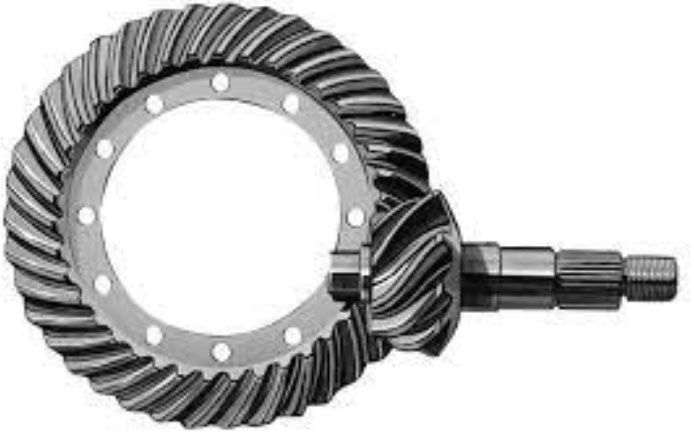
Maintenance and proper lubrication are essential for ensuring the longevity and optimal performance of hypoid gear systems. Hypoid gears, with their sliding contact and offset design, have unique requirements that must be addressed to prevent wear, reduce friction, and minimize the risk of premature failure. Here are some best practices for maintaining and lubricating hypoid gears:
1. Regular Inspection:
- Implement a scheduled inspection program to monitor the condition of the gear system. Regular inspections allow for early detection of wear, misalignment, or any other issues that may impact gear performance.
2. Lubricant Selection:
- Choose lubricants specifically designed for hypoid gears. Hypoid gear lubricants typically have additives that reduce friction, prevent wear, and handle the extreme pressure conditions in the gear system.
3. Proper Lubrication Amount:
- Ensure that the gear system is correctly filled with the recommended amount of lubricant. Under-lubrication can lead to increased wear, while over-lubrication may cause overheating and lead to lubricant degradation.
4. Lubricant Change Interval:
- Follow the manufacturer’s recommendations for lubricant change intervals. Regularly changing the lubricant helps maintain its effectiveness and extends gear life.
5. Lubricant Contamination Control:
- Prevent contamination of the lubricant by using proper seals and guarding against external elements such as dust, water, or debris. Contaminated lubricant can cause accelerated wear and reduce gear performance.
6. Gear Mesh Alignment:
- Ensure proper gear mesh alignment during installation and any subsequent maintenance or repairs. Misalignment can lead to increased wear and decreased gear efficiency.
7. Proper Torque Application:
- Follow the manufacturer’s torque specifications when assembling or reassembling the gear system. Incorrect torque application can lead to gear damage or misalignment.
8. Gearbox Ventilation:
- Adequate gearbox ventilation is crucial to maintain proper lubricant cooling and prevent overheating. Check for proper ventilation to avoid lubricant breakdown due to excessive heat.
9. Operating Conditions:
- Be mindful of the operating conditions in which the gear system is used. Extreme temperature, high loads, and severe shock loads may require specialized lubricants or additional maintenance measures.
10. Training and Documentation:
- Ensure that maintenance personnel are properly trained to handle hypoid gear systems. Keep detailed records of maintenance activities, including lubricant changes and inspections.
11. Noise and Vibration Monitoring:
- Regularly monitor gear noise and vibration levels during operation. Significant changes in noise or vibration may indicate potential issues that require attention.
By adhering to these best practices, operators can extend the longevity of their hypoid gear systems, minimize downtime, and enhance overall gear system performance. Regular maintenance and proper lubrication are critical to ensuring smooth and reliable operation, particularly in applications where hypoid gears are subjected to high loads and harsh operating conditions.