The process of gear forging involves several steps to transform raw materials into finished gears. Here’s an overview of the typical process:
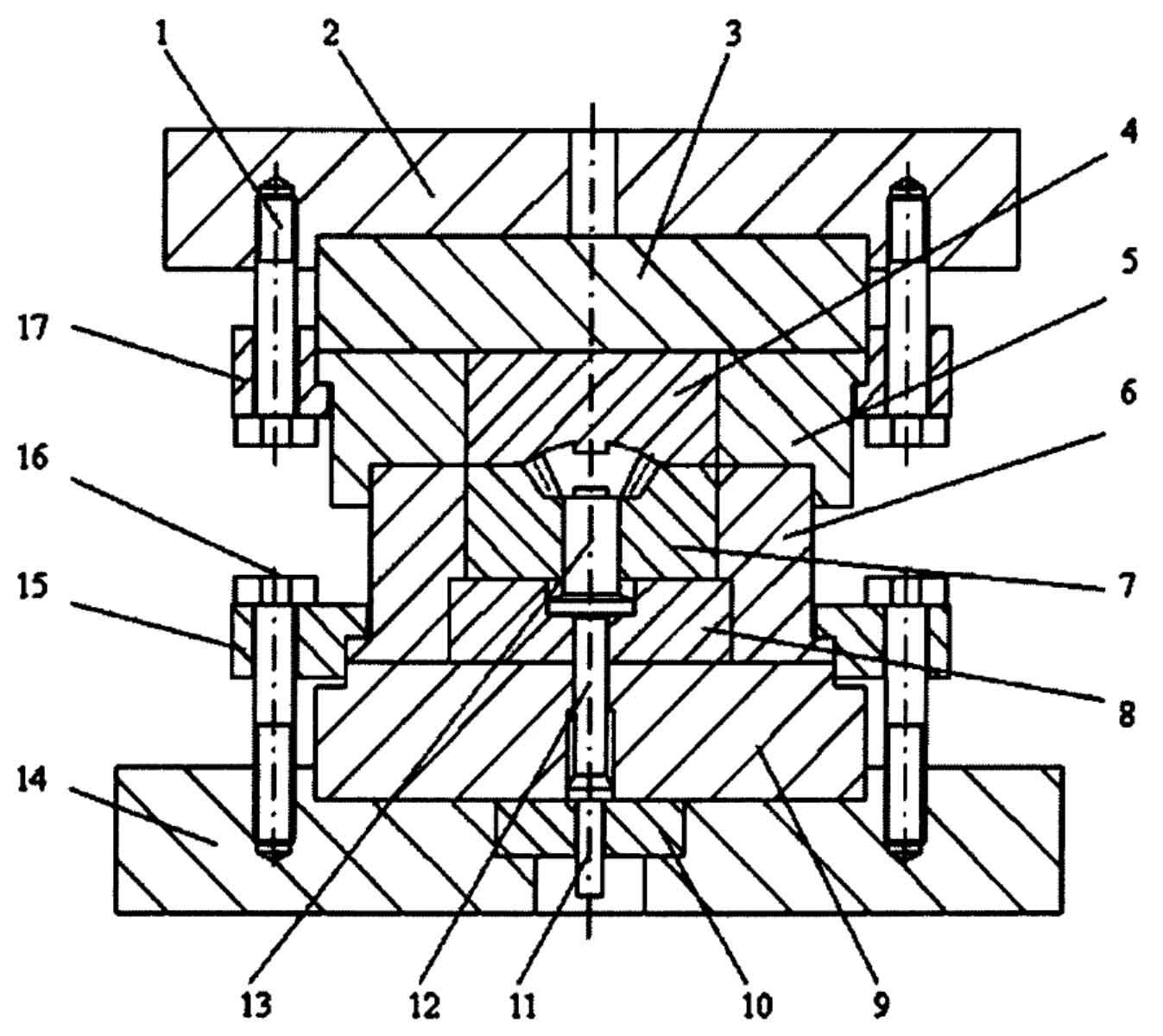
- Raw Material Selection: The first step is to select the appropriate raw material for gear forging. Common materials used for gear forging include carbon steel, alloy steel, stainless steel, and other specialized alloys. The material selection depends on factors such as the application, required strength, and operating conditions of the gear.
- Billet Preparation: The selected raw material is obtained in the form of a billet, which is a cylindrical or rectangular bar. The billet is cut to the desired length based on the size and specifications of the gear to be forged.
- Heating: The billet is then heated in a furnace to an elevated temperature, typically above the recrystallization temperature of the material. This heating process helps in improving the material’s malleability and reduces the risk of cracking during forging.
- Die Preparation: Meanwhile, the die, which is a specialized tool with the inverse shape of the desired gear, is prepared. The die is typically made from high-strength steel and undergoes machining processes to achieve the required gear profile.
- Forging Process: Once the billet reaches the desired forging temperature, it is placed onto the lower die, which is part of the forging press or hammer. The upper die is brought down with substantial force, exerting pressure on the billet. The force applied causes the metal to flow and take the shape of the die, forming the gear profile. This process can be done using either an open-die forging or closed-die forging method, depending on the complexity of the gear shape.
- Heat Treatment: After the forging process, the gear is subjected to heat treatment to refine its microstructure and enhance its mechanical properties. This typically involves processes such as quenching and tempering to achieve the desired hardness and toughness.
- Machining: In some cases, additional machining operations may be required to achieve precise dimensions, tolerances, and surface finishes. Machining processes, such as milling, grinding, and drilling, are performed to remove excess material, create gear teeth profiles, and achieve the final shape of the gear.
- Inspection and Quality Control: The finished gears undergo rigorous inspection to ensure they meet the required specifications and quality standards. This may include dimensional measurements, hardness testing, surface inspection, and other non-destructive testing methods.
- Surface Treatment and Finishing: Depending on the application and customer requirements, the gear may undergo surface treatments like coating, plating, or shot peening to improve its corrosion resistance, lubrication properties, or appearance.
- Final Inspection and Packaging: Once the gears pass the quality control checks, they undergo a final inspection to ensure they meet all the necessary requirements. The gears are then packaged and prepared for shipment to customers or further assembly in the manufacturing process.
It’s important to note that the specific details of the gear forging process can vary depending on factors such as the size and complexity of the gear, the equipment used, and the specific requirements of the application.
Pages: 1 2