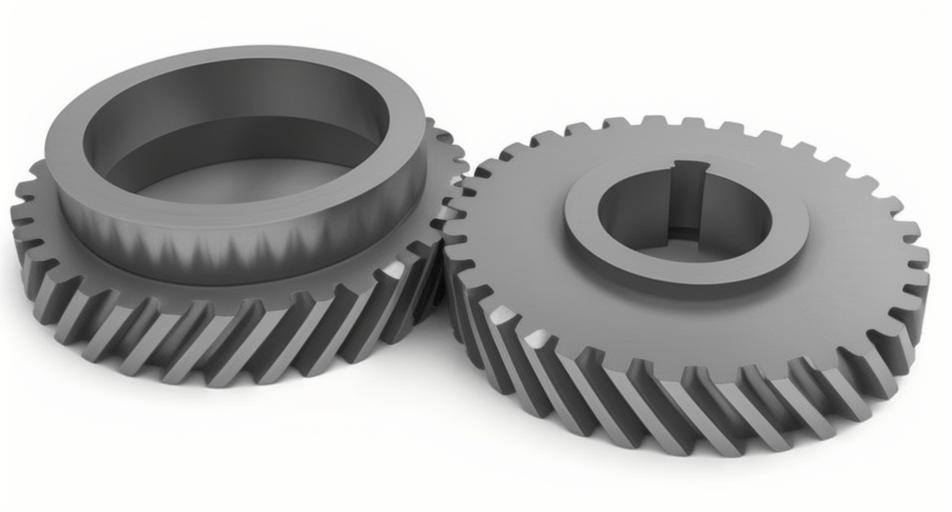
Helical gear is a fundamental component in many mechanical systems, known for their ability to transfer motion and power between non-parallel shafts efficiently and quietly. The manufacturing of high-tolerance helical gear requires precision techniques to ensure optimal performance, durability, and reliability. This article explores various precision manufacturing techniques employed to produce high-tolerance helical gear.
1. Gear Hobbing
Gear hobbing is a versatile and widely used process for manufacturing helical gear. It involves a rotating hob, which is a specialized cutting tool, and the gear blank. The hob cuts the gear teeth as it rotates, allowing for the creation of helical teeth with precise angles and tolerances. The key advantages of gear hobbing include its efficiency, ability to produce high-quality helical gear, and suitability for both small and large-scale production.
2. Gear Grinding
Gear grinding is a finishing process that ensures the highest level of precision and surface finish for helical gear. This technique uses abrasive wheels to remove small amounts of material from the gear teeth, correcting any deviations and achieving the desired tolerance. Gear grinding is particularly essential for high-performance applications where accuracy and surface quality are critical.
3. Gear Shaping
Gear shaping is another method for producing helical gear with high precision. In this process, a reciprocating cutter shapes helical gear teeth through successive cuts. Gear shaping is highly effective for internal gears and gears with complex geometries. It provides excellent control over helical gear profile and helix angle, making it suitable for high-tolerance requirements.
4. Gear Skiving
Gear skiving is a modern and efficient method for manufacturing helical gear. This technique involves the use of a skiving tool that simultaneously cuts and removes material, producing helical teeth with high precision. Gear skiving is known for its speed, accuracy, and ability to produce helical gear with complex profiles. It is particularly useful for manufacturing gears with small diameters and high helix angles.
5. Heat Treatment
Heat treatment is a crucial step in the manufacturing of high-tolerance helical gear. Processes such as carburizing, quenching, and tempering enhance the mechanical properties of helical gear, including hardness, strength, and wear resistance. Precision control of the heat treatment process ensures that the gears meet the required tolerances and performance specifications.
6. Quality Control and Inspection
Quality control and inspection are vital to ensure that helical gear meet high-tolerance standards. Techniques such as coordinate measuring machines (CMM), gear measurement systems, and surface roughness testers are used to verify the dimensions, profile, and surface finish of helical gear. Consistent quality control throughout the manufacturing process ensures that each gear meets the stringent requirements for high-tolerance applications.
Table: Comparison of Precision Manufacturing Techniques for Helical Gear
Technique | Advantages | Applications | Key Characteristics |
---|---|---|---|
Gear Hobbing | Efficient, high-quality production | Small and large-scale production | Versatile, precise angle control |
Gear Grinding | High precision, excellent surface finish | High-performance applications | Removes material for fine-tuning |
Gear Shaping | Effective for internal gears, complex geometries | Internal gears, complex profiles | Reciprocating cutter for profile control |
Gear Skiving | Fast, accurate, complex profiles | Small diameters, high helix angles | Simultaneous cutting and material removal |
Heat Treatment | Enhanced hardness, strength, wear resistance | All gear manufacturing stages | Precision control of mechanical properties |
Quality Control | Ensures high-tolerance standards | All stages of manufacturing | CMM, gear measurement systems |
In conclusion, the precision manufacturing of high-tolerance helical gear involves a combination of advanced techniques and rigorous quality control measures. By employing methods such as gear hobbing, grinding, shaping, skiving, and heat treatment, manufacturers can produce gear that meet the demanding requirements of modern mechanical systems. Consistent application of these techniques ensures the production of reliable, durable, and high-performance helical gear.