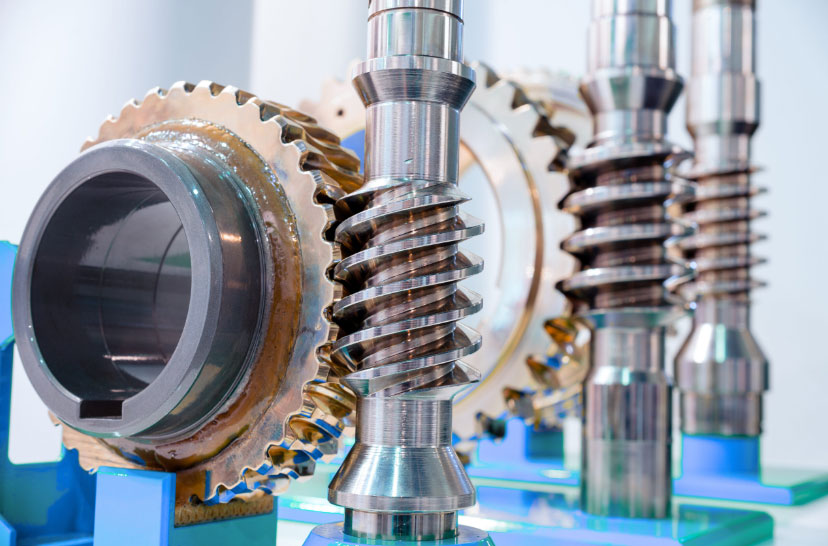
Worm gears are essential components in various industrial applications, and advancements in custom worm gears have indeed revolutionized gear technology. These advancements focus on optimizing performance, durability, efficiency, and precision to meet the specific requirements of modern industries. Here’s how custom worm gears are transforming gear technology:
1. Improved Material Selection:
- Advancements in material science have led to the development of high-performance alloys and surface treatments for worm gears. Custom worm gears are now made from materials that offer superior strength, wear resistance, and fatigue life, enhancing their overall durability.
2. Precision Manufacturing Techniques:
- Custom worm gears are manufactured using advanced precision machining techniques such as CNC grinding and milling. This ensures accurate tooth profiles and precise gear geometry, resulting in smoother operation and reduced backlash.
3. High Gear Ratios:
- Custom worm gears can be designed with higher gear ratios than standard worm gears. This allows for increased torque multiplication and power transmission efficiency, making them suitable for heavy-duty applications.
4. Customized Tooth Profiles:
- Advanced design and simulation tools allow for the optimization of worm gear tooth profiles. Custom tooth profiles can be tailored to specific applications, reducing friction and wear while enhancing load distribution.
5. Noise Reduction:
- Custom worm gears can be designed with tooth modifications and microgeometry to reduce noise during meshing. Noise dampening features help achieve quieter gear operation in noise-sensitive environments.
6. Backlash Reduction:
- Custom worm gears can incorporate features to minimize backlash, improving accuracy and repeatability in motion control applications.
7. Corrosion Resistance:
- For applications in harsh environments or exposure to corrosive substances, custom worm gears can be coated or made from materials with enhanced corrosion resistance properties.
8. Increased Efficiency:
- Advancements in custom worm gear design and manufacturing have led to improved efficiency, reducing energy losses and increasing the overall performance of gear systems.
9. Custom Integration:
- Custom worm gears can be designed to seamlessly integrate into complex mechanical systems. This allows for optimized system performance and increased functionality in industrial applications.
10. Lubrication Optimization:
- Custom worm gears can be designed to optimize lubrication distribution and reduce friction, contributing to longer gear life and lower maintenance requirements.
With these advancements in custom worm gears, industries such as robotics, aerospace, automotive, and industrial machinery are benefitting from gear solutions tailored to their specific needs. Custom worm gears have become a crucial component in high-precision motion control, power transmission, and automation systems, providing improved performance and reliability for modern gear technology. As technology continues to evolve, we can expect further innovations in custom worm gears, driving continuous improvements in gear technology across various industries.