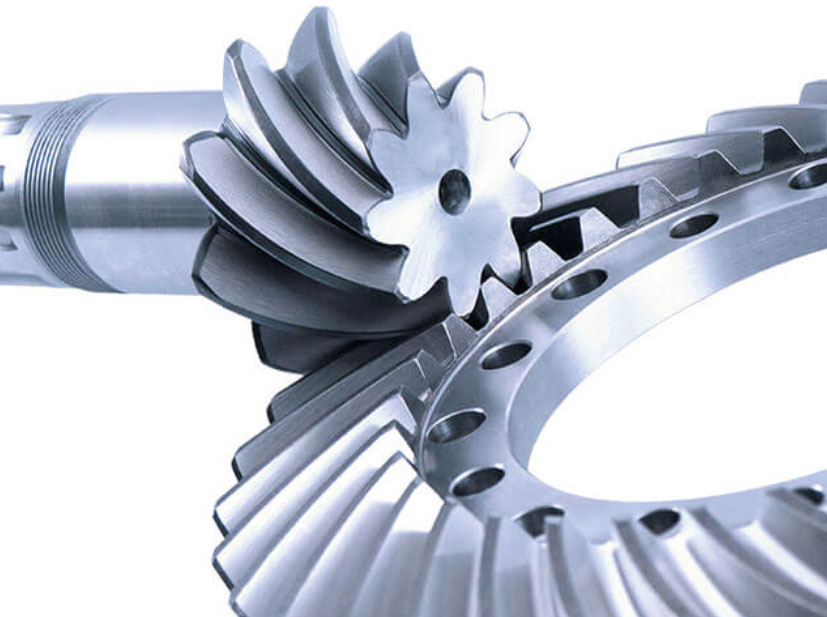
Spiral bevel gear inspection and quality control are critical to ensure the gears’ proper functionality, reliability, and durability. Various methods are employed to assess the gear’s dimensional accuracy, tooth geometry, surface integrity, and overall quality. Here are some commonly used inspection and quality control methods for spiral bevel gears:
1. Coordinate Measuring Machines (CMM):
- CMMs are sophisticated measurement devices used to assess the dimensional accuracy of spiral bevel gears.
- They can precisely measure the gear’s tooth profile, pitch, and runout, comparing the results to the design specifications.
2. Gear Inspection Machines:
- Dedicated gear inspection machines are used to evaluate the gear’s tooth profile, lead, pitch, and tooth spacing.
- These machines can provide accurate readings of gear geometry and verify compliance with design requirements.
3. Gear Roll Testers:
- Gear roll testers evaluate the gear’s tooth contact pattern and rolling action during meshing.
- The gear is rotated under load to check for proper tooth engagement and smooth motion.
4. Optical Profile Projectors:
- Optical profile projectors are used for visual inspection of gear tooth profiles and overall shape.
- They provide a magnified view of the gear’s surface and allow operators to check for any surface defects.
5. Surface Roughness Measurement:
- Surface roughness measurement tools assess the gear’s surface finish and integrity.
- The surface roughness is critical for reducing friction and wear, especially in high-performance applications.
6. Non-Destructive Testing (NDT):
- NDT methods, such as magnetic particle inspection and dye penetrant testing, are used to detect surface cracks or defects that might affect gear performance.
- These methods help identify potential defects without damaging the gear.
7. Hardness Testing:
- Hardness testing assesses the gear’s hardness to ensure it meets the required specifications.
- Proper hardness is essential to ensure the gear’s durability and resistance to wear.
8. Contact Pattern Analysis:
- Contact pattern analysis, using techniques like blue dye method or pressure-sensitive films, evaluates the tooth contact pattern during gear meshing.
- It ensures even distribution of contact along the tooth flank, minimizing stress concentrations.
9. Dimensional Gauging:
- Various dimensional gauges are used to measure critical dimensions of the gear, such as pitch diameter, root diameter, and backlash.
- These gauges ensure that the gear meets specified dimensional tolerances.
10. Quality Management Systems:
- Implementing quality management systems, such as ISO 9001, ensures that the entire manufacturing process adheres to strict quality control standards.
- Quality control checks are performed at various stages of production to maintain consistent product quality.
Proper inspection and quality control methods are essential to identify and rectify any manufacturing defects, ensure gear conformance to design specifications, and guarantee the gear’s performance and reliability. Adhering to stringent quality control measures is crucial in delivering high-quality spiral bevel gears for a wide range of applications, including automotive, aerospace, industrial machinery, and more.