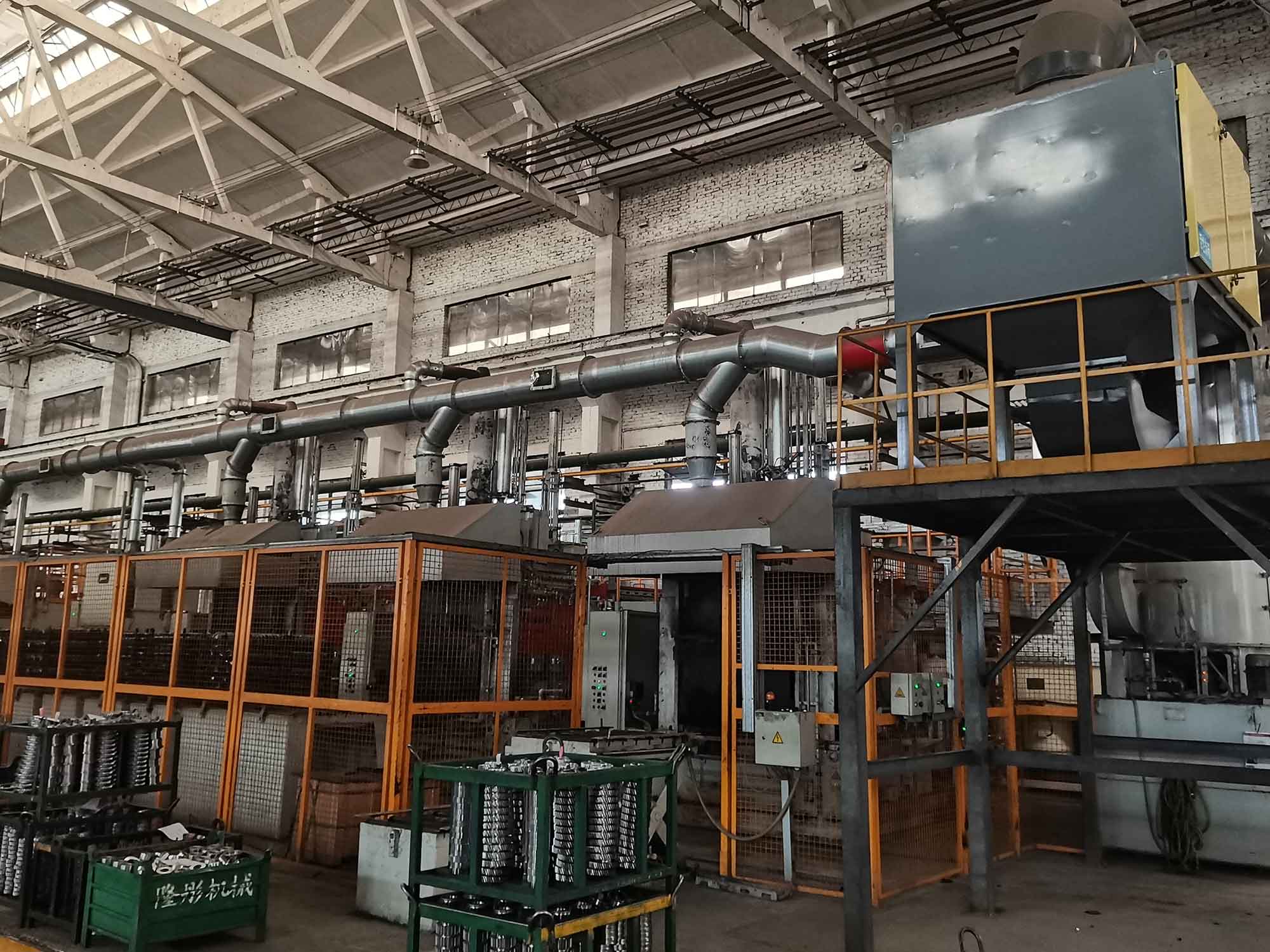
The evolution of gear manufacturing techniques is a fascinating journey through history and technology, showcasing the progression from simple manual methods to highly sophisticated automated processes. Here’s a look at how gear manufacturing has evolved:
- Early History and Manual Techniques:
- Ancient and Medieval Times: Early gears were made of wood and later metals like bronze. These gears were primarily crafted by hand with basic tools, used in water mills and simple machinery.
- Industrial Revolution: The 18th century marked significant improvements with the introduction of steam power. Metal gears became more common, and gear cutting was still largely a manual process involving specialized craftsmen.
- Introduction of Machine Tools:
- 19th Century: The development of machine tools, such as the lathe and milling machine, revolutionized gear manufacturing. Gear shaping and hobbing techniques were developed, allowing for more precise and consistent production.
- Gear Hobbing: Introduced in the late 19th century, this method uses a specialized tool called a hob to progressively cut the gear teeth on a blank piece.
- Modern Advances and Precision Manufacturing:
- 20th Century: Advances in technology led to the introduction of electric and electronic controls, further enhancing precision in gear production. Gear grinding machines came into use to provide a smooth finish and meet the high precision required for modern machinery.
- Computer Numerical Control (CNC): By the late 20th century, CNC machines transformed gear manufacturing by automating many processes, leading to increased efficiency and precision. These systems allow for the programming of machinery to carry out complex tasks with minimal human intervention.
- Recent Developments and Future Trends:
- Digital Manufacturing: Today, digital technologies, including computer-aided design (CAD) and computer-aided manufacturing (CAM), are integral to gear production. These tools allow for the precise design and modification of gear profiles before actual manufacturing.
- Additive Manufacturing: 3D printing technologies are beginning to be explored for gear production, particularly for complex or custom gear shapes that are difficult to make with traditional methods.
- Automation and Robotics: The integration of robotics in gear manufacturing processes is aimed at further increasing precision and reducing labor costs, with robots performing tasks such as loading and unloading materials.
- Integration of Advanced Materials:
- High-Performance Alloys and Composites: The use of advanced materials such as titanium alloys, advanced steel grades, and composites is becoming more prevalent in gear manufacturing. These materials offer improved strength, wear resistance, and weight reduction, which are crucial for applications in aerospace, automotive, and industrial machinery.
- Material Science Innovations: Ongoing research in material science continues to introduce new materials that can withstand harsher environments and higher stresses. This research also includes the development of materials that are easier to machine and more environmentally friendly.
- Quality Control and Inspection Technologies:
- Precision Measurement Tools: As gears become more sophisticated, the tools used to measure and ensure their quality have also advanced. Technologies such as coordinate measuring machines (CMM) and laser scanning provide highly accurate inspections that are critical for ensuring the performance of precision gears.
- Real-Time Monitoring: With the advent of the Internet of Things (IoT) and sensors, gear manufacturing processes can now include real-time monitoring of gear quality during production. This allows for immediate adjustments to be made, reducing waste and improving the final product’s quality.
- Sustainable Manufacturing Practices:
- Energy Efficiency: Modern gear manufacturing facilities increasingly focus on reducing energy consumption by using more efficient machines and processes. This not only lowers costs but also reduces the environmental impact of manufacturing operations.
- Recycling and Reuse: There is a growing emphasis on recycling used gears and the materials from which they are made. Re-manufacturing and refurbishing old gears are becoming practical solutions for extending the life of these components and minimizing resource usage.
- Collaborative and Flexible Manufacturing Systems:
- Customization and Small-Batch Production: As market demands shift towards customization and small-batch production, gear manufacturers are adapting by implementing flexible manufacturing systems. These systems can quickly switch between different gear types and sizes without significant downtime or cost.
- Collaborative Robotics (Cobots): Collaborative robots, or cobots, are designed to work alongside human operators, assisting with complex or repetitive tasks in the gear manufacturing process. This collaboration can lead to safer work environments and more efficient production lines.
- Artificial Intelligence and Machine Learning:
- Predictive Maintenance: AI and machine learning are being applied to predict when machinery maintenance should occur, preventing costly downtimes and extending machine life. By analyzing data from machine operations, AI can forecast when parts will likely fail or require service.
- Process Optimization: Machine learning algorithms are also used to optimize manufacturing processes, improving the efficiency and quality of gear production. These systems analyze vast amounts of data to identify patterns and insights that humans might overlook, enabling continuous process improvements.
- Virtual Reality (VR) and Augmented Reality (AR):
- Design and Prototyping: VR and AR technologies are increasingly being used in the design and prototyping stages of gear manufacturing. These tools allow engineers to visualize and interact with gear designs in a virtual environment, facilitating a more intuitive understanding of complex geometries and interactions.
- Training and Maintenance: AR, in particular, offers significant benefits for training and on-the-job support. AR can overlay digital information and guidance directly onto real-world objects, helping technicians perform maintenance tasks or troubleshoot issues more effectively and quickly.
- Interconnectivity and Smart Factories:
- Industry 4.0: The concept of smart factories within Industry 4.0 is profoundly influencing gear manufacturing. These factories integrate cyber-physical systems, IoT, and cloud computing to create interconnected environments where machinery and equipment can communicate and operate semi-autonomously.
- Supply Chain Optimization: Enhanced connectivity not only optimizes production processes but also improves supply chain efficiency. Real-time data collection and analysis can predict supply needs, adjust production schedules, and manage logistics more dynamically, reducing inventory costs and increasing responsiveness.
- Customization at Scale:
- Mass Customization: Advances in manufacturing technology are enabling the mass customization of gears. Using flexible manufacturing systems and modular design principles, producers can offer customized gear solutions without the traditional cost and time penalties associated with custom production.
- Customer-Centric Manufacturing: This approach allows for greater flexibility in meeting specific customer requirements, whether for specialized machinery, vehicles, or consumer products, enhancing customer satisfaction and competitive advantage.
- Globalization and Localized Production:
- Decentralized Manufacturing: To meet global demand more effectively, gear manufacturing is seeing a trend towards decentralized production. This strategy involves setting up smaller, localized production units closer to key markets, which helps reduce shipping costs and times and improves supply chain resilience.
- Nearshoring and Reshoring: Driven by geopolitical uncertainties and the need for more reliable supply chains, many companies are reshoring or nearshoring their manufacturing operations. This shift not only mitigates risks but also complies with national regulations and consumer preferences for locally made products.
- Regulatory Compliance and Environmental Responsibility:
- Regulations and Standards: As the global emphasis on sustainability grows, gear manufacturers must navigate an increasing array of environmental regulations and standards. Compliance is essential not only for market access but also for corporate responsibility.
- Eco-Friendly Manufacturing: Efforts to reduce the environmental footprint include adopting cleaner production technologies, minimizing waste through lean manufacturing, and using renewable energy sources. These practices not only comply with regulatory demands but also appeal to environmentally conscious consumers and investors.
Each step in the evolution of gear manufacturing has been driven by the need for greater precision, efficiency, and adaptation to new materials and demands. Future developments will likely continue to focus on the integration of technology and sustainability, pushing the boundaries of what’s possible in gear production.
As we move forward, the evolution of gear manufacturing will continue to integrate these technological, ecological, and economic trends. This integration will likely lead to even more innovative approaches to gear production, aimed at improving efficiency, sustainability, and adaptability in a rapidly changing world.