In the realm of spur gear manufacturing, precision is paramount. Tolerances—the permissible limits of variation in a physical dimension—play a critical role in ensuring that spur gear function correctly and reliably. The importance of tolerances in spur gear manufacturing cannot be overstated, as they directly impact the performance, efficiency, and longevity of gear systems. This article delves into the significance of tolerances in spur gear manufacturing, explaining how they influence gear quality and why meticulous adherence to specified tolerances is essential.
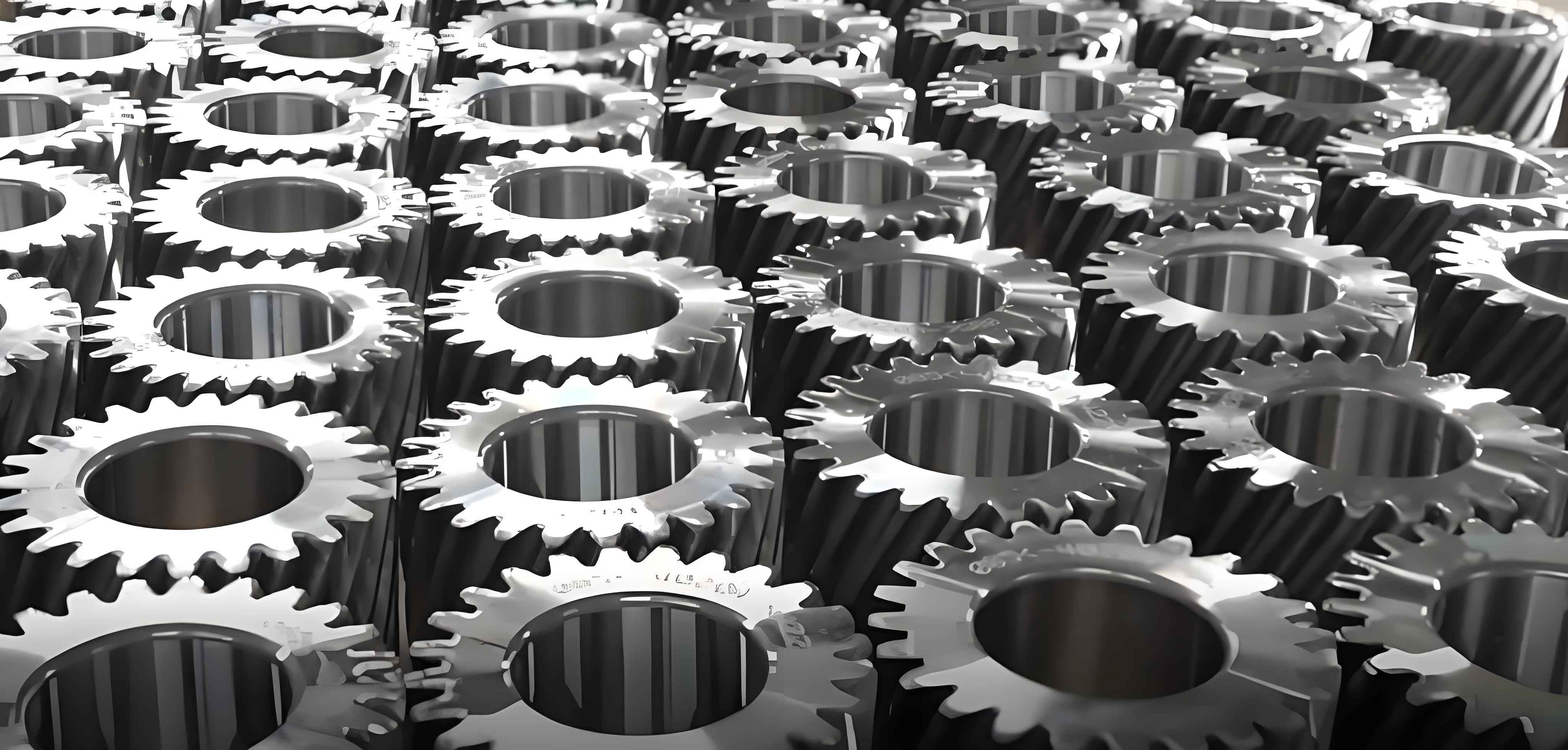
Understanding Tolerances in Spur Gear Manufacturing
Tolerances in spur gear manufacturing refer to the allowable deviations from the specified dimensions and geometries of the gears. These deviations can occur in various aspects of the gear, including tooth profile, pitch, diameter, and alignment. Adhering to precise tolerances ensures that the gears mesh correctly and perform their intended function without excessive noise, wear, or failure.
1. Dimensional Tolerances: These tolerances control the size and shape of the gear teeth and other critical dimensions. Maintaining tight dimensional tolerances is crucial for ensuring proper meshing and load distribution between gears.
2. Geometric Tolerances: These tolerances control the shape and relative positioning of the gear teeth, including parameters such as roundness, flatness, and concentricity. Geometric tolerances are vital for minimizing vibration and ensuring smooth operation.
3. Surface Finish Tolerances: The surface finish of the gear teeth affects friction, wear, and noise. Specifying precise surface finish tolerances helps optimize the performance and durability of the spur gear.
Table 1: Types of Tolerances in Spur Gear Manufacturing
Tolerance Type | Description | Importance |
---|---|---|
Dimensional Tolerances | Controls size and shape of gear teeth | Ensures proper meshing and load distribution |
Geometric Tolerances | Controls shape and relative positioning of teeth | Minimizes vibration and ensures smooth operation |
Surface Finish Tolerances | Controls texture and smoothness of gear surfaces | Optimizes friction, wear, and noise reduction |
The Impact of Tolerances on Spur Gear Performance
The importance of tolerances in spur gear manufacturing is evident in their direct impact on the performance and reliability of the gears. Tight tolerances are essential for achieving optimal gear function in several key areas:
1. Meshing Accuracy: Precise tolerances ensure that the gear teeth mesh correctly, which is critical for efficient power transmission. Incorrect meshing can lead to increased friction, noise, and wear.
2. Load Distribution: Proper load distribution across the gear teeth is essential for minimizing stress concentrations and preventing premature failure. Adhering to tight tolerances helps achieve uniform load distribution.
3. Vibration and Noise Reduction: Geometric tolerances are particularly important for minimizing vibration and noise in gear systems. Misalignment or deviations from the ideal tooth profile can cause excessive vibration and noise.
4. Wear Resistance: Surface finish tolerances impact the wear characteristics of the gear teeth. A smooth surface finish reduces friction and wear, extending the operational life of the spur gear.
5. Efficiency: Tighter tolerances lead to more efficient gear operation by reducing energy losses due to friction and misalignment. This results in lower operating costs and improved overall performance.
List: Key Impacts of Tolerances on Spur Gear Performance
- Meshing Accuracy: Ensures efficient power transmission and reduces friction.
- Load Distribution: Minimizes stress concentrations and prevents premature failure.
- Vibration and Noise Reduction: Reduces excessive vibration and noise.
- Wear Resistance: Extends operational life by minimizing wear.
- Efficiency: Improves energy efficiency and overall performance.
Table 2: Effects of Tolerance Deviations on Spur Gear Performance
Performance Aspect | Impact of Tolerance Deviations | Consequences |
---|---|---|
Meshing Accuracy | Incorrect meshing | Increased friction, noise, and wear |
Load Distribution | Uneven load distribution | Stress concentrations, premature failure |
Vibration and Noise Reduction | Increased vibration and noise | Reduced operational smoothness |
Wear Resistance | Higher friction and wear | Shortened gear life, increased maintenance |
Efficiency | Reduced operational efficiency | Higher energy consumption, increased costs |
Achieving Tight Tolerances in Spur Gear Manufacturing
Achieving and maintaining tight tolerances in spur gear manufacturing requires a combination of advanced manufacturing techniques, precise measurement, and rigorous quality control processes.
1. Advanced Manufacturing Techniques: Modern gear manufacturing techniques, such as Computer Numerical Control (CNC) machining, gear hobbing, and grinding, enable the production of gears with extremely tight tolerances and high precision.
2. Precision Measurement: Accurate measurement tools and techniques, including Coordinate Measuring Machines (CMMs) and optical profilometers, are essential for verifying that gears meet specified tolerances.
3. Quality Control: Implementing stringent quality control processes throughout the manufacturing process ensures that tolerances are consistently met. This includes regular inspection and testing of gears at various stages of production.
4. Material Selection: The choice of high-quality materials with uniform properties helps in maintaining consistent tolerances and achieving reliable gear performance.
5. Surface Treatments: Surface treatments such as heat treatment, coating, and superfinishing can improve the dimensional stability and surface quality of gears, helping to achieve tighter tolerances.
List: Strategies for Achieving Tight Tolerances in Spur Gear Manufacturing
- Advanced Manufacturing Techniques: Utilize CNC machining, gear hobbing, and grinding.
- Precision Measurement: Employ CMMs and optical profilometers for accurate measurement.
- Quality Control: Implement rigorous quality control processes and regular inspections.
- Material Selection: Use high-quality materials with uniform properties.
- Surface Treatments: Apply heat treatment, coating, and superfinishing for improved stability and quality.
Table 3: Techniques for Ensuring Tight Tolerances in Spur Gear Manufacturing
Technique | Description | Benefits |
---|---|---|
Advanced Manufacturing | CNC machining, gear hobbing, grinding | High precision, tight tolerances |
Precision Measurement | CMMs, optical profilometers | Accurate verification of tolerances |
Quality Control | Regular inspections and testing | Consistent adherence to specifications |
Material Selection | High-quality, uniform materials | Reliable and consistent gear performance |
Surface Treatments | Heat treatment, coating, superfinishing | Improved dimensional stability and surface quality |
Conclusion
The importance of tolerances in spur gear manufacturing is paramount for ensuring the performance, reliability, and efficiency of gear systems. Precise control of dimensional, geometric, and surface finish tolerances is essential for achieving accurate meshing, uniform load distribution, reduced vibration and noise, enhanced wear resistance, and overall operational efficiency. By employing advanced manufacturing techniques, precision measurement tools, rigorous quality control processes, high-quality materials, and surface treatments, manufacturers can achieve and maintain the tight tolerances necessary for high-performance spur gear. As the demand for precision and reliability in industrial applications continues to grow, the role of tolerances in spur gear manufacturing will remain a critical factor in the development of superior gear systems.