1.Parameter calculation of helical cylindrical gear pair
In this design, helical cylindrical gear is selected for transmission. The precision of helical cylindrical gear is grade 7. The material of pinion gear is 40Cr. The heat treatment method is surface quenching. The material of wheel of helical cylindrical gear is 20cr2. The heat treatment method is surface quenching after carburizing. The working life LH is calculated according to the total working time, and the number of stress cycles N1 and N2 are calculated according to formula (1) and formula (2) according to the rotational speed n1 of the helical cylindrical gear pinion, the number of meshing J on the same tooth surface, and the number of teeth Z2 and Z1 of the helical cylindrical gear wheel and pinion:
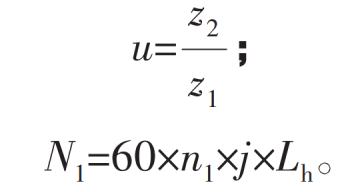
Where u is the gear ratio. Finally, according to the calculation results, the contact fatigue life coefficients khn1 and khn2 are obtained.
2.Strength check of helical cylindrical gear
1) Method 1: check according to tooth surface contact fatigue strength. Calculate the parameter values of helical cylindrical gear through equations (3) – (8):
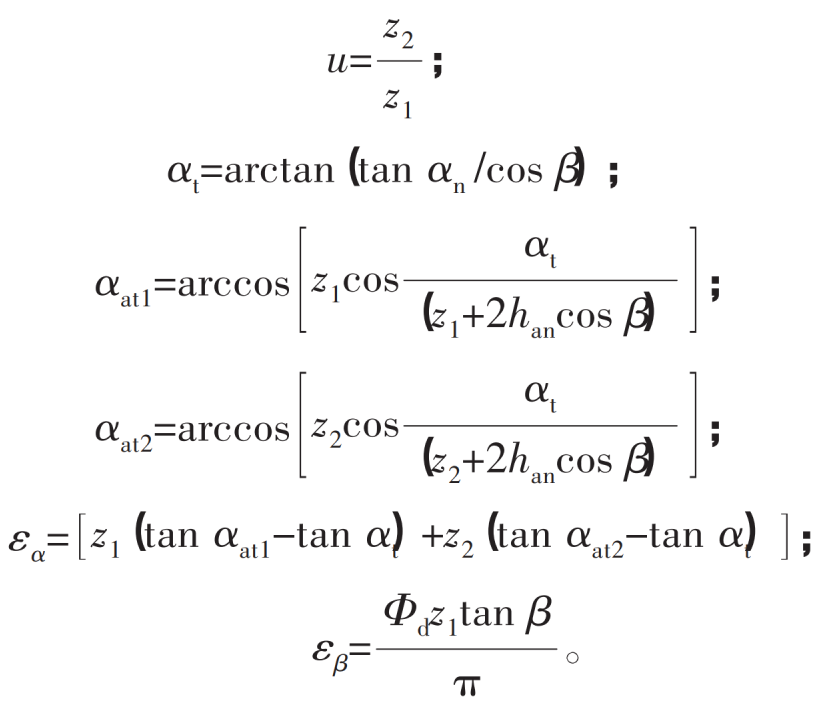
Where: Z1 and Z2 are the number of helical cylindrical gear pinion and helical cylindrical gear large teeth; α N is the normal pressure angle; α T is the end pressure angle; Han is the tooth crest height coefficient; Φ D is the tooth width coefficient; β To correct the helix angle.
Calculate the coincidence coefficient Z for contact fatigue strength by formula (9) and formula (10) ε And rotation angle coefficient Z β:
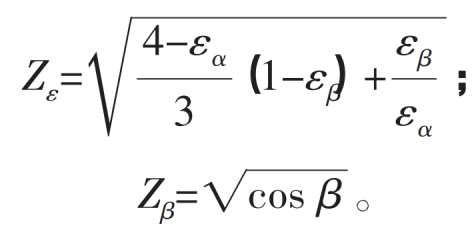
The service coefficient Ka, dynamic load coefficient kV and load distribution coefficient KH between teeth can be obtained by looking up the table α And KH β, Calculate the actual load coefficient KH according to formula (11):
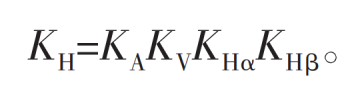
Calculate the pitch circle diameter of helical cylindrical gear pinion by formula (12):
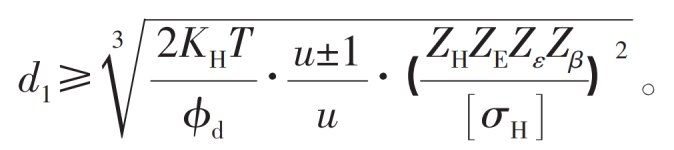
The area coefficient zh and the elastic influence coefficient Ze are obtained by looking up the table. The parameters are substituted into formula (13) to obtain the check results of the contact fatigue strength of the tooth surface:
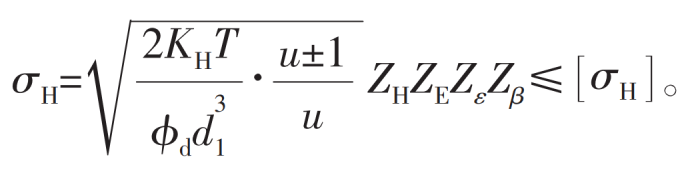
2) Method 2: check according to bending fatigue strength of tooth root.
Select the load coefficient KFT, and calculate the coincidence coefficient y between each parameter and bending fatigue strength through equations (14) – (16) ε:
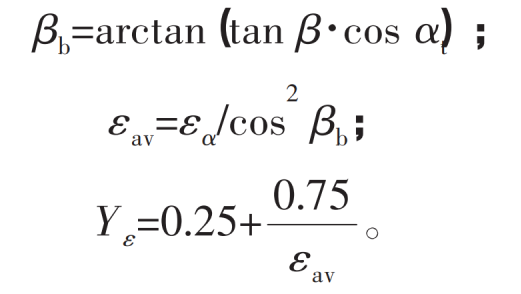
Where: β B is the helix angle of the base circle; ε AV is the coincidence degree of equivalent helical cylindrical gear.
Calculate the spiral angle coefficient y of bending fatigue strength by equation (17) β:
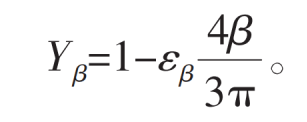
The tooth profile coefficients yfa1 and yfa2 and the stress correction coefficients ysa1 and ysa2 are obtained by looking up the table, and then the helical cylindrical gear module Mn is calculated by formula (18):
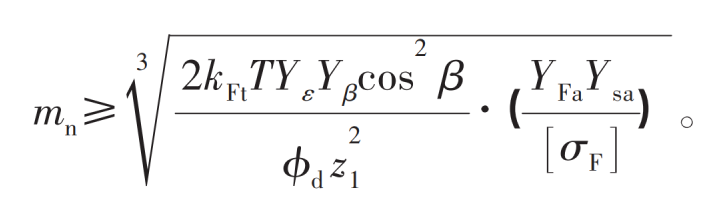
Finally, the bending fatigue strength of the checked helical cylindrical gear is calculated by formula (19):
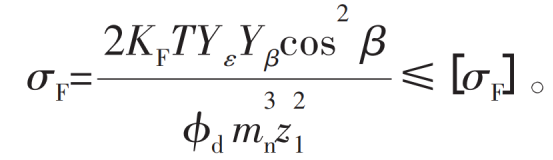