Straight bevel gears are essential mechanical components that transmit torque through the meshing of the tooth profiles of the gears, similar to the function of straight cylindrical gears. However, compared to straight cylindrical gears, bevel gears have several advantages. Firstly, the installation shaft of bevel gears can have any angle between 0° and 90°. Secondly, bevel gears operate more smoothly and transmit more torque than cylindrical straight gears. Lastly, the modulus of straight bevel gears varies from one end to the other of the full tooth width.
Bevel gears are also used in pairs. When inspecting gear components, some inspection parameters require the detection of individual gears, such as tooth height, common normal length, chordal tooth thickness, etc. However, there are other parameters that can only be detected when the gears are paired and meshed, such as sub-cone angle detection, shaft intersection angle detection, contact spot detection, tooth surface backlash detection, and tooth tip clearance detection, etc.
If paired gears are assembled on the product without undergoing pairing inspection and problems with the tooth surface meshing are found, disassembly can be quite cumbersome. This is because generally, straight bevel gears and the matching transmission shafts are assembled together through interference or transition fits by means of hot or cold installation, with a relatively tight fit. Secondary disassembly is more troublesome. Therefore, it is necessary for us to design a tooling for bevel gear meshing to inspect the detection elements in the case of gear meshing in advance.
1. Product Introduction
Our company is one of the main manufacturers of rubber and plastic machinery in China, including internal mixers, twin-screw extruders, flat vulcanizing machines, tire vulcanizing machines, etc. The object of our study here is the main transmission component on the twin-screw extruder, the synchronous bevel gear, with the specific model of 416 single-hung double-cone twin-screw extruder. As shown in Figure 1, it belongs to the straight bevel gear with equal top clearance, with 48 teeth, a pressure angle of 20°, a sub-cone angle of 7°, a large-end modulus of 20 mm, a designed common normal length of 338.14 mm, and an assembly backlash of 0.5 mm. In our actual assembly process, we often encounter such a situation. After the two matching bevel gears are assembled, when checking the backlash on the meshing and non-meshing surfaces with a feeler gauge, it is found that the backlash at the large end of the bevel gear is different from that at the small end, and the difference is relatively large. Therefore, when the gears are meshing and transmitting, the contact along the tooth width is not sufficient, and the contact spot is smaller than the design requirement. This will cause the tooth surface wear of the matching bevel gears to be different, the wear of the contact part will intensify, while the non-contact area will not wear or have slight wear, seriously affecting the transmission effect and working life of the bevel gears. For this problem that affects the assembly quality, we cannot eliminate all unqualified items outside the assembly link by relying solely on the quality inspection of individual bevel gears. Moreover, once unqualified bevel gears are installed on the product, it is time-consuming and laborious for the assembly workers to disassemble them, and it is easy to damage the self-aligning roller bearings or the transmission shaft. This is the reason why we design the bevel gear meshing tooling.
2. Tooling Structure
The designed bevel gear meshing tooling is shown in Figures 2 and 3:
1 – Base; 2 – Guide Rail; 3 – Slider; 4 – Mounting Plate; 5 – Pin Shaft; 6 – Bracket; 7 – Fixed Block; 8 – Spacer Sleeve; 9 – Support Bolt; 10 – Round Nut; 11 – Spacer Ring; 12 – Cylindrical Self-aligning Roller Bearing; 13 – Cylindrical Thrust Roller Bearing; 14 – Mounting Shaft; 15 – Key; 16 – Bevel Gear
3. Tooling Operating Steps
(1) Before installing the bevel gear, restore the fixed block to the horizontal state.
(2) Install the bevel gear (No. 16). It should be noted that the inner hole mating surface of the bevel gear needs to be coated with lubricating oil before installation. In addition, as a detection tooling, here we need to modify the fit size between the outer diameter of the mounting shaft and the inner hole of the bevel gear from the interference or transition fit in the drawing design to a clearance fit, and appropriately reduce the outer diameter of the mounting shaft. These steps are all helpful for us to install and disassemble the bevel gear smoothly.
(3) Install the key (No. 15) to fix the bevel gear and the mounting shaft to prevent a single bevel gear from rotating freely around the mounting shaft.
(4) Check the pre-tightening round nut (No. 10) at the tail of the mounting shaft to prevent the inner and outer rings of the self-aligning roller bearing used for positioning below the tooling from loosening during assembly.
(5) According to the sub-cone angle designed in the bevel gear drawing, adjust the support bolt (No. 9) to drive the fixed block (No. 7) to rotate around the pin shaft (No. 5) to achieve the sub-cone angle. When the sub-cone angle is 0°, the straight cylindrical gears can be paired and checked.
(6) Move the bracket (No. 6) along the guide rail to smoothly mesh the two bevel gears together.
(7) Lock the locking slider (No. 3) to fix the bracket and prevent the bracket from displacing laterally along the guide rail (No. 2).
(8) Through the hexagonal wrench inner hole at the end face of the mounting shaft (No. 14), the two meshing gears can easily realize manual meshing rotation around the shaft.
4. Main Parameters and Application Range
(1) Overall Dimensions: 2000 mm × 1020 mm × 1300 mm
(2) Application Range of the Tooling: Straight Cylindrical Gears, Straight Bevel Gears
(3) Adjustable Sub-cone Angle Range of the Tooling: 0 – 20°
(4) Gear Diameter Range: Ф800 – Ф1200
(5) Maximum Bearing Weight of the Gear: 5 t/piece
5. Meshing Detection Analysis of Straight Bevel Gears
In addition to the tooth profile, the meshing of straight bevel gears is mainly affected by two parameters, one is the cone distance, and the other important parameter is the sub-cone angle. The cone distance determines the position of the meshing pair of bevel gears on the rotating shaft, similar to the center distance parameter of cylindrical gears. The difference is that the centers of cylindrical gears are parallel to each other, while the centers of bevel gears form a certain angle. The cone distance is a parameter given by the design, and we can adjust the cone distance to adjust the backlash of the meshing tooth surface. Moving towards the small end of the bevel gear, the backlash becomes smaller, and vice versa. However, this only works when the sub-cone angles of the two bevel gears are consistent. If the sub-cone angles of the paired bevel gears are inconsistent, the effect of adjusting the tooth surface backlash by adjusting the cone distance will disappear.
The sub-cone angle is a parameter that reflects the angle between the center of the bevel gear and the straight line of the reference circle. It directly determines the size of the contact spot area of the tooth surfaces of the two known bevel gears, thereby determining the quality of power transmission at the meshing surface. Practice shows that the sub-cone angle will appear in the following four situations during the assembly of bevel gears:
The first is the ideal meshing state of bevel gears, as shown in Figure 4. In this case, the straight lines of the reference circles of the two bevel gears will overlap, the tooth surface backlash will be completely eliminated, and the backlash on the meshing and non-meshing surfaces of the tooth surface will be zero. In practical applications, considering the existence of processing errors and the situation where the meshing teeth are prone to jamming under zero backlash, this situation is basically not adopted.
The second is the meshing state of bevel gears in a parallel state, as shown in Figure 5. It refers to the case where the backlash on the meshing surface of the gear is zero before and after, while a certain backlash value is left on the non-meshing surface, and the backlash value at the front and rear positions of the bevel gear along the tooth width direction is equal. The specific backlash value is determined by the designer according to the processing accuracy level of the gear itself and the operating conditions. If the measured backlash value of the actually paired bevel gears is larger than the design requirement, it means that the two gears need to move a certain distance inward along the axial direction; conversely, if the measured backlash value is smaller than the design requirement, the two gears need to move a certain distance outward along the axial position. This distance adjustment is generally achieved by adjusting the width of the two spacer sleeves installed at the front and rear positions of the bevel gear.
The third is the meshing state of bevel gears when the sub-cone angle is too large, as shown in Figure 6. In this state, the measured backlash value at the small end of the bevel gear is smaller than that at the large end of the bevel gear using a feeler gauge, and the backlash values on the meshing and non-meshing surfaces at the large end of the tooth side are not zero. This indicates that the meshing situation of such paired bevel gears is not ideal at all, and only a part of the tooth surface at the small end of the bevel gear can effectively transmit power, which will inevitably lead to intensified wear of the contact tooth surface, greatly reducing the service life of the bevel gear, and irregular abnormal meshing noise will occur during operation. Once this situation occurs, the bevel gear can only be directly scrapped, or for some cases where the deviation of the backlash value is not large, it can be manually repaired and then used as a defective product for downgrading.
The fourth is the meshing state of bevel gears when the sub-cone angle is too small, as shown in Figure 7. This state is just the opposite of the previous one. The measured backlash value at the small end of the bevel gear is larger than that at the large end of the bevel gear using a feeler gauge, and the backlash values on the meshing and non-meshing surfaces at the small end of the tooth side are not zero. This indicates that only a part of the tooth surface at the large end of the bevel gear is in normal contact, which will also cause the same problems as shown in Figure 6, and the processing method can also refer to the third one.
6. Summary
Gear pairing meshing inspection is very necessary, and its results cannot directly reflect whether the quality requirements of a certain individual item in the gear processing process are qualified. It is only an inspection of the assembly quality of gear meshing. In addition to being directly affected by the tooth profile itself, the meshing detection of bevel gears is mainly affected by the cone distance and the sub-cone angle. We can eliminate the tooth profile through single-piece inspection using a tooth profile template; the cone distance is a fixed value given by the design and has no impact on the bevel gear itself once determined; the only remaining determining factor is the sub-cone angle. Our reference circle is a virtual circle, and it is difficult to measure its specific size in practice, let alone the sub-cone angle based on the reference circle. This tooling can not only help us detect the size of the tooth surface backlash of the two bevel gears meshing before formal assembly, but also calculate and adjust the pitch of the bevel gear according to the actual measured backlash value to achieve an ideal gear meshing state.
Now, let’s take a look at the following table summarizing the key information about the bevel gear and the tooling:
Parameter | Details |
---|---|
Gear Model | 416 single-hung double-cone twin-screw extruder |
Gear Type | Straight bevel gear with equal top clearance |
Number of Teeth | 48 |
Pressure Angle | 20° |
Sub-cone Angle | 7° |
Large-end Modulus | 20 mm |
Designed Common Normal Length | 338.14 mm |
Assembly Backlash | 0.5 mm |
Tooling Dimensions | 2000 mm × 1020 mm × 1300 mm |
Application Range of Tooling | Straight cylindrical gears, straight bevel gears |
Adjustable Sub-cone Angle Range of Tooling | 0 – 20° |
Gear Diameter Range | Ф800 – Ф1200 |
Maximum Bearing Weight of Gear | 5 t/piece |
In conclusion, the design and application of this bevel gear meshing detection tooling play a crucial role in ensuring the quality and performance of bevel gear transmissions. By accurately detecting and adjusting the meshing parameters, we can improve the reliability and efficiency of the gear system, reducing the risk of failures and improving the overall performance of the machinery.
Furthermore, the recent anti-dumping investigations launched by Thailand, Brazil, and Türkiye against Chinese tires and rubber products highlight the importance of international trade regulations and fair competition. These investigations may have an impact on the export of related products and require manufacturers and exporters to closely monitor the situation and take appropriate measures to respond.
For example, in the case of Thailand’s initiation of the second anti-dumping sunset review investigation on motorcycle rubber inner tubes originating from China, it is essential for Chinese manufacturers to closely follow the progress of the investigation and provide relevant evidence to defend their interests. Similarly, Brazil’s reassessment of the anti-dumping measures against truck and bus tires from China requires attention to ensure that the rights and interests of Chinese enterprises are protected.
In the case of Türkiye’s initiation of the anti-circumvention investigation against vulcanized rubber conveyor belts from China, it is necessary for Chinese exporters to ensure that their trade practices comply with relevant regulations and avoid any actions that may be suspected of circumvention.
Overall, the combination of advanced tooling design and compliance with international trade rules is crucial for the sustainable development of the manufacturing industry in the global market. By continuously improving the quality and technology of products and adhering to fair trade principles, enterprises can better cope with various challenges and seize opportunities for development.
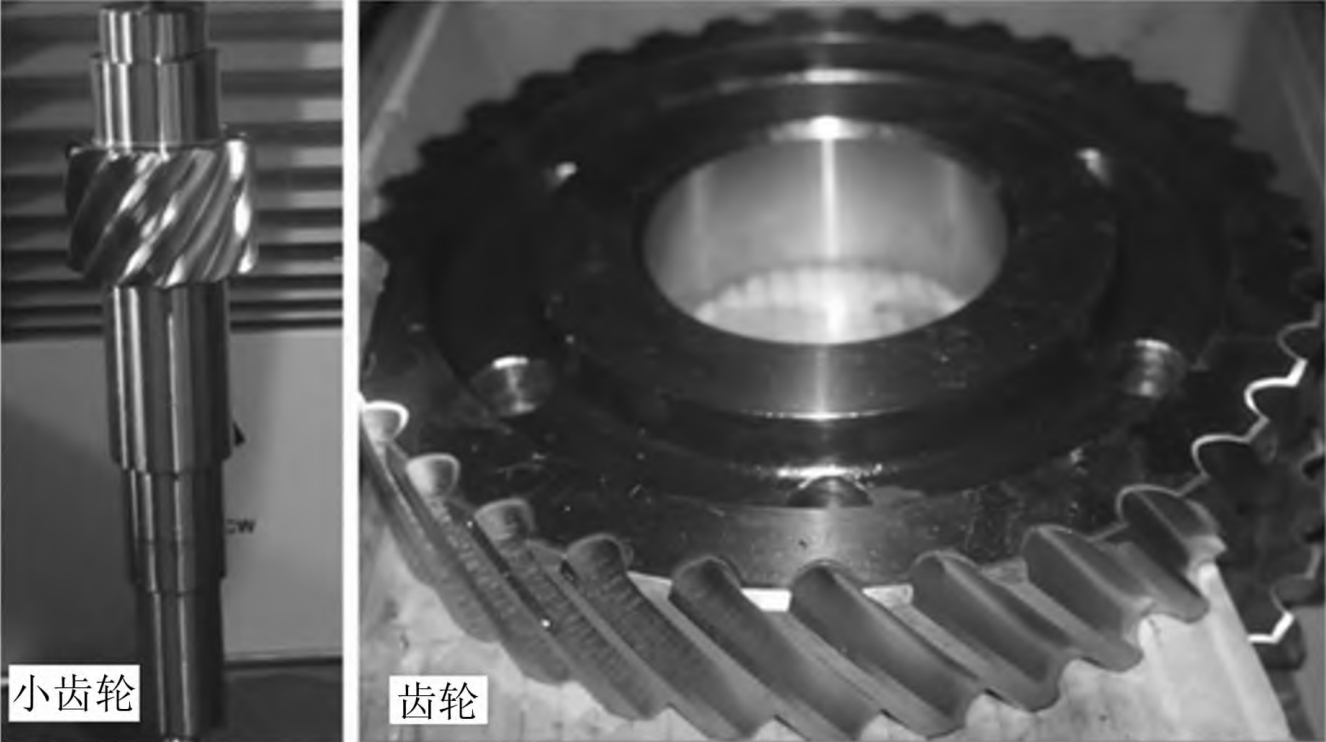