- Applications: Custom spiral bevel gear with optimized weight and strength properties.
- Electron Beam Melting (EBM)
- Process: Utilizes an electron beam to melt and fuse metal powder in a vacuum.
- Benefits: Suitable for high-performance materials like titanium and Inconel, offering excellent mechanical properties.
- Applications: Aerospace and high-stress applications requiring robust spiral bevel gear.
- Fused Deposition Modeling (FDM)
- Process: Extrudes thermoplastic filaments layer by layer to form the desired shape.
- Benefits: Cost-effective for prototyping and producing spiral bevel gear from engineering-grade thermoplastics.
- Applications: Rapid prototyping and low-load applications where metal spiral bevel gear is not necessary.
- Stereolithography (SLA)
- Process: Uses a UV laser to cure liquid resin into solid layers.
- Benefits: High resolution and smooth surface finish, ideal for detailed prototypes.
- Applications: Prototyping and manufacturing of spiral bevel gear requiring high precision.
Applications in Custom Spiral Bevel Gear Manufacturing
- Rapid Prototyping
- Advantages: AM allows for the quick production of spiral bevel gear prototypes, enabling faster design iterations and testing.
- Outcome: Reduces the time and cost associated with developing new spiral bevel gear designs.
- Complex Geometry
- Capabilities: AM can produce complex internal structures and optimized geometries that are challenging for traditional methods.
- Outcome: Enhances spiral bevel gear performance through weight reduction and improved load distribution.
- Material Efficiency
- Reduction in Waste: AM processes are more material-efficient, reducing waste compared to subtractive manufacturing methods.
- Outcome: Lower material costs and a more sustainable production process.
- Customization
- Flexibility: AM allows for the customization of spiral bevel gear to meet specific application requirements, including unique sizes, shapes, and material compositions.
- Outcome: Provides tailored solutions for specialized applications in automotive, aerospace, and industrial machinery.
Material Selection
- Metals
- Common Metals: Stainless steel, titanium, aluminum, and Inconel.
- Properties: High strength, durability, and wear resistance suitable for high-stress applications.
- Polymers
- Engineering Plastics: Nylon, polycarbonate, and PEEK.
- Properties: Lightweight, corrosion-resistant, and suitable for lower-load applications or prototyping.
- Composites
- Fiber-Reinforced Polymers: Carbon fiber or glass fiber reinforcements.
- Properties: Enhanced mechanical properties, reduced weight, and improved performance in specific applications.
Challenges and Solutions
- Surface Finish and Accuracy
- Challenge: AM parts often require post-processing to achieve the desired surface finish and dimensional accuracy.
- Solution: Implementing post-processing techniques such as CNC machining, polishing, and heat treatment to refine spiral bevel gear surface and dimensions.
- Material Properties
- Challenge: Ensuring the mechanical properties of AM spiral bevel gear meet the standards required for high-performance applications.
- Solution: Utilizing advanced materials and optimizing process parameters to achieve consistent and reliable material properties.
- Cost
- Challenge: The initial cost of AM equipment and materials can be high.
- Solution: Focusing on long-term cost savings through reduced lead times, material efficiency, and the ability to produce complex designs that would be cost-prohibitive with traditional methods.
- Scalability
- Challenge: Scaling up production for large quantities can be challenging with current AM technologies.
- Solution: Combining AM for prototyping and custom parts with traditional manufacturing for high-volume production.
Case Studies
- Automotive Prototyping
- Application: Custom spiral bevel gear prototypes for transmission systems.
- Outcome: Faster development cycles and improved design validation.
- Aerospace Components
- Application: Lightweight, high-strength spiral bevel gear for aircraft and spacecraft.
- Outcome: Enhanced performance and fuel efficiency due to weight reduction.
- Industrial Machinery
- Application: Custom spiral bevel gear for specialized machinery requiring unique geometries.
- Outcome: Improved machinery performance and reduced downtime due to tailored spiral bevel gear designs.
Conclusion
Additive manufacturing offers significant advantages in the production of custom spiral bevel gear, including design flexibility, material efficiency, and rapid prototyping. While challenges such as surface finish, material properties, and scalability exist, ongoing advancements in AM technologies and materials continue to expand the possibilities for custom spiral bevel gear manufacturing. The integration of AM in spiral bevel gear production can lead to innovative designs and improved performance across various industries.
References
- Journal of Manufacturing Processes: Research on additive manufacturing techniques and their applications in spiral bevel gear production.
- Additive Manufacturing Journal: Articles on the materials and methods used in 3D printing for mechanical components.
- Precision Engineering: Studies on the accuracy and surface finish of AM parts and post-processing methods.
- Materials Science and Engineering: Papers on the mechanical properties and performance of AM-produced spiral bevel gears.
This review provides a comprehensive overview of the applications and benefits of additive manufacturing in the production of custom spiral bevel gear, offering valuable insights for engineers, researchers, and industry professionals.