Therefore, in recent years, the application of plastic forming technology to replace the traditional mechanical cutting methods has been paid more and more attention. Precision forming technology overcomes the shortcomings of low material utilization and low productivity in cutting processing technology, especially the low strength caused by cutting off the metal streamline. It has become one of the main methods of gear processing reform with its high efficiency and high precision.
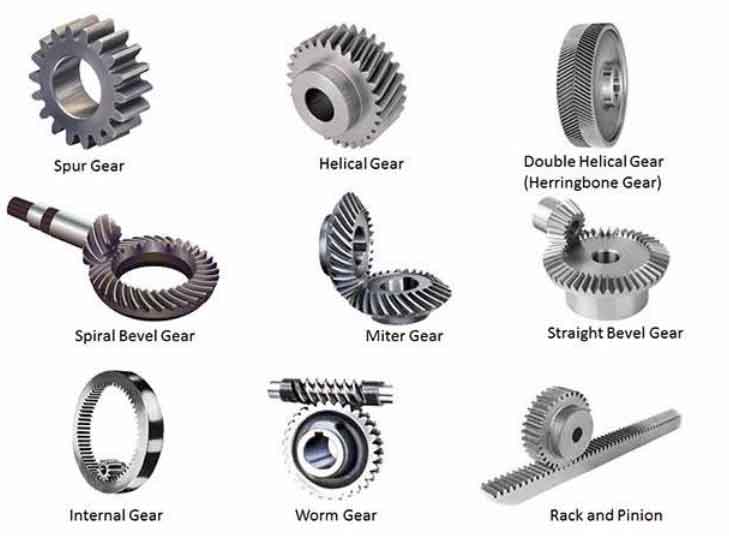
As an advanced manufacturing technology, precision forming technology is gradually developed on the basis of traditional die forging technology. At present, the generally accepted definition of precision forming process is “at least the dimensional accuracy and shape accuracy of some surfaces of forgings can be directly used for assembly or can be assembled only by grinding”.
Using precision forming technology to produce gear parts not only has the significant advantages of material saving, energy saving, reducing machining processes and working hours, low cost and high efficiency, but also can greatly improve the internal and appearance quality of products, which is in line with the development trend of advanced manufacturing technology in the century of high efficiency, precision, green and clean. Straight bevel gear is widely used in machine production. The traditional bevel gear processing method is produced by metal cutting, which not only wastes raw materials, but also has low productivity. At present, precision die forging technology is widely used at home and abroad instead of metal cutting, which greatly improves the strength, bending fatigue life and productivity of bevel gear, and reduces the production cost.
However, there are also some problems in precision die forging process, such as many processes, strict control of heating temperature during hot forging and warm forging, not too much oxide scale on forgings, and precision forging is not suitable for small batch production. The precision forming of bevel gear by cold rotary forging is an advanced gear processing technology adopted in recent years. The process can not only avoid various disadvantages caused by heating during hot forging, but also overcome the disadvantages of excessive deformation resistance and low die life during ordinary cold forging. Moreover, the use of cold rotary forging saves the heating equipment and related energy consumption. Due to the reasonable distribution of metal fibers in rotary forging parts and the strengthening in the process of rotary forging, the mechanical properties of finished parts are greatly improved, and the machining accuracy and surface finish can also be greatly improved. Therefore, cold rotary forging precision forming technology has broad application prospects in the field of gear processing.