Abstract:
This article presents a comprehensive approach to verify the design rationality of an external meshing angular modified cylindrical helical gear pair utilized in the final stage of a wire rope hoist reducer. By leveraging the parametric modeling capabilities of Creo Parametric and finite element analysis (FEA) functionalities of Creo Simulate, this study aims to simplify the complex calculations and manual verifications involved in gear design and strength assessments. The precision parametric 3D modeling of the involute tooth profile of the helical gear pair, combined with static simulation analysis, provides detailed stress distributions across various tooth regions. This method significantly reduces manual calculations and the need to consult manuals for formulas, parameters, and coefficients, thereby enhancing the efficiency of gear design and evaluation processes.
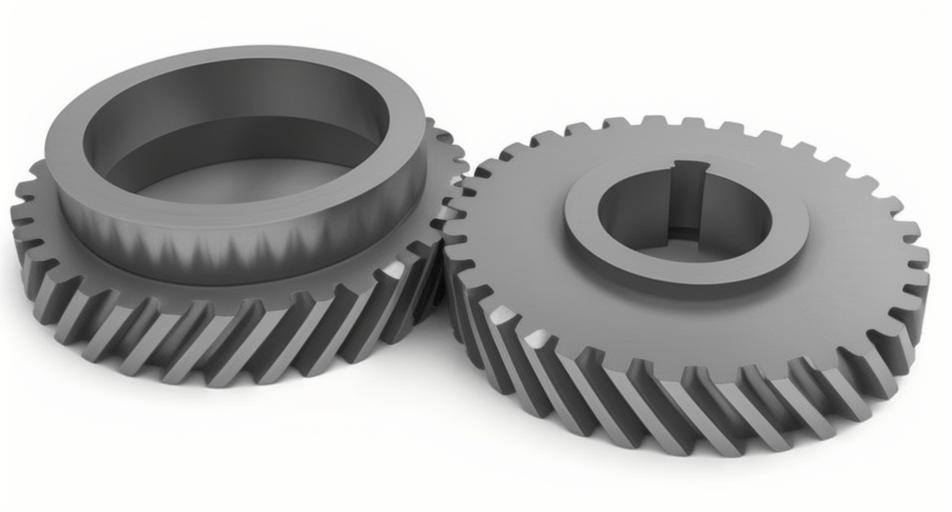
Keywords: modified gear, helical gear, parameterization, finite element analysis, Creo Simulate
1. Introduction
Helical gear is widely employed in various industrial applications due to their superior meshing performance, high load-bearing capacity, and smooth transmission. In heavy-duty applications such as crane hoists, angularly modified helical gear is often utilized to further enhance their load-bearing capabilities and transmission stability. However, calculating and verifying the strength of these gears can be intricate, primarily due to the complexity of their tooth shapes and the intricate load distribution among mating gear pairs.
Traditionally, gear strength calculations are based on standards like GB/T 3480 and GB/T 10063, which often involve numerous formulas and assumptions, leading to complex manual computations and significant reliance on engineering experience. This approach not only consumes considerable time but also introduces inaccuracies and inconsistencies across different evaluations.
With the widespread adoption of computer-aided design (CAD) and computer-aided engineering (CAE) tools, finite element analysis (FEA) has emerged as a potent means to streamline gear strength evaluations. By creating precise finite element models and performing stress simulations, engineers can now obtain reliable strength assessments without resorting to complex manual calculations.
This article explores the use of Creo Parametric and Creo Simulate to model and analyze an angularly modified helical gear pair designed for the final stage of a wire rope hoist reducer. The study encompasses parametric 3D modeling, finite element modeling, and stress analysis, ultimately verifying the design’s rationality and highlighting the benefits of this approach.
2. Design Input and Gear Parameters
2.1 Design Overview
The study focuses on an angularly modified helical gear pair employed in the final stage of a wire rope hoist reducer. The reducer’s overall design and gear ratio allocation necessitate the use of high-capacity gears to withstand the substantial loads generated during hoisting operations.
2.2 Gear Geometric Parameters
Based on the design requirements, the following parameters are selected for the helical gear pair:
- Lifting Force (F_G): 25 kN
- Drum Pitch Diameter (D): 274 mm
- Lifting Speed (v): 24 m/min
- Final Gear Ratio (i): Approximately 4.7
The initial gear tooth counts are set to z1 = 15 for the pinion and z2 = 71 for the gear, resulting in an actual gear ratio of i = 4.733. The helix angle (β) is initialized at 15°, and 20CrMnTiH steel, heat-treated through carburizing, quenching, and low-temperature tempering, is chosen as the material.
Utilizing standard gear design formulas, the center distance (a), normal module (mn), and other geometric parameters are calculated. After considering the desired load-bearing capacity and overall performance, a total modification coefficient (xΣ) of 0.6869 is selected, with individual modification coefficients of x1 = 0.5 for the pinion and x2 = 0.1869 for the gear. The final geometric parameters are summarized in Table 1.
Table 1: Geometric Parameters of the Angularly Modified Helical Gear Pair
Parameter | Pinion (Gear 1) | Gear (Gear 2) |
---|---|---|
Number of Teeth (z) | 15 | 71 |
Normal Module (mn, mm) | 3.5 | 3.5 |
Normal Pressure Angle (αn, °) | 20 | 20 |
Helix Angle (β, °) | 15 | 15 |
Total Addendum Modification (xΣ) | 0.6869 | – |
Addendum Modification (x1, x2) | 0.5, 0.1869 | – |
Center Distance (a’, mm) | 158.1 | – |
Dedendum Height Coefficient (ha*) | 1.0 | 1.0 |
Top Clearance Coefficient (c*) | 0.25 | 0.25 |
Face Width (B, mm) | 55 | 55 |
Pitch Diameter (dp, mm) | 54.35 | 257.27 |
Base Circle Diameter (db, mm) | 50.86 | 240.74 |
Addendum Circle Diameter (da, mm) | 64.63 | 265.35 |
Dedendum Circle Diameter (df, mm) | 49.10 | 249.82 |
3. Parametric 3D Modeling in Creo Parametric
To create an accurate finite element model, a precise parametric 3D representation of the helical gear teeth is essential. This section outlines the process of generating the 3D models using Creo Parametric.
3.1 Establishing Parametric Curves
The first step involves defining the parametric curves that form the basis of the gear tooth profiles. These curves include the involute profile and helix line, which are generated using mathematical expressions within Creo Parametric.
- Involute Curve: The involute curve is described using the base circle diameter (db) and the involute equation:
x=rb(cosθ+θsinθ)
y=rb(sinθ−θcosθ)
where θ is the angle measured from the base circle center.
- Helix Line: The helix line along the tooth flank is described by its polar coordinates, considering the helix angle (β) and face width (B):
r=rbsecβ
θ=rbttanβ
z=t
where t represents the parameter along the helix.
Figure 2: Parametric Curves for Involute Profile and Helix Line
Note: This is a placeholder image; actual curves should be included as per the study’s specific details.
3.2 Creating the 3D Gear Models
Utilizing the parametric curves, the 3D gear models are constructed within Creo Parametric. This involves extruding the involute and helix curves to form the tooth profiles and sweeping them along the gear axis to create the complete tooth geometry.
After constructing the individual gear models, they are virtually assembled and meshed to ensure proper alignment and contact.
4. Static Simulation Analysis in Creo Simulate
Having established the precise 3D models, the next step involves conducting a static simulation analysis using Creo Simulate to assess the stress distribution within the gear teeth.
4.1 Defining Material Properties and Loading Conditions
The material properties for 20CrMnTiH steel, including yield strength, ultimate tensile strength, density, Poisson’s ratio, and elastic modulus, are defined within Creo Simulate. The gears are loaded according to the operating conditions, with the torque (T1 = 723.6 N·m) applied to the pinion gear.
Figure 4: Loading and Constraint Conditions in Creo Simulate
4.2 Meshing and Simulation Setup
A suitable mesh is generated for the gear models, with a finer mesh applied to critical regions such as the tooth roots and flanks. The mesh is optimized to balance computational efficiency and accuracy.
4.3 Stress Analysis Results
The static simulation analysis produces detailed stress distributions across the gear teeth. The primary outcomes include:
- Von Mises Stress Distribution: Highlights regions of high stress concentration, particularly at the tooth roots and tips.
- Contact Stress Distribution: Reveals the contact stresses at the mating tooth surfaces, essential for assessing the potential for tooth surface failure.
The analysis results demonstrate that the maximum stress values are within acceptable limits, as dictated by the material’s yield strength and contact stress limits.
5. Conclusion and Discussion
Through the combined use of Creo Parametric for parametric 3D modeling and Creo Simulate for static simulation analysis, this study effectively verifies the design rationality of an angularly modified helical gear pair employed in a wire rope hoist reducer. The key findings include:
- Efficient Design Verification: The approach significantly reduces the reliance on manual calculations and eliminates the need to consult multiple standards and handbooks, thereby streamlining the design verification process.
- Detailed Stress Analysis: The simulation analysis provides a comprehensive understanding of stress distributions across various tooth regions, facilitating the identification of potential failure modes and their mitigation strategies.
- Enhanced Design Flexibility: The parametric modeling capabilities enable rapid design iterations by modifying gear parameters and quickly re-evaluating the stress distributions, thereby enhancing the overall design efficiency.
- Validation of Design Choices: The analysis validates the selected gear parameters and material properties, ensuring that the design meets the operational requirements and safety standards.
Future studies could explore the dynamic behavior of the gear pair under varying operating conditions and load spectra, utilizing advanced simulation techniques such as transient dynamics or fatigue analysis. Additionally, the impact of different material choices and heat treatment processes on gear performance could be investigated to further optimize the design.
References:
- Design and Analysis of Machine Elements, S. Timoshenko and J.N. Goodier, Wiley, 1969.
- Finite Element Analysis, O.C. Zienkiewicz and R.L. Taylor, McGraw-Hill, 2005.
- GB/T 3480 – Calculation of Load Capacity of Spur and Helical Gear, Standards Press of China, various years.
- Gear Design and Application Handbook, Paul R. Lewicki, McGraw-Hill, 2011.