With the intensification of global warming, it is urgent for countries to carry out energy transformation and develop high-quality low-carbon economy. In this context, the country has established the national policy of building an ecological civilization society, made efforts to improve the policy of energy conservation and emission reduction, and proposed to develop high-quality and efficient energy. Due to the serious problem of exhaust emissions from traditional fuel vehicles, only new energy vehicles with low pollution will dominate the automotive market in the future. At present, the well-known new energy vehicles at home and abroad include Volkswagen ID.4X, Tesla Model S, BYD Tang, etc., as shown in the figure. Although these electric oil hybrid or pure electric vehicles have the advantages of energy saving, low noise, low consumption, etc. compared with fuel vehicles, without the contrast of traditional gearboxes, the noise generated by gearbox gears is more sharp than that generated by smooth and quiet motor drive. At the same time, the rapid development of the new energy vehicle industry has brought noise, vibration Harshness puts forward higher requirements. Some studies have shown that the vibration and noise characteristics of helical gear, as an indispensable part of the gearbox, affect the vehicle performance. Therefore, how to reduce the helical gear transmission noise of the electric vehicle gearbox, improve the vehicle performance, and thus improve its market competitiveness has become the key to the country’s technological leadership in new energy vehicles.
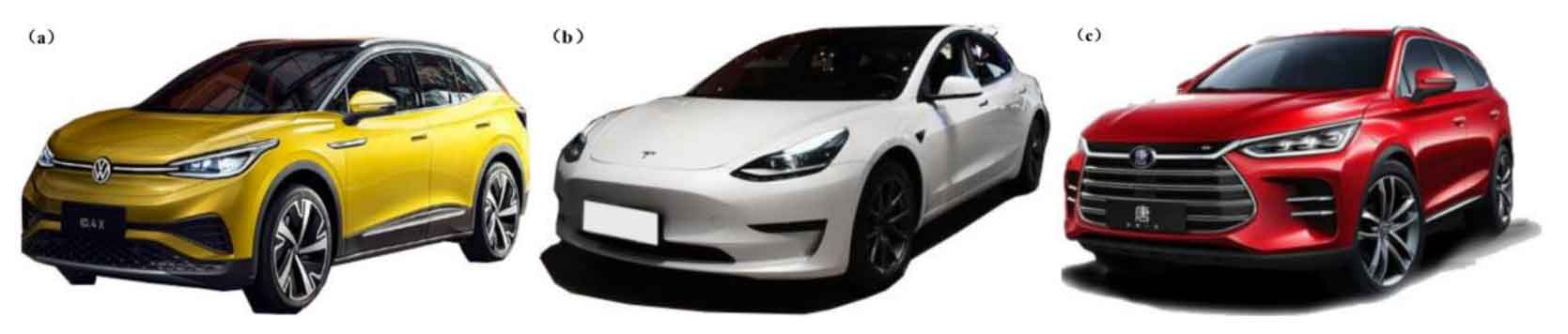
During the driving of electric vehicle, the reducer will make noise due to the exciting force when the helical gear is engaged, the nonlinear vibration when the bearing is running, the shaft vibration, the shell wall vibration, etc. Among the various factors that make up the vibration noise of electric vehicle gearbox, the noise of helical gears accounts for the vast majority, so it is self-evident that it is important to carry out research on it. In fact, scholars at home and abroad had carried out relevant research on helical gear vibration and noise as early as the beginning of last century, but what really made it a hot issue was in the mid 1960s. Nowadays, the ability to control the vibration and noise of helical gears has become an important indicator to measure the quality of a helical gear transmission device, which not only reflects the manufacturing capacity of relevant enterprises, but also reflects the comprehensive strength of a country’s manufacturing industry.
As an important mechanical component for power transmission, helical gear has the advantages of reliable operation, less energy loss and fixed transmission ratio, and is widely used in automobile, industrial gearbox, machine tools and other fields. However, under the actual working conditions, due to the influence of manufacturing accuracy error and installation position deviation, the helical gear pair will produce a certain degree of mesh in and mesh out impact when the gear teeth are alternately engaged, which will then cause unnecessary vibration noise, uneven stress distribution, excessive axial force during engagement, helical gear wear and other serious problems, and ultimately lead to unstable transmission during helical gear engagement, premature scrapping of reducer and other mechanical equipment. However, from the perspective of actual production and mechanism research, it is not a fundamental policy to try to reduce the vibration noise of the electric vehicle gearbox only by improving the gear manufacturing accuracy, reducing the installation position error of bearings and other accessories, and improving the helical gear materials. Instead, it will cause a significant increase in production costs. Under this background, helical gear modification technology came into being.
In recent years, gear modification technology is an important method to reduce gear vibration noise and increase its service life. From a certain point of view, if we can apply gear modification technology to helical gears, improve their service life, reduce their vibration during meshing transmission, fundamentally improve the noise of the helical gear transmission system of the entire automobile gearbox, and then control the performance of the whole vehicle, we can finally form a complete set of theoretical system for predicting, analyzing, optimizing, and testing the vibration and noise of helical gear optimization modification, which will improve the quality of related brand vehicles It is of positive significance to increase the market share.
With the intensification of global warming, it is urgent for countries to carry out energy transformation and develop high-quality low-carbon economy. In this context, the country has established the national policy of building an ecological civilization society, made efforts to improve the policy of energy conservation and emission reduction, and proposed to develop high-quality and efficient energy. Due to the serious problem of exhaust emissions from traditional fuel vehicles, only new energy vehicles with low pollution will dominate the automotive market in the future. At present, the well-known new energy vehicles at home and abroad include Volkswagen ID.4X, Tesla Model S, BYD Tang, etc., as shown in the figure. Although these electric oil hybrid or pure electric vehicles have the advantages of energy saving, low noise, low consumption, etc. compared with fuel vehicles, without the contrast of traditional gearboxes, the noise generated by gearbox gears is more sharp than that generated by smooth and quiet motor drive. At the same time, the rapid development of the new energy vehicle industry has brought noise, vibration Harshness puts forward higher requirements. Some studies have shown that the vibration and noise characteristics of helical gear, as an indispensable part of the gearbox, affect the vehicle performance. Therefore, how to reduce the helical gear transmission noise of the electric vehicle gearbox, improve the vehicle performance, and thus improve its market competitiveness has become the key to the country’s technological leadership in new energy vehicles.
During the driving of electric vehicle, the reducer will make noise due to the exciting force when the helical gear is engaged, the nonlinear vibration when the bearing is running, the shaft vibration, the shell wall vibration, etc. Among the various factors that make up the vibration noise of electric vehicle gearbox, the noise of helical gears accounts for the vast majority, so it is self-evident that it is important to carry out research on it. In fact, scholars at home and abroad had carried out relevant research on helical gear vibration and noise as early as the beginning of last century, but what really made it a hot issue was in the mid 1960s. Nowadays, the ability to control the vibration and noise of helical gears has become an important indicator to measure the quality of a helical gear transmission device, which not only reflects the manufacturing capacity of relevant enterprises, but also reflects the comprehensive strength of a country’s manufacturing industry.
As an important mechanical component for power transmission, helical gear has the advantages of reliable operation, less energy loss and fixed transmission ratio, and is widely used in automobile, industrial gearbox, machine tools and other fields. However, under the actual working conditions, due to the influence of manufacturing accuracy error and installation position deviation, the helical gear pair will produce a certain degree of mesh in and mesh out impact when the gear teeth are alternately engaged, which will then cause unnecessary vibration noise, uneven stress distribution, excessive axial force during engagement, helical gear wear and other serious problems, and ultimately lead to unstable transmission during helical gear engagement, premature scrapping of reducer and other mechanical equipment. However, from the perspective of actual production and mechanism research, it is not a fundamental policy to try to reduce the vibration noise of the electric vehicle gearbox only by improving the gear manufacturing accuracy, reducing the installation position error of bearings and other accessories, and improving the helical gear materials. Instead, it will cause a significant increase in production costs. Under this background, helical gear modification technology came into being.
In recent years, gear modification technology is an important method to reduce gear vibration noise and increase its service life. From a certain point of view, if we can apply gear modification technology to helical gears, improve their service life, reduce their vibration during meshing transmission, fundamentally improve the noise of the helical gear transmission system of the entire automobile gearbox, and then control the performance of the whole vehicle, we can finally form a complete set of theoretical system for predicting, analyzing, optimizing, and testing the vibration and noise of helical gear optimization modification, which will improve the quality of related brand vehicles It is of positive significance to increase the market share.