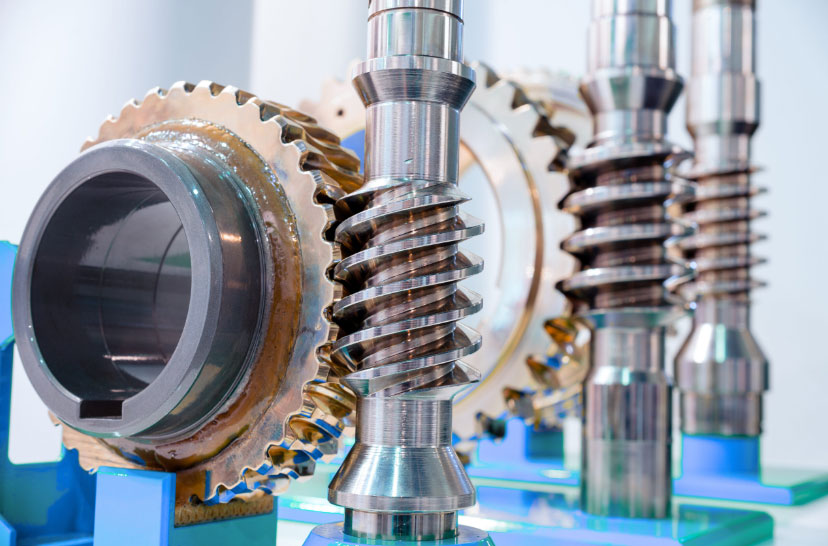
Custom worm gears play a crucial role in enhancing the performance of robotics and automation systems. These gears consist of a worm (a type of screw) and a gear (a toothed wheel) meshing together to transmit motion and power at a right angle. They are often used in applications where high reduction ratios and precision are required, such as robotics, automation, and machinery with limited space.
To optimize performance in robotics and automation, consider the following factors when designing and implementing custom worm gears:
- Material Selection: Choose high-quality materials for both the worm and gear components. Heat-treated and hardened materials like alloy steels (e.g., 8620, 9310) or stainless steel provide increased durability and wear resistance.
- Gear Ratio and Efficiency: Select an appropriate gear ratio that meets the specific application’s requirements. Higher reduction ratios are advantageous for increasing torque output but can reduce gear efficiency. Strive to strike a balance between torque and efficiency to avoid unnecessary power losses.
- Gear Geometry: The design of worm gear teeth is critical. Opt for precise tooth profiles to minimize backlash and ensure smooth motion transmission. Common tooth profiles include the concave “globoid” worm and the more traditional “cylindrical” worm.
- Lubrication: Proper lubrication is essential for reducing friction and wear, ensuring smooth operation, and extending the gear’s lifespan. Choose lubricants with the right viscosity and additives to handle the specific application’s loads and temperatures.
- Mounting and Housing: Ensure precise alignment during assembly to prevent misalignment, which can lead to premature wear and decreased performance. Utilize rigid housings to maintain gear alignment and reduce external disturbances.
- Backlash Minimization: Backlash, the play between the worm and gear teeth, can impact precision in robotics and automation. Minimize backlash through careful design and manufacturing, or use preloaded worm gears to compensate for any potential slack.
- Noise and Vibration Reduction: In noise-sensitive applications, consider noise reduction techniques such as tooth profiling modifications, damping elements, and isolation mounts.
- Temperature Considerations: Evaluate the operating temperature of the gear system and choose materials and lubricants that can withstand the expected range without compromising performance.
- Maintenance and Inspection: Design the gear system to allow for easy maintenance and inspection, enabling timely identification of wear or damage.
- Simulation and Testing: Utilize computer simulations and physical testing to validate the gear design’s performance under real-world conditions. This can help identify potential issues and refine the design before implementation.
- Application-Specific Design: Tailor the worm gear design to suit the specific application’s needs. Consider factors such as load requirements, operating environment, speed, and duty cycle.
Remember that custom worm gears can be complex, and it’s essential to involve experienced engineers and gear specialists in the design and optimization process. By addressing these aspects, custom worm gears can unleash the full potential of robotics and automation systems, providing improved efficiency, precision, and reliability.