Gear forgings offer several advantages and find extensive applications in industrial gear systems. Here are some of the key advantages and applications:
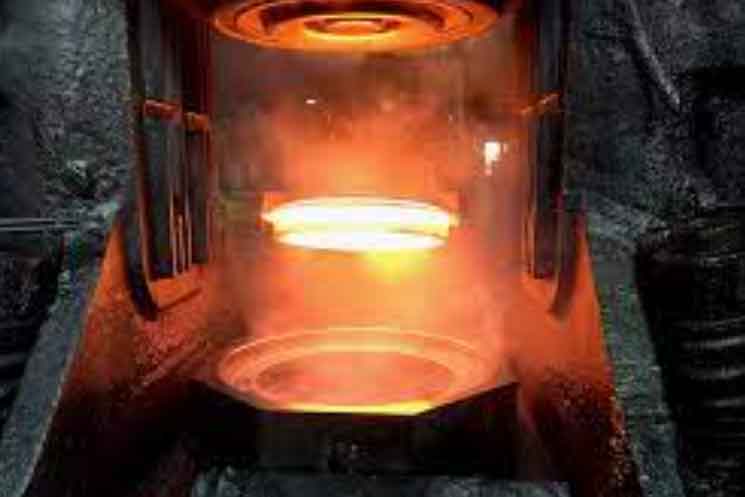
Advantages of Gear Forgings:
- Strength and Durability: Gear forgings are known for their exceptional strength and durability. The forging process creates a refined grain structure that enhances the mechanical properties of the gears, including high tensile strength, toughness, and resistance to fatigue and impact loads. This makes gear forgings ideal for heavy-duty applications where reliability and longevity are crucial.
- Improved Material Properties: The controlled heating and cooling during the forging process result in improved material properties, such as enhanced hardness, wear resistance, and dimensional stability. Gear forgings can withstand high loads and provide consistent performance even in demanding operating conditions.
- Cost Efficiency: While gear forgings may have higher upfront costs compared to other manufacturing methods like casting, they offer long-term cost efficiency. The superior strength and durability of gear forgings reduce the need for frequent replacements and maintenance, resulting in lower overall lifecycle costs.
- Design Flexibility: Gear forgings allow for greater design flexibility, enabling the creation of complex gear geometries and custom configurations. This flexibility allows engineers to optimize gear designs for specific applications, improving performance and efficiency.
Applications of Gear Forgings:
- Industrial Gearboxes: Gear forgings are extensively used in industrial gearboxes across various sectors, including manufacturing, energy, and transportation. These gearboxes are employed in heavy machinery, power generation systems, wind turbines, and marine propulsion systems, among others. Gear forgings ensure reliable power transmission and efficient torque conversion in these critical applications.
- Automotive Transmissions: Gear forgings are widely used in automotive transmissions to transmit power from the engine to the wheels. The high-strength and durability of gear forgings ensure smooth and efficient gear shifting, contributing to improved vehicle performance, fuel efficiency, and driver comfort.
- Construction Equipment: Gear forgings find application in construction equipment, such as cranes, excavators, bulldozers, and loaders. These machines require gears that can withstand heavy loads, shock, and vibrations. Gear forgings offer the necessary strength and durability for the demanding working conditions encountered in the construction industry.
- Aerospace and Defense: The aerospace and defense sectors rely on gear forgings for various applications, including aircraft engines, helicopter transmissions, missile systems, and naval propulsion systems. Gear forgings provide the required strength, reliability, and weight reduction necessary for these high-performance applications.
- Oil and Gas Industry: Gear forgings are used in the oil and gas industry for drilling equipment, pumps, compressors, and refineries. The gears used in these applications must handle extreme loads, harsh environments, and continuous operation. Gear forgings deliver the necessary strength and durability to withstand these challenging conditions.
Gear forgings offer numerous advantages over alternative manufacturing methods and find extensive use in various industrial gear systems where strength, durability, and performance are critical factors.