In the fields of aerospace vehicles, high-speed and heavy-duty spiral bevel gears, as the key of the transmission system, have strict requirements on its load-bearing capacity, contact performance, dynamic characteristics and reliability. With the development of modern machinery in the direction of high power to weight ratio, the load transmitted in the system increases, and the problems of vibration and noise become more prominent. During the operation of high-speed and heavy-duty spiral bevel gears, the important factors causing vibration and noise are the actual coincidence degree and transmission error. Improving the design coincidence directly improves the transmission error and dynamic behavior of high-speed and heavy-duty spiral bevel gear pairs, and the transmission error is used as the excitation factor of the transmission system. Therefore, the tooth surface design with high coincidence and low transmission error amplitude will significantly improve the stability and load distribution between teeth of high-speed and heavy-duty spiral bevel gear transmission, and can obtain good dynamic characteristics, meshing characteristics and strength performance at the same time.
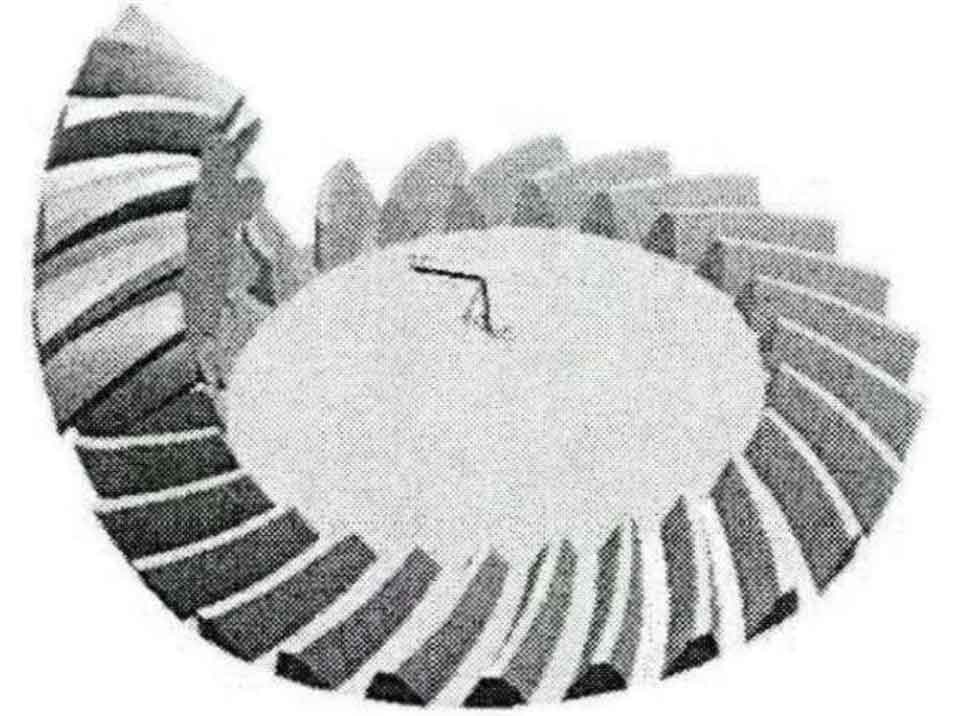
The traditional spiral bevel gear tooth surface design is based on the “local conjugate principle”, and the meshing performance of the tooth surface is controlled by Gleason adjustment card and tooth trial cutting. Independent of the traditional design method, Professor Litvin proposed the “local synthesis method”, which can make up for the lack of pre controlling the meshing characteristic parameters in the traditional design. First, the second-order contact parameters of three tooth surfaces are preset, and the basic equations of line contact (tool tooth surface and machined tooth surface) and point contact (two-phase meshing tooth surface) between two surfaces are established by the differential geometry theory, Finally, the adjustment parameters of large wheel gear cutting are pushed back to the adjustment parameters of small wheel gear cutting. The high-speed and heavy-duty spiral bevel gear pair designed by this method can effectively control the first-order and second-order contact performance at the reference point of the tooth surface. Professor Fang Zongde and his team introduced the local synthesis method for China, and on this basis, the meshing quality of high-speed and heavy-duty spiral bevel gears is controlled as a whole by optimizing the optional processing parameters. Deng Xiaozhong and other experts and scholars combined TCA and LTCA technologies to give a design method to improve the coincidence degree of high-speed and heavy-duty spiral bevel gears, so as to improve the strength of high-speed and heavy-duty spiral bevel gears and achieve the purpose of vibration and noise reduction of transmission system. Caixiangwei proposed a modification method of the variable coefficient of high-order transmission error. Through numerical simulation, it is verified that the transmission error of high-order design can significantly improve the strength performance and dynamic characteristics of high-speed and heavy-duty spiral bevel gear pairs, and the transmission error of side reflection of high-order design can improve the design coincidence of high-speed and heavy-duty spiral bevel gear pairs. Mou Yanming et al. Combined with ease off technology and based on tooth length curvature correction, designed the target tooth surface, reduced the fluctuation amplitude of high-order transmission error, and effectively improved the load distribution and meshing performance of high-speed and heavy-duty spiral bevel gear pairs. Su Chengfa et al. Proved that the contact path design along the tooth length direction can improve the coincidence degree and avoid the premature edge contact of teeth.
Combined with TCA, LTCA and other technologies, based on the local synthesis method, a multi-objective optimization design model for the transmission error amplitude at the high coincidence and low meshing conversion is established. The second-order contact parameters of three tooth surfaces are optimized by using NSGA-II algorithm to obtain the Pareto optimal solution set, and a relatively appropriate non inferior solution is selected according to the importance of the objective function. Finally, taking a pair of high-speed and heavy-duty spiral bevel gears as an example, through numerical simulation, the meshing performance and strength performance of high-speed and heavy-duty spiral bevel gears before and after optimization are compared and analyzed to verify the rationality of the optimization results and achieve the effect of vibration and noise reduction.