Spiral bevel gears are known for their ability to drive efficiency and enhance performance in various gear applications. Here are some key aspects that contribute to their effectiveness:
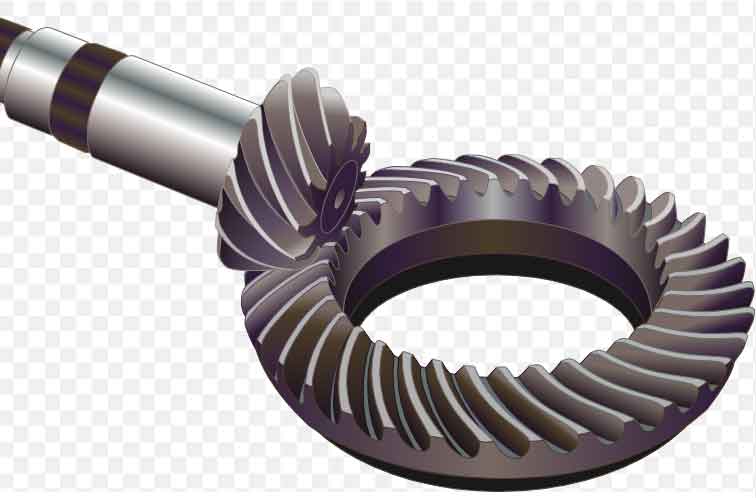
- Power Transmission Efficiency: Spiral bevel gears have high mechanical efficiency due to their tooth geometry and meshing characteristics. The spiral teeth allow for gradual engagement and smooth contact between the gear surfaces, resulting in reduced friction and improved power transmission efficiency.
- Load Distribution: The spiral tooth profile of the gears facilitates load distribution across multiple teeth, increasing the contact area and reducing tooth stresses. This enables the gears to handle higher loads and transmit power efficiently while minimizing the risk of tooth failure.
- Torque Transmission: Spiral bevel gears are capable of transmitting high torque due to their robust tooth design and contact pattern. The gradual engagement of the teeth allows for efficient torque transfer and helps to distribute the load evenly, reducing the concentration of stresses on individual teeth.
- Compact Design: Spiral bevel gears offer a compact and space-saving design compared to other gear types. The spiral tooth profile allows for a larger number of teeth to be engaged simultaneously, resulting in a more compact gear assembly. This is particularly advantageous in applications where space is limited, such as automotive differentials and power tools.
- Smooth and Quiet Operation: The spiral tooth profile of the gears reduces noise and vibration during operation. The gradual engagement of the teeth minimizes impact forces and helps to maintain a constant meshing contact, resulting in quieter operation and improved gear durability.
- High-Speed Capability: Spiral bevel gears are well-suited for high-speed applications due to their balanced tooth geometry and optimized tooth contact pattern. They can operate at higher rotational speeds while maintaining good load-carrying capacity and minimizing noise and vibration.
- Versatility: Spiral bevel gears can be used in a wide range of applications, including automotive, aerospace, industrial machinery, and marine systems. They are suitable for both high-power and high-speed applications, making them versatile and adaptable to various gear transmission needs.
To fully harness the efficiency and performance benefits of spiral bevel gears, it is important to consider factors such as gear design, material selection, lubrication, and proper installation and maintenance practices. Collaboration with experienced gear engineers and utilizing advanced design and analysis tools can help optimize the performance and reliability of spiral bevel gear systems.