According to the requirements of the national driving axle fatigue test standard qc/t 533-1999, the test bench as shown in Figure 1 (a) is built, the input load is 1598nm, and the speed of the bench test is 481rpm according to the basic parameters of the vehicle. During the operation, the oil temperature is controlled at 85-120 ° C. here, the oil temperature is controlled by water cooling. The installation method is shown in Fig. 1 (b). The cooling water pipe is arranged on the main speed reducer of the tested bridge, and the lubricating oil temperature is controlled by adjusting the opening of the tap.
In order to monitor the abnormal vibration of the drive axle caused by early fatigue cracks during the test, an acceleration sensor is arranged on the drive axle. Before the test, the drive axle shall be run in according to 1 / 4 load, 1 / 2 load, 3 / 4 load and full load respectively. The running time is 6000 wheel cycles corresponding to the vehicle. Bench test shall be conducted on the drive axle after running in.
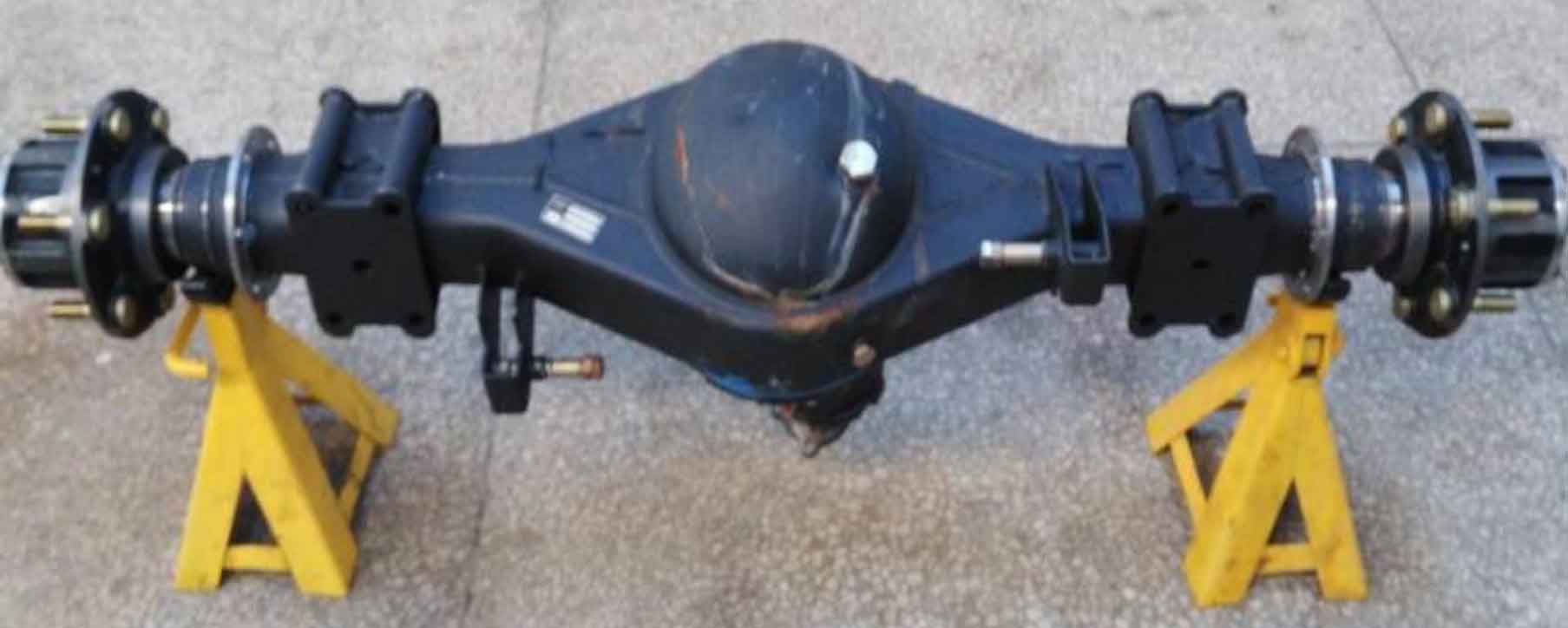
During the first test of the drive axle, it was damaged after 200000 times of operation. As shown in Figure 2, the appearance of the drive axle assembly was not damaged. As shown in figures 3 and 4, the final fatigue failure forms of the large and small wheels of the hypoid gear were respectively shown. The fatigue failure of the large wheel of the hypoid gear near the small end and the first failure of the small wheel of the hypoid gear at the big end, which was the same as the trend predicted by the stress distribution of the tooth root. The fatigue times of hypoid gears in this test were 200000 times, which did not meet the standard requirements for 500000 times, and the predicted value was 1.05 times the test value. According to the same test method, the Fatigue Bench test was carried out on two other bridges of the same type. The fatigue life was 180000 times and 420000 times respectively, which failed to meet the design requirement of 500000 times. The results show that there is a deviation between the predicted value and the test value, which may be due to the fact that the heat treatment process of the hypoid gear, the residual stress of the hypoid gear, the assembly deviation of the drive axle and the randomness of the fatigue test are not considered in the simulation process. However, the predicted results are consistent with the results of the driving bridge abutment test, and the number of fatigue cycles is very close, indicating that the fatigue prediction method based on the integral driving bridge finite element model can accurately predict the tooth root fatigue stress.