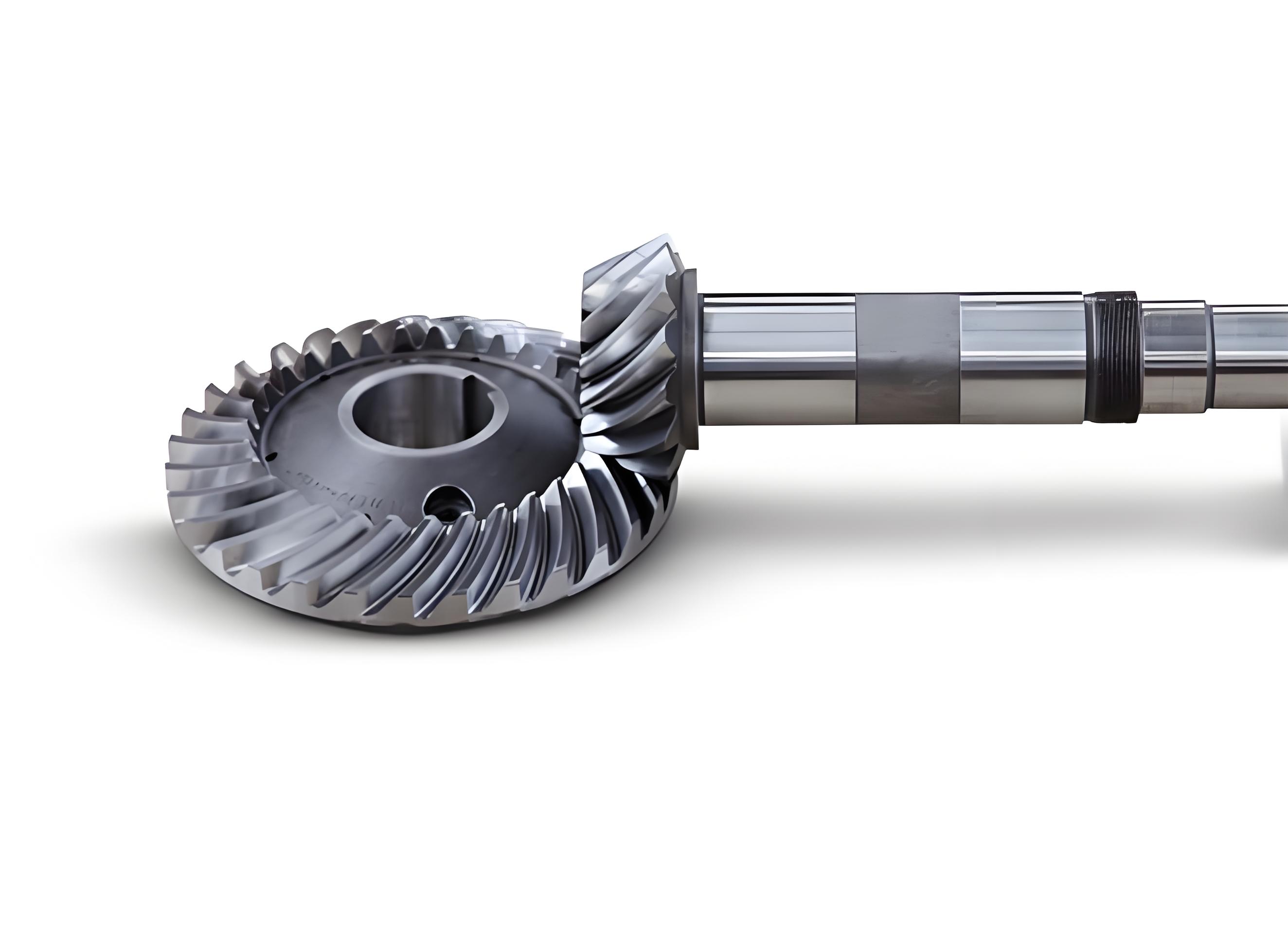
Abstract
The integration of real-time monitoring and predictive maintenance techniques for spiral bevel gear in industrial applications is essential for optimizing performance, minimizing downtime, and extending spiral bevel gear life. This review explores various monitoring technologies, data analysis methods, and predictive maintenance strategies tailored to spiral bevel gear.
Introduction
Spiral bevel gear is critical components in many industrial systems, including automotive, aerospace, and heavy machinery. Their complex geometry and high load-bearing capacity make them susceptible to wear and failure if not properly monitored and maintained. Real-time monitoring and predictive maintenance can prevent unexpected breakdowns, reduce maintenance costs, and improve operational efficiency. This review examines the latest advancements and applications in these fields.
Real-Time Monitoring Technologies
- Vibration Analysis
- Technique: Using accelerometers and vibration sensors to detect anomalies in spiral bevel gear movement.
- Benefits: Identifies issues such as misalignment, imbalance, and spiral bevel gear tooth damage.
- Applications: Commonly used in high-speed and high-load spiral bevel gear systems.
- Acoustic Emission
- Technique: Monitoring high-frequency sound waves produced by spiral bevel gear during operation.
- Benefits: Detects early signs of wear and crack propagation.
- Applications: Effective for early fault detection in noisy environments.
- Oil Analysis
- Technique: Analyzing lubricants for contaminants and wear particles using spectrometry and ferrography.
- Benefits: Provides information on spiral bevel gear condition and lubrication effectiveness.
- Applications: Used in systems where oil health is critical for spiral bevel gear performance.
- Thermography
- Technique: Using infrared cameras to measure temperature distribution across spiral bevel gear surfaces.
- Benefits: Detects overheating, friction, and lubrication issues.
- Applications: Useful in monitoring spiral bevel gear in high-temperature environments.
- Strain Gauges
- Technique: Measuring strain on spiral bevel gear teeth under load to assess stress distribution.
- Benefits: Identifies overloads and potential failure points.
- Applications: Suitable for highly stressed spiral bevel gear applications.
Data Analysis Methods
- Machine Learning Algorithms
- Approach: Using supervised and unsupervised learning to analyze sensor data and identify patterns indicative of spiral bevel gear faults.
- Benefits: Provides predictive insights and anomaly detection.
- Applications: Enhances the accuracy of fault diagnosis and predictive maintenance.
- Statistical Analysis
- Approach: Applying statistical methods to sensor data to identify trends and deviations.
- Benefits: Simplifies data interpretation and highlights significant changes in spiral bevel gear behavior.
- Applications: Useful for establishing baseline conditions and threshold limits.
- Time-Frequency Analysis
- Approach: Using techniques such as Fast Fourier Transform (FFT) and Wavelet Transform to analyze signal characteristics over time.
- Benefits: Detects transient and periodic faults.
- Applications: Effective for diagnosing complex spiral bevel gear issues in variable operating conditions.
- Digital Twin Technology
- Approach: Creating a virtual model of spiral bevel gear system that replicates its physical counterpart using real-time data.
- Benefits: Enables simulation of different scenarios and proactive maintenance planning.
- Applications: Widely used in high-stakes industries like aerospace and heavy machinery.
Predictive Maintenance Strategies
- Condition-Based Maintenance (CBM)
- Strategy: Performing maintenance actions based on real-time condition monitoring data.
- Benefits: Reduces unnecessary maintenance and prevents unexpected failures.
- Applications: Ideal for systems where continuous monitoring is feasible.
- Prognostics and Health Management (PHM)
- Strategy: Predicting future spiral bevel gear failures and remaining useful life (RUL) using advanced analytics.
- Benefits: Allows for strategic maintenance scheduling and resource allocation.
- Applications: Crucial for mission-critical applications with high reliability requirements.
- Reliability-Centered Maintenance (RCM)
- Strategy: Developing maintenance plans based on reliability data and failure modes.
- Benefits: Optimizes maintenance activities to improve system reliability and performance.
- Applications: Used in industries where maximizing uptime is essential.
Case Studies
- Automotive Industry
- Application: Real-time monitoring of transmission spiral bevel gear using vibration analysis and oil sensors.
- Outcome: Improved detection of spiral bevel gear wear and timely maintenance, reducing vehicle downtime.
- Aerospace Sector
- Application: Implementation of digital twin technology for aircraft gearboxes.
- Outcome: Enhanced predictive maintenance capabilities, leading to increased flight safety and reduced maintenance costs.
- Heavy Machinery
- Application: Using thermography and strain gauges to monitor spiral bevel gear in mining equipment.
- Outcome: Early detection of overheating and stress-related issues, extending spiral bevel gear life and preventing catastrophic failures.
Conclusion
The integration of real-time monitoring and predictive maintenance for spiral bevel gear in industrial applications offers significant benefits in terms of operational efficiency, cost savings, and system reliability. By leveraging advanced sensor technologies, data analysis methods, and predictive maintenance strategies, industries can ensure the optimal performance and longevity of their gear systems.
References
- IEEE Transactions on Industrial Informatics: Research on real-time monitoring technologies and data analysis methods for industrial applications.
- Journal of Mechanical Engineering Science: Articles on predictive maintenance strategies and their impact on gear performance.
- Tribology International: Studies on the role of lubrication and oil analysis in gear maintenance.
- Journal of Vibration and Control: Papers on vibration analysis and acoustic emission techniques for fault detection.
This review provides a comprehensive overview of the latest techniques and strategies for real-time monitoring and predictive maintenance of spiral bevel gears, offering valuable insights for engineers, researchers, and industry professionals.