Abstract
Due to the complex coupling vertical vibrations in automotive rear axles, precise detection of wear in spiral bevel gears remains challenging. This paper proposes a novel method for wear detection in automobile spiral bevel gears utilizing Delaunay triangulation. By scanning the gear surface to collect discrete data, Delaunay triangulation is applied to adjacent scan lines, segmenting non-characteristic discrete data and enabling a comprehensive description of the gear surface area. Subsequently, the Local Mean Decomposition (LMD) algorithm, based on Hermite interpolation, traverses and calculates the amplitude of the Product Function (PF) components of the triangular meshes, facilitating the detection of gear wear faults. Experimental results indicate that the proposed method accurately aligns with measured wear depth and rate, effectively detects wear area with up to 98.7% accuracy, demonstrating its effectiveness in detecting gear wear.
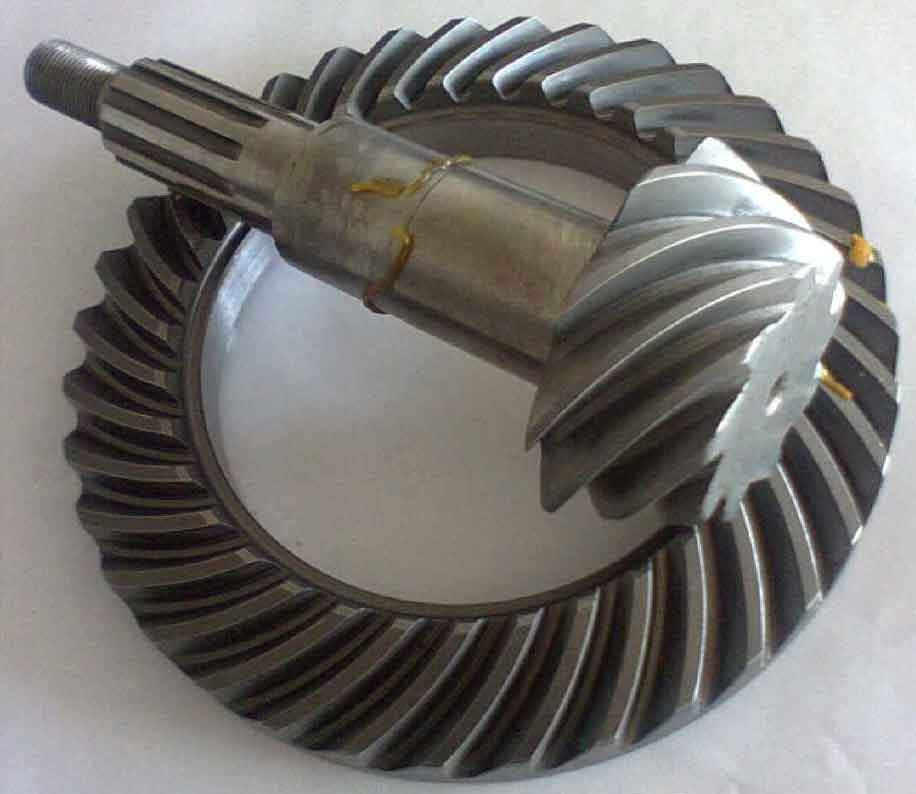
1. Introduction
Automobiles have become indispensable in modern life, with gears playing a crucial role in transmitting power and motion. However, as vehicles age, wear in the spiral bevel gears, particularly those in the rear axle, becomes increasingly evident due to coupling vertical vibrations. This wear can significantly compromise driving safety if left undetected. Thus, researching efficient gear wear detection methods to improve accuracy and safety is imperative.
Existing methods, such as wavelet packet energy analysis and modulation signal bispectrum sideband estimation [1], and reverse engineering-based techniques [2], have limitations in noise reduction and detection precision. Similarly, methods utilizing Mask Scoring R-CNN [3] struggle with data denoising, reducing overall detection accuracy. To address these issues, this paper introduces a Delaunay triangulation-based approach for precise wear detection in automobile spiral bevel gears.
2. Delaunay Triangulation for Non-Characteristic Discrete Data Segmentation
2.1 Background on Delaunay Triangulation
Delaunay triangulation is a widely used technique in computational geometry, characterized by ensuring that no point lies within the circumcircle of any triangle formed in the triangulation. This property guarantees optimal triangulation across a point set, making it suitable for describing complex surfaces like spiral bevel gears.
2.2 NURBS Surface Modeling
Non-Uniform Rational B-Splines (NURBS) surfaces are frequently used to model complex geometries like automobile spiral bevel gears. The NURBS surface equation is defined as:
A(u,v)=i=0∑qj=0∑mNi,p(u)Nj,q(v)ωijPij
where Ni,p(u) and Nj,q(v) are the B-spline basis functions of degree p and q in the u and v parametric directions, respectively; ωij are the weights; and Pij are the control points.
2.3 Delaunay Triangulation for Gear Surface Data
To segment the non-characteristic discrete data from the gear surface, Delaunay triangulation is applied to adjacent scan lines. The process involves connecting starting and ending points of adjacent scan lines, followed by connecting each measurement point on one line to its nearest point on the other line, effectively partitioning the area into triangles and quadrilaterals. The quadrilaterals are then further triangulated based on the minimum internal angle maximization criterion.
3. Hermite Interpolation-Based Gear Wear Detection
To accurately identify wear regions, the segmented triangular meshes from Delaunay triangulation are analyzed using Hermite interpolation within the LMD framework.
3.1 Local Mean Decomposition (LMD)
LMD is an adaptive time-frequency analysis method that decomposes a signal into a finite number of Product Functions (PFs) and a residual trend [4]. Each PF represents an Amplitude Modulation-Frequency Modulation (AM-FM) component.
3.2 Wear Detection Steps
- Noise Reduction: Convert the raw, noisy discrete data c(y) into a small parameter form and apply cascaded bistable stochastic resonance (CBSR) for denoising, yielding cn(y).
- Extrema Extension: Extend the extrema points ml of cn(y) to generate a new sequence cl.
- Envelope Estimation: Generate upper and lower envelopes Rup(y) and Rdown(y) using Hermite interpolation from the extrema of cl.
- Local Mean and Envelope Estimate Functions:q(y)=2Rup(y)+Rdown(y)s(y)=2∣Rup(y)−Rdown(y)∣
- PF Component Amplitude Calculation: Separate the envelope data from the original gear surface data using LMD and compute the PF component amplitudes:f_0(y) = \frac{12}}\right)where f0(y) is the PF component amplitude, and values outside the range [0, 1] indicate wear.
4. Experimental Analysis
To validate the proposed method, a comparative testing experiment was conducted using spiral bevel gears from a 2015 Santana manual automobile.
4.1 Experimental Setup
Twenty identical gears were tested under continuous operation for 200 hours, with data collected every 5 minutes. The equipment used included acoustic sensors, torque-speed sensors, and a test rig.
4.2 Data Collection and Processing
Wear data were analyzed for wear depth, wear rate, and wear area accuracy, comparing the proposed method with reverse engineering [2] and Mask Scoring R-CNN-based approaches [3].
4.3 Results
4.3.1 Wear Depth
Wear depth measurements at the tooth root and tip show the proposed method closely aligns with actual measurements, outperforming the comparison methods.
4.3.2 Wear Rate
The proposed method consistently matches the actual wear rate within a maximum error of 0.01 μm, while the comparison methods exhibit larger deviations .
4.3.3 Wear Area Detection Accuracy
The proposed method achieves up to 98.7% accuracy in detecting wear area, significantly surpassing the 79.4% and 84.3% accuracies of the comparison methods (Table 1).
Method | Maximum Wear Area Detection Accuracy (%) |
---|---|
Proposed | 98.7 |
Reverse Eng. | 79.4 |
Mask R-CNN | 84.3 |
Table 1: Wear Area Detection Accuracy
5. Conclusion
This paper introduces a Delaunay triangulation-based method for precise wear detection in automobile spiral bevel gears. By segmenting non-characteristic discrete data through Delaunay triangulation and applying Hermite interpolation within the LMD framework, the proposed method accurately identifies wear depth, rate, and area. Experimental results demonstrate the method’s effectiveness, achieving up to 98.7% accuracy in wear area detection. This approach enhances automobile driving safety and paves the way for future advancements in gear wear detection technology.