This paper focuses on the welding process of the spiral bevel gear cutter head with constant height teeth. Through in-depth analysis of the welding heat deformation theory, establishment of welding models, numerical simulation and experimental verification, the influence of welding parameters and groove gaps on the welding deformation of the cutter head is studied, aiming to optimize the welding process and improve the welding quality of the cutter head. The research content mainly includes the following aspects: Firstly, the basic theory of welding heat transfer and thermal elastic-plastic deformation is introduced, and the finite element method is used to analyze the welding process. Secondly, the welding model of the cutter head is established, and the appropriate welding heat source model and groove form are selected. Then, the Simufact.welding software is used to simulate the welding process of the cutter head, and the influence of different groove gaps on the welding deformation is analyzed. Finally, welding experiments are carried out to verify the reliability of the simulation results and optimize the welding process parameters. The research results show that the laser multi-layer wire filling welding method can effectively control the welding deformation of the cutter head, and the selection of the appropriate groove gap and welding process parameters can improve the welding quality of the cutter head.
1. Introduction
1.1 Gear Transmission and Spiral Bevel Gear
Gear transmission is widely used in mechanical engineering due to its stable and reliable operation, high efficiency, and long service life. Among various gears, the spiral bevel gear has unique advantages in transmitting motion and power between intersecting shafts. The spiral bevel gear with constant height teeth not only inherits the advantages of the spiral bevel gear but also has higher transmission efficiency, greater load-carrying capacity, lower energy consumption, and less noise during gear transmission. Therefore, it is widely used in automobiles (especially heavy-duty trucks), construction machinery, precision machine tools, and other fields, showing a good application prospect.
1.2 Manufacturing Method of Cutter Head
The manufacturing process of the spiral bevel gear with constant height teeth is relatively complex, and the cutter head used for processing it is usually a precision and complex tool. At present, there are mainly two processing methods for the cutter head: integral type and welding type. The integral type has high processing accuracy and long service life, but it requires high processing conditions and high cost, and the technology is monopolized by foreign countries. In contrast, the welding type has the advantages of simple processing method, easy realization, and relatively low cost. It is the main processing method adopted in China. However, in the welding process of the cutter head, due to the influence of the heat source, the welding temperature field is unevenly distributed, resulting in welding deformation of the cutter head, which affects the processing accuracy and service life of the cutter head. Therefore, it is of great significance to study the welding deformation of the spiral bevel gear cutter head with constant height teeth and improve the welding accuracy.
1.3 Research Status of Welding Simulation and Laser Welding
Welding is a complex physical and chemical process involving multiple disciplines such as metal metallurgy, material mechanics, heat transfer, and arc physics. In the past, the research on welding mainly relied on experimental methods, which were time-consuming, labor-intensive, and prone to waste of resources. With the development of computer technology, numerical simulation technology has emerged. By using numerical simulation, the welding process can be analyzed and predicted, which can save a lot of experimental costs and help us understand the essence of welding. At present, the research on welding numerical simulation at home and abroad mainly focuses on the finite element simulation of welding residual stress and deformation. By simulating the welding heat source, temperature field, clamping before welding, and heat treatment after welding, the finite element simulation data of welding residual stress and deformation can be obtained, and the most suitable welding scheme can be determined through theoretical research and experimental verification.
Laser welding is an important welding method, especially in the welding of the spiral bevel gear cutter head with constant height teeth. There are many research results on laser multi-layer welding of steel plates with a thickness of less than or equal to 40 mm in the world, which shows the potential of laser multi-layer welding of thick plates. However, in the actual welding process of the cutter head, there are still some problems, such as excessive welding power requirements and limited welding depth in laser deep penetration welding, and low production efficiency in multi-layer and multi-pass welding. Therefore, it is necessary to explore a more suitable welding method and process parameters.
2. Welding Heat Deformation Theory
2.1 Finite Element Method
The finite element method is a powerful numerical calculation and analysis method. It divides the system or the whole into a finite number of small units, analyzes each unit separately, and then combines all the units to establish a set of equations to simulate the behavior of the original system. In the welding research, the finite element method can be used to analyze the temperature field, stress field, and deformation of the welded parts. By establishing an appropriate finite element model and setting the material properties and boundary conditions, the welding process can be simulated and predicted. However, when using the finite element method, it is necessary to pay attention to the selection of the model size and the grid division method to ensure the accuracy of the calculation results while reducing the calculation time and computer load.
2.2 Welding Temperature Field
2.2.1 Heat Transfer Basics
Heat transfer occurs when there is a temperature difference. In the welding process of the cutter head, heat transfer mainly includes three forms: heat conduction, convection, and radiation. Heat conduction is the main form of heat transfer in solids, and the heat flow density is proportional to the negative temperature gradient. Convection occurs in fluids and gases, and the heat flow density is related to the convective heat transfer coefficient and the temperature difference between the welding surface and the environment. Radiation is an important form of heat transfer at high temperatures, and the heat flow density is proportional to the fourth power of the surface temperature of the welded parts. In addition, the heat conduction differential equation is used to describe the heat exchange and temperature change inside the solid, and the boundary conditions of heat conduction include three types: known boundary temperature, known boundary heat flow density, and known boundary heat exchange.
2.2.2 Welding Temperature Field Classification
According to different heat source models and movement states, the welding temperature field can be divided into three types: the temperature field under an instantaneous fixed heat source, the temperature field under a continuously moving concentrated heat source, and the temperature field under a Gaussian distributed heat source. The temperature field formula under an instantaneous fixed heat source is obtained by simplifying the assumptions, and it is of great significance for analyzing the welding process. The temperature field under a continuously moving concentrated heat source is affected by the moving speed of the heat source, and different moving speeds will result in different temperature distributions. The Gaussian distributed heat source model is commonly used in laser welding, and its temperature field formula is more in line with the energy distribution characteristics of laser welding.
2.3 Thermal Elastoplastic Deformation Theory
2.3.1 Basic Principles of Elastoplastic Mechanics
The yield strength criterion is used to judge whether the workpiece is deformed. When the equivalent stress of the metal material reaches a certain value, the material enters the plastic state. The plastic flow theory describes the relationship between stress and strain during plastic deformation, and the loading-unloading criterion is used to determine whether the material is in a loading, unloading, or neutral loading state. The strengthening criterion can be divided into isotropic strengthening and kinematic strengthening, which determine the change rule of the yield surface after plastic deformation.
2.3.2 Elastoplastic Mechanics Analysis
In the welding process, the stress and strain of the material are mainly caused by the change of temperature. By using the elastoplastic mechanics method and the finite element analysis software, the stress and strain changes of the material during welding can be analyzed. In the elastic stage, the stress-strain relationship of the material conforms to Hooke’s law, and in the plastic stage, the plastic strain increment needs to be considered. By establishing the strain-displacement matrix and the balance equation, the relationship between the internal force and displacement of the welded parts can be obtained, which provides a theoretical basis for analyzing the welding deformation.
3. Establishment of Welding Model
3.1 Cutter Head Welding Model
In the finite element welding simulation, the establishment of the welding model is crucial. For the spiral bevel gear cutter head with constant height teeth, considering the influence of the welding groove on the welding deformation, the cutter head model is established by separately modeling the cutter head body and the outer ring. The position of the welding groove and the numbering of the welds are determined, which provides a basis for subsequent numerical simulation. By simulating the changes of the stress and strain of the cutter head caused by the welding temperature field and the filling wire during the welding process, the influence on the final welding deformation can be analyzed, and the optimal welding groove can be obtained through simulation and verified by experiments.
3.2 Welding Heat Source Model
3.2.1 Gaussian Heat Source Model
The Gaussian heat source model assumes that the heat flux density on the welding surface obeys a normal distribution function. It is suitable for thin plate welding and is also commonly used in laser welding simulation analysis. Its heat source model has a relatively small and shallow molten pool. The expressions of the heat source density, maximum heat source density, and heat source effective power are given, which can be used to calculate the temperature field during welding.
3.2.2 Double Ellipsoidal Heat Source Model
The double ellipsoidal heat source model can better reflect the heating effect of the high-energy beam welding heat flow in the depth direction, and it is suitable for simulating deep penetration welding such as electron beam welding and laser welding of medium and thick plates. The heat flow density formulas of the front and rear parts of the ellipsoid are provided, which can accurately describe the heat transfer process during welding.
3.2.3 Uniform Body Heat Source Model
The uniform body heat source model assumes that the heat flux density is uniformly distributed in a certain heating volume, and it is often used in the welding simulation of multi-pass welding. Its expression is related to the welding heat efficiency, voltage, current, and heat source action volume.
3.2.4 Combined Heat Source Model
The combined heat source model combines multiple basic heat source models to take advantage of their respective advantages. In this paper, a combination of a plane Gaussian heat source model and a conical heat source model is selected based on the characteristics of laser wire filling welding. The energy distribution of the laser and the expressions of the heat source models are given, which can improve the simulation accuracy.
3.3 Temperature Field Model of Cutter Head
The spiral bevel gear cutter head with constant height teeth has 34 arc-shaped welds, and each weld is discontinuous and multi-layer welded. In the study of the heat cycle around the welds, some assumptions are made to simplify the calculation. By using the superposition method of multiple temperature fields, the temperature field expressions of each layer of welds are derived. In the first layer of welding, the temperature field expressions of each weld are calculated based on the initial temperature and the influence of the previous weld. In the second layer of welding, considering the cooling time between layers and the influence of the first layer of welding, the initial temperature and the temperature field expressions of each weld are obtained. Similarly, the temperature field of the third layer of welding is analyzed.
3.4 Selection of Welding Groove
For the welding of thick plates such as the cutter head, the selection of the welding groove is very important. There are many types of welding grooves, such as I, V, Y, U, double Y, and double U. Among them, the double Y groove has the advantages of simple groove surface processing, small weld filling amount, and small welding deformation, so it is widely used in thick plate welding. In this paper, the double Y groove is selected for welding, and the groove size is designed according to the actual situation.
4. Numerical Simulation of Welding Process
4.1 Introduction of Simufact.welding Software
Simufact.welding is a professional welding simulation software. It has a Windows operating interface, which is easy to use and can simulate various welding processes. It can simulate the changes of the molten pool during welding, the deformation after welding, and the distribution of residual stress. It can also perform operations such as post-weld heat treatment and pre-weld preheating. The simulation process is similar to the actual welding process, which has strong guiding significance for welding experiments. The software can easily set the welding gun parameters, define multiple welding paths, and set boundary conditions. It also has a built-in multiple welding heat sources and finite element solvers, which can meet the needs of different welding simulations.
4.2 Simplification and Meshing of Cutter Head Model
Due to the complexity of the cutter head model, in order to reduce the requirements for computer performance and focus on the research of the welding area and its surrounding areas, the cutter head model is simplified. Using the hypermesh software, a hexahedral mesh is generated based on the 2D mesh by rotation and stretching. After meshing, the cutter head has 110472 nodes and 96236 elements, and the weld model has 1248 nodes and 816 elements. The minimum element size is 0.5mm×1mm×0.8mm, and the maximum element size is 3mm×3.5mm×3mm.
4.3 Definition of Material Properties and Welding Process
4.3.1 Material Properties of 20CrMo
The welding experiment in this paper uses 20CrMo alloy structural steel. The material has good welding performance and is commonly used in gears, shafts, and other parts. The properties of 20CrMo include thermal conductivity, specific heat capacity, density, elastic modulus, Poisson’s ratio, linear expansion coefficient, and yield strength. These properties change with temperature, especially the specific heat capacity, elastic modulus, and yield strength. In the Simufact software, the material properties can be set by referring to the material library.
Temperature (°C) | 20 | 200 | 500 | 700 | 900 | 1100 | 1300 | 1500 | 1800 |
---|---|---|---|---|---|---|---|---|---|
Specific heat capacity (J/kg•°C) | 461 | 498 | 540 | 896 | 664 | 763 | 775 | 780 | 770 |
4.3.2 Calculation of Welding Preheating Temperature
Preheating before welding is an important measure to reduce welding deformation. The preheating temperature is mainly affected by factors such as the carbon equivalent of the material, the cooling rate of welding, the restraint of the welded parts, the hydrogen content in the welded parts and the surrounding environment, and the heat treatment process after welding. For low alloy steels, the preheating temperature can be calculated by relevant formulas. In this paper, through calculation, the preheating temperature is determined to be 200°C, and the environmental temperature is set in the Simufact.welding software to achieve preheating.
4.3.3 Determination of Welding Process Parameters
In this welding simulation, laser wire filling welding is used. The welding process parameters include welding power, welding speed, efficiency, filler setting, welding gun parameters, and cooling time. The welding heat source is a Gaussian-conical heat source model, and the specific parameters of the heat source are set. The welding path is set by adding constraints to the weld model and selecting a point sequence. In addition, the cooling time between each weld and each layer is set to simulate the actual welding process and stabilize the microstructure of the cutter head.
4.4 Numerical Simulation Analysis
4.4.1 First Layer Welding
In the first layer of welding, a certain welding sequence is followed, and characteristic points are selected in the knife groove to study the deformation, temperature, and stress changes. The simulation results show that after the completion of the four welds in the first layer of the cutter head, the deformation of the knife groove changes suddenly due to the melting of the filler metal and the groove sidewall. After cooling, the total deformation generally decreases with the increase of the depth in the thickness direction, and the larger the bottom groove gap, the greater the deformation. The temperature rises suddenly during welding and then gradually cools to the preheating temperature. The equivalent stress also changes suddenly during welding and then tends to be stable. The equivalent stress on different thicknesses is different, and the maximum equivalent stress can reach 825Mpa on the cutter head plane.
4.4.2 Second Layer Welding
The second layer of welding is carried out on the basis of the first layer, and the characteristic points remain unchanged. The simulation results show that the change trends of temperature and deformation are similar to those of the first layer. The equivalent stress changes differently from the first layer. The closer to the cutter head plane, the faster the equivalent stress stabilizes after a sharp change. For cutter heads with different groove bottom gaps, when the groove bottom gap is 2.5mm, the deformation and equivalent strain changes are the most obvious.
4.4.3 Third Layer Welding
The third layer of welding has a longer cooling time than the previous two layers. The simulation results show that the change trends of temperature and deformation are similar to those of the previous two layers. After a long cooling time, the equivalent stress also tends to be stable. The deformation and temperature changes are related to the distance in the thickness direction. The closer to the cutter head plane, the greater the change of equivalent stress. For cutter heads with different welding groove gaps, the temperature change difference is not large, and the deformation and equivalent stress change the most when the gap is 2.5mm and the least when the gap is 2mm. 综合考虑,the welding groove with a gap of 2mm is selected as the optimal solution for this welding simulation.
5. Welding Experiment
5.1 Influencing Factors of Laser Wire Filling Welding
5.1.1 Laser Power Density
Laser power density is an important factor in laser welding. In wire filling welding, a higher laser power density can make the wire melt faster, but it also requires higher cost for the laser device.
5.1.2 Welding Speed
The welding speed affects the melting efficiency of the wire and the volume shape of the welding pool. If the welding speed is too low or too high, it may lead to welding failure, so it is necessary to determine a reasonable welding speed.
5.1.3 Type of Shielding Gas
Argon, helium, nitrogen, etc. are commonly used as shielding gases in laser welding.Argon is widely used in industrial welding because of its low activity, low cost, and good protection effect. It can prevent the welding area from being oxidized and reduce the negative effect of the plasma cloud generated during high-power welding.
5.1.4 Laser Spot Diameter and Defocus Amount
The diameter of the laser spot should be controlled within a certain range. If it is too large, it will cause unnecessary ablation around the weld and lead to weld depression. The defocus amount also affects the power density on the workpiece. When the defocus amount is 0, the power density is too large, which may damage the welding quality.
5.1.5 Laser Absorption Rate
The absorption rate of different materials for laser energy is different, which is related to factors such as the chemical composition, microstructure, laser wavelength, power density, surface smoothness, welding groove form, and preheating temperature of the material.
5.1.6 Wire Feeding Speed
The wire feeding speed directly affects the amount of laser energy absorbed by the wire. With the increase of the wire feeding speed, the laser energy absorbed by the unit length of the wire decreases, resulting in a decrease in the melting state of the wire.
5.2 Welding Performance of Base Metal
The base metal used for the cutter head welding in this paper is 20CrMo. After quenching and tempering treatment, it has high strength, good toughness, and strong impact resistance. During welding, due to the high temperature and rapid cooling in the welding area, a lath martensite structure with good strength and hardness is formed. However, the rapid transformation of the martensite structure will cause an increase in internal stress, which has an adverse effect on the welding seam. Therefore, appropriate post-welding heat treatment measures need to be taken to eliminate or reduce this influence.
5.3 Welding Experiment of Cutter Head
5.3.1 Pre-welding Preparation
Before welding the cutter head, it is necessary to process the welding groove and assemble the cutter head. The assembly method is an interference fit. The outer ring of the cutter head needs to be heated in oil to expand and then assembled with the cutter head body. After assembly, the surface of the cutter head needs to be cleaned to remove oil, dust, and other contaminants. Manual cleaning, electrolytic cleaning, and ultrasonic cleaning can be used. In this experiment, manual cleaning with acetone solution is mainly used. After cleaning, the cutter head needs to be isolated from the outside environment to prevent secondary pollution.
5.3.2 Pre-welding Preheating
According to the preheating formula calculated before, the preheating temperature of the cutter head is set to 200°C. Before welding, the cutter head is heated to this temperature and then taken out for welding. Preheating can reduce the probability of forming hardened martensite after welding, increase the hydrogen escape rate in the metal, and reduce the possibility of cracks and large pores in the welding seam.
5.3.3 Welding Process
In this experiment, a diffusion-cooled radio frequency excited CO₂ laser processing system is used for cutter head welding. Ar-CO₂ binary mixed gas is selected as the shielding gas to improve the welding stability and the quality of the welding seam. During welding, a block is inserted into the cutter head groove to prevent excessive deformation of the cutter head. The welding process parameters are the same as those in the simulation, including welding power, welding speed, defocus amount, and wire feeding speed. After welding, the cutter head needs to be heat treated to reduce the residual stress.
5.4 Detection of Welding Results
5.4.1 Detection of Cutter Head Deformation
After heat treatment of the cutter head, the deformation of the cutter head groove is detected by using an electronic plug gauge. When the groove size is within the range of 10.18 – 0.008 – 0.003, it meets the installation requirements of the cutter bar. The measured groove sizes after welding with different groove bottom gaps are shown in the following table:
Groove Number | Groove Bottom Gap 2mm | Groove Bottom Gap 2.5mm | Groove Bottom Gap 3mm |
---|---|---|---|
1 | 10.1735 | 10.1752 | 10.1742 |
2 | 10.1741 | 10.1740 | 10.1736 |
3 | 10.1758 | 10.1759 | 10.1755 |
… | … | … | … |
The curve graph shows that when the groove bottom gap is 2mm, the deformation fluctuation of the cutter head groove is small and the accuracy meets the requirements. When the gap is 2.5mm, the deformation fluctuation is large and some groove deformations exceed the accuracy range. Therefore, the welding groove with a gap of 2mm is more suitable.
5.4.2 Installation Detection of Cutter Bar
After detecting the groove size and stress of the cutter head, the cutter bar is installed. First, visually observe the deformation of the groove to judge whether there are obvious welding defects and large deformations. Then, install the reference group on the tool setting table and adjust the height. During the installation process, pay attention to the total runout less than 2µm. After installation, the cutter bar may need to be adjusted. The installation results show that all the cutter bars pass through the grooves, meeting the requirements.
5.4.3 Stress Detection of Cutter Head Groove
After welding the cutter head, the stress of the groove is detected by tightening the bolts to make the welding seam bear the load for 48 hours. If there is no cracking sign after this time, it indicates that the welding seam quality is good and the cutter head groove after welding meets the use requirements.
6. Conclusion and Outlook
6.1 Research Results
In this paper, through the research on the welding process of the spiral bevel gear cutter head with constant height teeth, the following results are obtained:
- Based on the research of multi-layer welding at home and abroad, the laser wire filling welding method is determined. The welding mathematical model is established, the welding groove is optimized, and the welding parameters are set. The cutter head model is built according to the existing data, and the thermal physical properties of the welding base metal are analyzed. The temperature change of each layer in multi-layer welding is analyzed by using the temperature field theory, laying a foundation for the research of stress and deformation.
- The welding simulation of the cutter head is carried out. According to the actual situation, the Gaussian – conical composite heat source model is adopted. Based on the elastoplastic thermal deformation theory, the Simufact.welding software is used to obtain the cloud diagrams and curves of temperature, stress, and deformation changes during the welding process of the cutter head. The analysis of the data shows that when the groove bottom gap is 2mm, the welding state is the best.
- The welding experiment of the cutter head is carried out by using laser wire filling welding. The actual welding performance of the base metal is analyzed, and the pre-welding treatment of the cutter head is carried out. After welding and heat treatment, the deformation of the cutter head groove is detected to verify the reliability of the welding simulation and that the selected welding groove can effectively reduce the groove deformation. The installation and inspection of the cutter bar are carried out to verify the feasibility of the actual operation of the cutter head.
6.2 Research Deficiencies and Outlook
Due to the limitations of research time and conditions, there are still some deficiencies in this paper. For example, the situation of multi-layer and multi-pass welding when the welding groove is large has not been considered, and the welding of the cutter head under different materials and welding methods needs to be further studied. In the future research, it is necessary to expand the research scope, explore more welding methods and process parameters, and improve the welding quality of the spiral bevel gear cutter head with constant height teeth. At the same time, it is also necessary to strengthen the research on the relationship between welding deformation and the performance of the cutter head to provide more theoretical support for the manufacturing of high-quality cutter heads.
In conclusion, this research has important theoretical and practical significance for improving the welding quality of the spiral bevel gear cutter head with constant height teeth and promoting the development of the gear manufacturing industry. It is expected that future research can make further progress in this field.
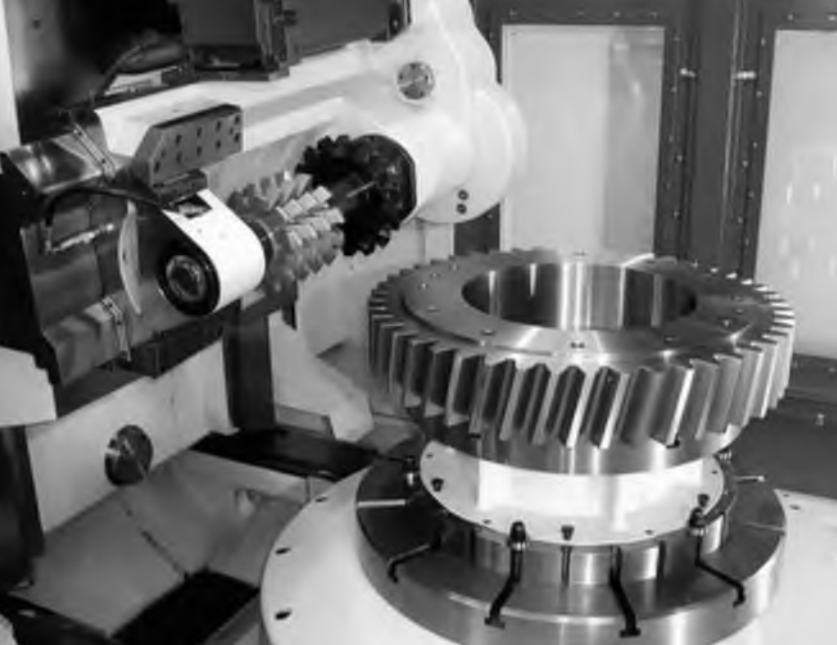