1 Introduction
Nowadays, automobiles are attracting attention in terms of their functionality as an indispensable means of transportation in people’s real lives. In automobile processing and production, gears belong to the basic transmission components. With the increasing demand for automobiles, the quality of gears and their functions are highly valued. The gradual improvement of gear processing technology is conducive to the positive improvement of gear strength and ensures that the gear is available In addition to the noise reduction and durability functions, it also ensures that the stability of the car is improved, thereby extending the life cycle and overall comfort of the car.
2 Dry cutting technology for gear machining
Cutting oil has always been used in the machining of automobile gears, which not only pollutes the industrial production environment, but also poses a major threat to the health of the operators themselves. In addition, the use of cutting oil will also increase related costs, such as the cost of disposing of waste oil, the cost of cutting oil, the separation of oil mist equipment, etc. These will further increase the processing cost, and some countries even exceed 10%~30% of the total processing cost in terms of processing cutting oil costs. Therefore, under the requirements of environmental protection, automotive gear processing plants in many countries advocate the use of non-cutting oil Quasi-dry cutting technique. In order to ensure that dry cutting is feasible, research and development must be strengthened first
Machine tools and tools required for dry cutting foundations. In dry cutting technology, the tools required to ensure a stable service life and the rapid evacuation of chips generated at high temperatures are also required for the machine. With the improvement of machine tool design technology and the continuous development of tool coating and material technology, automobile gear processing provides space for the rapid development of gear dry cutting technology in many countries, so as to achieve continuous improvement of social benefits.
2.1 Hobbing dry cutting technology
In the early 70s of the 20th century, Japan developed the technology for dry cutting of tungsten carbide hob cylindrical gears (Fig. 1), and widely introduced it on the market, such as Mitsubishi Heavy Industries and a company to process cemented carbide gear equipment. In the 80s of the 20th century, many units such as China’s research tool industry, gear processing plant, machine tool factory, and material research factory also shouldered the research and development task of cemented carbide hob tools, and began to dry cut cemented carbide hob technology Some technologies and products have even obtained scientific and technological achievements Research awards, such as a reverse gear (m=3.175), but have not been consistently studied due to many factors. This type of technology is currently used in synchronous gearboxes It is used in products such as small modules and pinions, and has not been vigorously promoted in China Wide. Even if Japan is the first to introduce this kind of technology, it has not been widely used, and cemented carbide hob tools are prone to chipping, resulting in a shortened tool application cycle, which is the fundamental factor that its production has not been widely used.
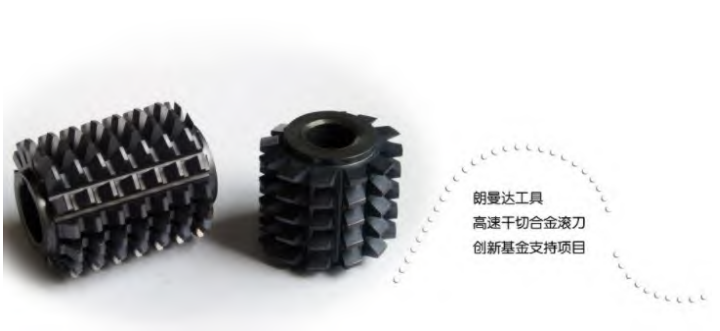
Figure 1 Carbide hob diagram
a. Comparison of hobbing cutters and cutting for dry cutting gear hobbing. Mitsubishi Heavy Industries is developing a dry cutting hob for lifting knives In the cutting of m=2.05, z=49, β=21.5°, b=40 and other workpieces, 170HB and SCM415 were selected. The number of hob heads is 3, i.e. De=75, the number of slots should be controlled at 16, the cutting speed should be controlled at 1 min/v=200 m, and the pass speed should be controlled at 1 revolution/s=2.4 mm. Comparison of dry and wet cutting of rotary milling It was found that dry cutting can be 2 times more effective than wet cutting, 5 times longer tool life cycle, and more than 40% reduction in dry cutting cost due to the absence of cutting oil.
b. Dry cutting and hobbing machine.
During the development of GE Hobbing Machine’s special dry cutting technology, Mitsubishi Heavy Industries is equipped with a special chip conveyor at the appropriate position of the machine to cut, and compressed air is used to quickly discharge the high-temperature chips without touching the machine, so as to prevent thermal deformation of the hobbing machine caused by hot chips. So there is
Some hobbing gears are designed to be horizontal so that chips can be easily evacuated, such as Mitsubishi Heavy Industries’ GN type gear hobbing machine, and some industries have successively introduced a gear hobbing machine that can be used in both wet and dry cutting technologies. Figure 2 shows the machine for dry gear hobbing.
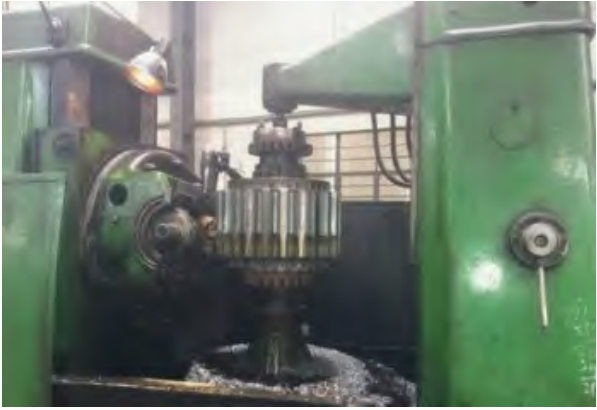
Fig. 2 Diagram of the machine for dry cutting and hobbing
2.2 Shaping dry cutting technology
In the automotive gear processing technology, there are not only hobbing, but also tooth extraction dry cutting technology, such as Tang Ze Iron Industry, Mitsubishi Heavy Industries, etc., have successively developed a gear shaping machine, using dry cutting technology. The model of Mitsubishi Heavy Industries’ gear shaping machine is SE25A, and the material of the dry cutting cutter is high-speed steel, and the speed of rough cutting is 1~2 times higher than that of wet difference, and the processing effect can be improved 1.3~1.5 times, the tool service life can be extended by 3~5 times. When designing this type of gear shaping machine, it is necessary not only to think about the chip evacuation and rigidity of the machine, but also to use a balanced axis to promote the reduction of noise and vibration in high-speed gear shaping.
2.3 Dry cutting technology of spiral bevel gears
a. Spiral bevel gear milling machine for powerful dry cutting.
A company’s six-axis full-control CNC hypoid gear milling machine CNC has chosen a special spindle with a faster speed, and the speed of the cutterhead spindle can reach as fast as 1 min/2 000 r, which is simply not possible in the traditional rocking gear cutting machine. The complex gear drive chain has been eliminated, which ensures a balanced movement of the cutter shaft, thus avoiding the increase in spindle temperature during high-speed cutting actions. The company needs to install it in the processing machine area according to the relevant principles of aerodynamics Equipped with a unique discharge device, the cutter shaft head and the machining area are integrated into all the containers that discharge the cutting, and the chips are blown to the position of the backsplash of the machine tool through two high-pressure air nozzles, so that they are far away from the tool and the workpiece, and 80% of the heat generated by the processing and production will be discharged to the outside of the machine with the cutting synchronization, and the front of the container for discharging and cutting needs to be rotated laterally, so as to facilitate the replacement of tools. The spiral bevel gear is shown in Figure 3.
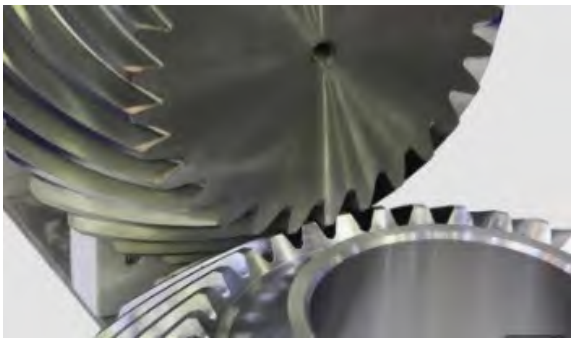
Figure 3 Spiral bevel gear diagram
b. Knives for powerful dry cutting.
For powerful dry cutting, the newly developed model is the PENTAC tool, which has an overall shape of a rod-shaped carbide head. Tungsten carbide cutter heads are coated with diamond grinding wheel blades on a company’s 300CG cutterhead grinder, and the cutter bits are made of carbide material H10F type material, which is equivalent to ISO standard K grade. The cutting surface of the cutter head is coated with TiAIN.
c. Comparison of the economy of strong dry cutting.
A company compared the two types of cutting technologies of the 450HC gear cutting machine, and the results showed that the powerful dry cutting method can achieve better benefits than traditional cutting techniques, for example, the same cutting gear, each gear used to consume 119.85 kW/min, while the powerful dry cutting only required 30.75 kW/min, which is equivalent to 1/4 of the original use. However, the processing time of large and small gears under the same cutting basis is about 1/3~1/2 of the traditional compared with the traditional dry cutting technology. Although it is a strong dry cutting technique The use of coated cemented carbide cutter head is easy to increase the cost, but because the cutter head should be The cycle can be extended, the number of sharpening times can be reduced and the cutting oil can be saved, especially the cutting oil Reduced costs due to improved production efficiency are therefore economically beneficial and often reduce the overall cost of the gear by approximately 28%.
3 Helical tooth shaping machine without helical tooth guide sleeve
When the gear shaping machine is processed by spur gear or helical gear, it is necessary to use a guide sleeve to ensure the smooth progress of the cutting operation, and the helical gear should be reasonably used for the spiral guide sleeve. Helical gears have equal requirements for the helix angle of the shaper cutter and the helix angle of the workpiece. The same requirements are put forward for the lead of the spiral guide sleeve and the lead of the gear shaping cutter, which is generally in the processing and production of helical gears In order to use the spiral guide bushing, it is necessary to carry out a reasonable replacement of the guide sleeve when processing all kinds of helical gears. But because the processing and production process of the guide bushing is very complex, and has a very long manufacturing time, the guide bushing is very troublesome to replace, so when developing a new product, the helical gear has become a major obstacle to the research and development of new products, so the helical gear structure can be changed to two bodies, such as this method is selected when processing the MSB Isuzu intermediate shaft, the other method is to change the helix angle parameter of the workpiece under the existing guide bushing foundation, and this method should be used when designing the gear ring in the 1 252 transfer case, but the above-mentioned methods are all restrictive.
For this reason, for many years, it has been hoped that a gear shaping machine can be used to insert helical gears without the use of helical guides.
4 Synchronous shaving machine
In finishing gears, tooth shaving is also one of the methods. In the shaving process, because the workpiece can be rotated under the drive of the shaving cutter, there is no transmission chain between the two, the secondary meshing is carried out by the shaving cutter and the helical gear of the workpiece without lateral gaps, and the contact point rate of the two will be accompanied by different directions to let the gear processing tooth side move along the shaving cutter to the tooth side, there are many small grooves on the side of the shaving cutter, the groove and the tooth flank intersection line is the cutting edge, and the gear side is in itself Fine chips can be cut off during the slide. Shaving is correcting and reducing the shape of the shaving teeth The effect of tooth direction error and tooth surface roughness is better, especially in lifting In terms of the production effect of tooth shaving, it is significantly lower than the cost of tooth grinding, so it is still there It is still widely used for finishing gears. However, this kind of tooth shaving method still has shortcomings, because it belongs to free transmission, in the reverse processing shaving rotation, it is easy to occur the phenomenon of speed loss, which has a direct impact on the ability to correct the tooth shape, especially the runout error in the radial correction of the gear ring, which is easy to be converted into tangential error, and will also increase the tooth pitch error.
At present, synchronous shaving machines have been developed abroad, such as the FS synchronous shaving machine developed by Mitsubishi Heavy Industries. According to the company’s introduction, there is a mandatory transmission chain between the tooth cutter and the workpiece of this type of tooth shaving machine, and through the synchronous control of the meshing transmission between the razor shaft and the workpiece shaft, it can not only correct the tooth shape and tooth direction, but also strengthen the correction of the tooth distance error and the runout of the gear ring, and the direction of rotation of the shaver is only One, the machining operation can be completed without reversing, and the machining time can be reduced Reduce by 30% to ensure that the shaving operation continues to improve. In addition, the existing transmission shaving machine opens and switches forward and reverse rotation, shape The acceleration and deceleration of the speed of the process is prone to form large loads, resulting in razor wear and damage to the worker Synchronous shaving machines can completely circumvent this problem. After research and development in some countries, it has been proven that synchronous shaving machines are easy to increase the wear rate of the shaving cutter and increase the roughness of the shaving surface.
5 Application of gear grinding processing
5.1 Cylindrical gear grinding processing
When finishing the cylindrical gears of a transmission, the key link is grinding and shaving, but the roughness and precision of grinding the side of the gear are significantly higher than that of shaving, especially the correction of thermal deformation. In the mid-80s of the 20th century, a company introduced the technology of producing transmissions from the Japanese automobile manufacturing industry, and began to widely use gear grinding technology in finishing gears. Limited to the current conditions, some manufacturers think that the production effect of gears is not high, the cost of investment is high, and will not promote a large number of automotive gear processing industry. However, at present, with the rapid development of NC gear grinding machine, the grinding effect is gradually improved, the correction degree of gear is also more simple, CBN grinding wheel is widely used, especially when the automobile improves the accuracy requirements of the transmission gear and the width of the tooth surface is increased in order to promote the continuous improvement of the gear strength under the premise that the core distance of the Sinotruk transmission remains unchanged, and the accuracy of the tooth direction needs to be selected, so it is inevitable to replace the shaving technology before hot tooth grinding through hot post-grinding. Many countries have gears for heavy-duty transmissions and high-end car transmissions Gear grinding will be chosen, especially in European countries, which regards gear grinding as a preferred technology for high-precision production of automotive gears. In recent years, China’s transmission gears have widely used gear grinding technology, which has improved the processing effect.
5.2 Spiral bevel gear grinding processing
The requirements for automobile transmission quality are gradually improving, and the gear grinding requirements are put forward for the transmission pairs of automobile spiral bevel gears and hypoid gears. In the past, foreign companies in the production and processing of mechanical transmission arc tooth bevel gear grinding machine, because of the relatively complex structure, high price, and poor processing effect, did not use the gear grinding technology, which is only used in the production of some small quantities of high precision petroleum machinery, aviation and precision machine tools and other spiral bevel gears. In recent years, with the continuous development of CNC technology, the automotive machining industry has continued to develop similar gear grinding machines, which are used in grinding arc-toothed spiral bevel gears. There are also industries that have developed CNC series arc-toothed spiral tapers The gear grinding machine and grinding technology promote the maximum improvement of the grinding effect. The grinding time of a single piece of arc tooth bevel gear has been equal to the cutting time, especially through the development of the Wagroul method grinding and forming for the processing of spiral bevel gears, so that the grinding technology of automobile gear arc tooth bevel gear has been widely used in a large number of production enterprises.
6 Development of strong honing technology
In the 60~70s of the 20th century, the choice of disc-shaped or worm-shaped refractory wheel as a finishing process for repairing the tooth surface after heating has been used in the foreign automobile processing gear industry, and there are still many enterprises in China that process gears are using this kind of technology, such as the author’s company began to introduce the disc-shaped honing wheel honing machine produced by the British company in the 60s. Practice has shown that such technologies only It can be used to harden the roughness of the tooth surface of the gear, but it cannot improve the accuracy of the tooth shape and tooth direction, and the long honing time will destroy the accuracy of the gear, so this technology has not been widely spread. Although tooth grinding can improve the accuracy of the gear after heating, according to the experimental research of relevant foreign scholars, the ripple on the surface of the gear, that is, the ripple amplitude, wavelength and direction will have an impact on the noise characteristics of the gear. Grinding teeth to reduce noise The sound is extremely unfavorable, and there are many manufacturers who choose to derive the teeth after completing the grinding operation, which is easy to increase the manufacturing cost.
7.Automatic gear sorting and inspection machine
a. Check with a gear pairing machine. The gears that can be meshed are used on the paired device to run at high speeds, and the gears are judged by human senses to see if there are burrs and bump noises.
b. Inspect with a gear double-sided meshing tester. By inspecting the gears and meshing the gear standards on both sides, the inspected gear converts to the center distance to determine whether it has burrs or bump noise.
c. Manual visual inspection. Manually and visually inspect the gear for burrs and bump noise. Although there are advantages and disadvantages of the above inspection methods, there are still common problems, that is, the configuration of special personnel to complete the operation, not only the cost is higher but also needs to rely on human senses to judge, and it is impossible to avoid the unqualified transmission assembly will make the gear burr and bump noise and disassemble again.
8 Conclusion
This article introduces the new technology of the automotive gear processing industry, including the dry cutting and hobbing process of the spiral bevel gear grinding machine, etc., there are many units in China that have carried out research and development work on such technologies, but there are still many new technologies in the blank in China, so China’s manufacturers need to attach great importance to this new technology and development trends, and promote the level of China’s automotive gear manufacturing to a new level.