AI technology is revolutionizing the field of gear manufacturing, a critical component of precision engineering. Here are some of the ways in which gear manufacturer is pioneering the use of AI:
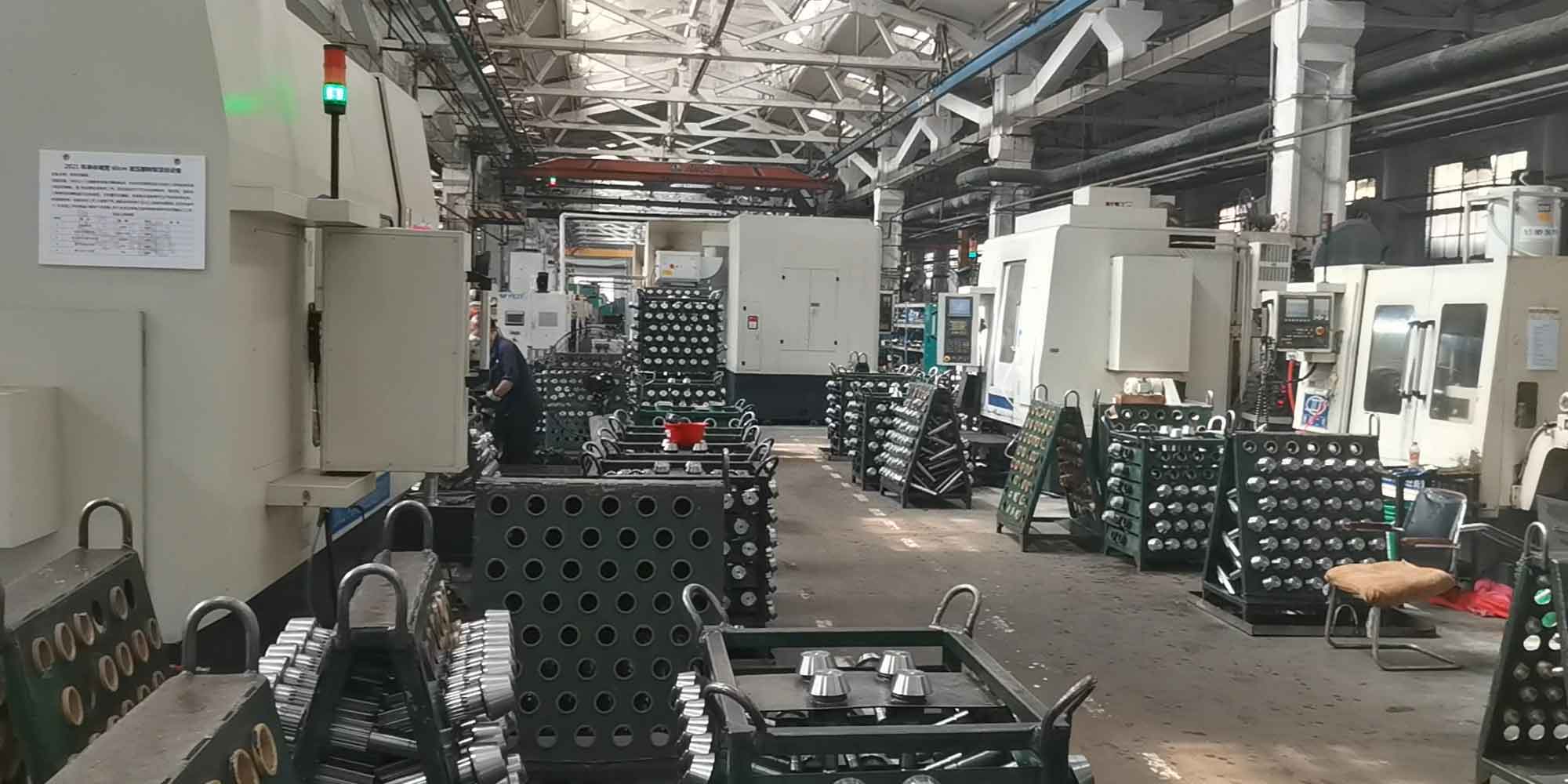
- Design Optimization: AI algorithms can analyze complex data and simulations to optimize gear designs for enhanced performance and durability. This includes optimizing tooth geometry, material selection, and load distribution, which can significantly improve the efficiency and lifespan of gears.
- Predictive Maintenance: AI-driven predictive maintenance uses sensors and machine learning to monitor the condition of gear machinery in real time. By predicting when a machine is likely to fail or when a gear is wearing out, gear manufacturer can perform maintenance before breakdowns occur, reducing downtime and maintenance costs.
- Quality Control: AI can automate the quality control process by analyzing images or data collected during gear manufacturing. Advanced image recognition and machine learning models can detect even minute defects in gears, ensuring that only parts meeting stringent quality standards are dispatched.
- Supply Chain Optimization: AI can also be used to optimize the supply chain, from raw material procurement to delivery of the final product. By analyzing trends and patterns, AI helps in predicting demand, managing inventory, and planning production schedules more efficiently.
- Robotics and Automation: In gear manufacturing, robotics equipped with AI are being used for tasks such as assembly, welding, and cutting. AI enhances the precision of robots, allowing them to perform complex tasks that require adaptability and fine control.
- Customization: AI enables more flexible and scalable production capabilities, allowing for cost-effective customization of gears. Using AI, gear manufacturer can easily switch production processes to create custom gears for specific applications without significant downtime or retooling costs.
- Simulation and Testing: AI technologies facilitate advanced simulation models that predict how gears will perform under various conditions without the need for physical prototypes. This virtual testing can save time and resources, speed up the development process, and ensure that the gears will operate reliably in their intended applications. Machine learning models can be trained with historical data to forecast potential failure points and stress areas in gear designs.
- Energy Efficiency: AI can also be employed to optimize the energy consumption of gear manufacturing processes. By analyzing operational data, AI algorithms can identify inefficiencies and suggest adjustments to machine settings that reduce energy usage without compromising performance, aligning with sustainability goals.
- Integrating IoT with AI: The integration of the Internet of Things (IoT) with AI in gear manufacturing brings about smarter factories. Sensors on equipment can feed real-time data to AI systems, which then analyze the data to optimize production processes, improve machine efficiency, and reduce waste. This connected network of machines and systems allows for a more responsive and integrated gear manufacturing environment.
- Employee Training and Safety: AI-driven tools are also enhancing the way employees are trained, offering virtual reality (VR) and augmented reality (AR) training that simulates gear manufacturing environment. These tools help workers learn in a risk-free setting, enhancing safety and proficiency. AI can also monitor work environments to identify safety hazards, alerting employees and management in real-time to potential risks.
- Market Analysis and Customer Insights: AI can analyze market trends and consumer behavior to provide gear manufacturers with valuable insights into customer needs and preferences. This information can guide product development and marketing strategies, allowing gear manufacturer to better align their offerings with market demands.
- Collaborative AI: Some gear manufacturer is exploring the use of collaborative AI, where AI systems work alongside human engineers to design and manufacture gears. This collaboration can lead to innovative solutions that would not be possible with either humans or AI alone, leveraging the creative problem-solving skills of humans and the computational power of AI.
By harnessing the capabilities of AI, gear manufacturer is not only enhancing their production techniques but also driving forward the future of the entire manufacturing sector. This technological advancement leads to higher productivity, reduced costs, improved safety, and greater innovation, ultimately benefiting both gear manufacturer and their customers.