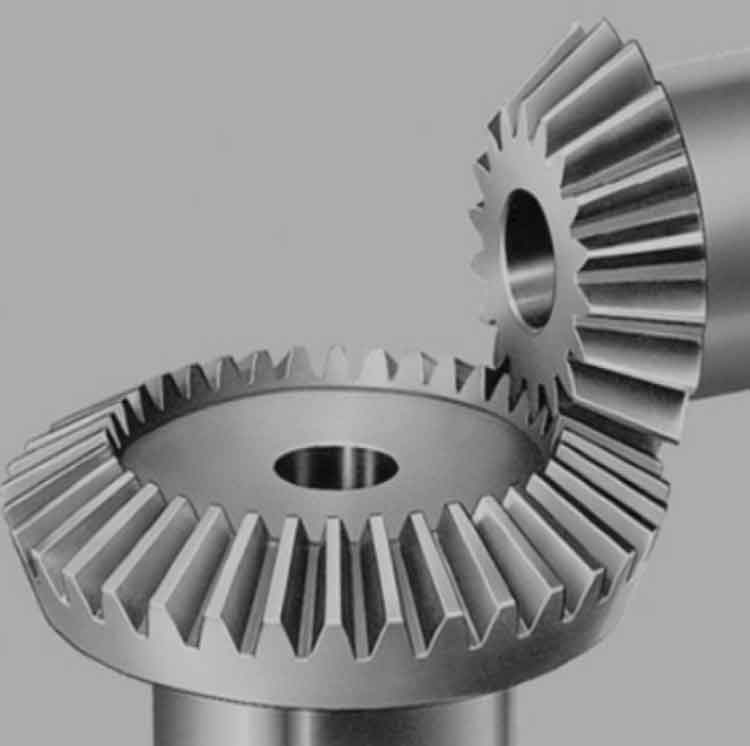
Straight bevel gears, with their conical shape and straight teeth, are crucial components in various mechanical systems, providing efficient torque transmission between intersecting shafts. Recent advancements in their design have significantly enhanced their performance, making them suitable for high-performance applications. This guide explores these advancements, focusing on materials, manufacturing processes, computational design, and application-specific innovations.
1. Material Innovations
High-Strength Alloys:
- Advanced Steel Alloys: The development of high-strength, low-alloy steels with improved fatigue and wear resistance has increased the durability of straight bevel gears.
- Heat-Treated Alloys: Advanced heat treatment processes, such as carburizing and nitriding, enhance surface hardness while maintaining a tough core, improving overall gear performance.
Composite Materials:
- Fiber-Reinforced Composites: The use of composites like carbon fiber-reinforced polymers offers a lightweight alternative with excellent strength-to-weight ratios, reducing inertia and improving efficiency in high-speed applications.
Ceramic Coatings:
- Surface Coatings: Ceramic coatings applied to gear surfaces provide exceptional wear resistance and reduce friction, extending the gear’s lifespan and reliability in high-stress environments.
2. Manufacturing Advances
Precision Machining:
- CNC Machining: High-precision computer numerical control (CNC) machining allows for the production of gears with tighter tolerances, reducing noise and improving efficiency.
- Additive Manufacturing: 3D printing and additive manufacturing techniques enable complex gear geometries and customized designs, which were previously difficult or impossible to achieve with traditional methods.
Enhanced Gear Grinding:
- High-Accuracy Grinding: Advances in gear grinding technologies, including the use of advanced abrasives and computer-controlled processes, result in smoother gear surfaces and higher precision.
Automated Inspection:
- In-Line Metrology: Real-time, automated inspection systems ensure consistent quality and precision during the manufacturing process, reducing defects and enhancing performance.
3. Computational Design Improvements
Finite Element Analysis (FEA):
- Stress Analysis: FEA allows for detailed stress and strain analysis, optimizing gear geometry to minimize stress concentrations and enhance load distribution.
- Thermal Analysis: Thermal simulations predict temperature distributions during operation, aiding in the design of gears that can withstand thermal stresses.
Optimization Algorithms:
- Topology Optimization: Computational algorithms optimize material distribution within the gear, reducing weight while maintaining strength and performance.
- Multi-Objective Optimization: Advanced algorithms balance multiple performance criteria, such as strength, noise, and efficiency, to achieve the best overall gear design.
Dynamic Simulation:
- Vibration Analysis: Dynamic simulations help predict and mitigate vibration and noise, enhancing the performance and longevity of the gear system.
- Load Distribution: Simulations of load distribution across the gear teeth ensure even wear and reduce the risk of gear failure.
4. Application-Specific Innovations
Automotive Applications:
- High-Performance Drivetrains: Advanced straight bevel gears are being integrated into high-performance automotive drivetrains, providing smoother, more efficient power transmission.
- Electric Vehicles (EVs): Lightweight, high-strength gears are critical for improving the efficiency and range of electric vehicles, where reducing weight and maximizing performance are paramount.
Aerospace Applications:
- Weight Reduction: The use of lightweight materials and optimized designs reduces the weight of aerospace gear systems, enhancing fuel efficiency and payload capacity.
- High-Temperature Performance: Advanced materials and coatings enable gears to operate reliably in the extreme temperature conditions of aerospace environments.
Industrial Machinery:
- Heavy-Duty Applications: In industrial settings, high-strength materials and precision manufacturing ensure gears can handle high loads and harsh operating conditions.
- Robotics: The demand for precision and reliability in robotics has driven the development of gears with minimal backlash and high positional accuracy.
5. Case Studies and Real-World Applications
Automotive Performance:
- Racing Vehicles: In racing applications, straight bevel gears made from high-strength alloys and precision machined to exact tolerances provide the reliability and performance needed for competitive racing.
Aerospace Efficiency:
- Aircraft Gearboxes: Advanced straight bevel gears in aircraft gearboxes contribute to improved fuel efficiency and reduced maintenance costs, critical for commercial aviation.
Industrial Robustness:
- Mining Equipment: In mining equipment, robust straight bevel gears withstand high torque and heavy loads, ensuring operational reliability and reducing downtime.
Conclusion
The advancements in straight bevel gear design, driven by innovations in materials, manufacturing processes, computational design, and application-specific requirements, have significantly enhanced their performance in high-performance applications. By leveraging these advancements, industries ranging from automotive to aerospace and industrial machinery can achieve greater efficiency, reliability, and performance in their gear systems. As technology continues to evolve, we can expect further improvements in straight bevel gear design, pushing the boundaries of what these critical components can achieve.