The active design technology of gear tooth surface designs the shape of gear tooth surface according to the functional requirements of gear transmission. First, the meshing performance of mating gear tooth surface is preset, that is, the transmission error curve and the best contact mark, and then the gear tooth surface and its processing method that can accurately meet the above preset conditions are designed to achieve the purpose of active design.
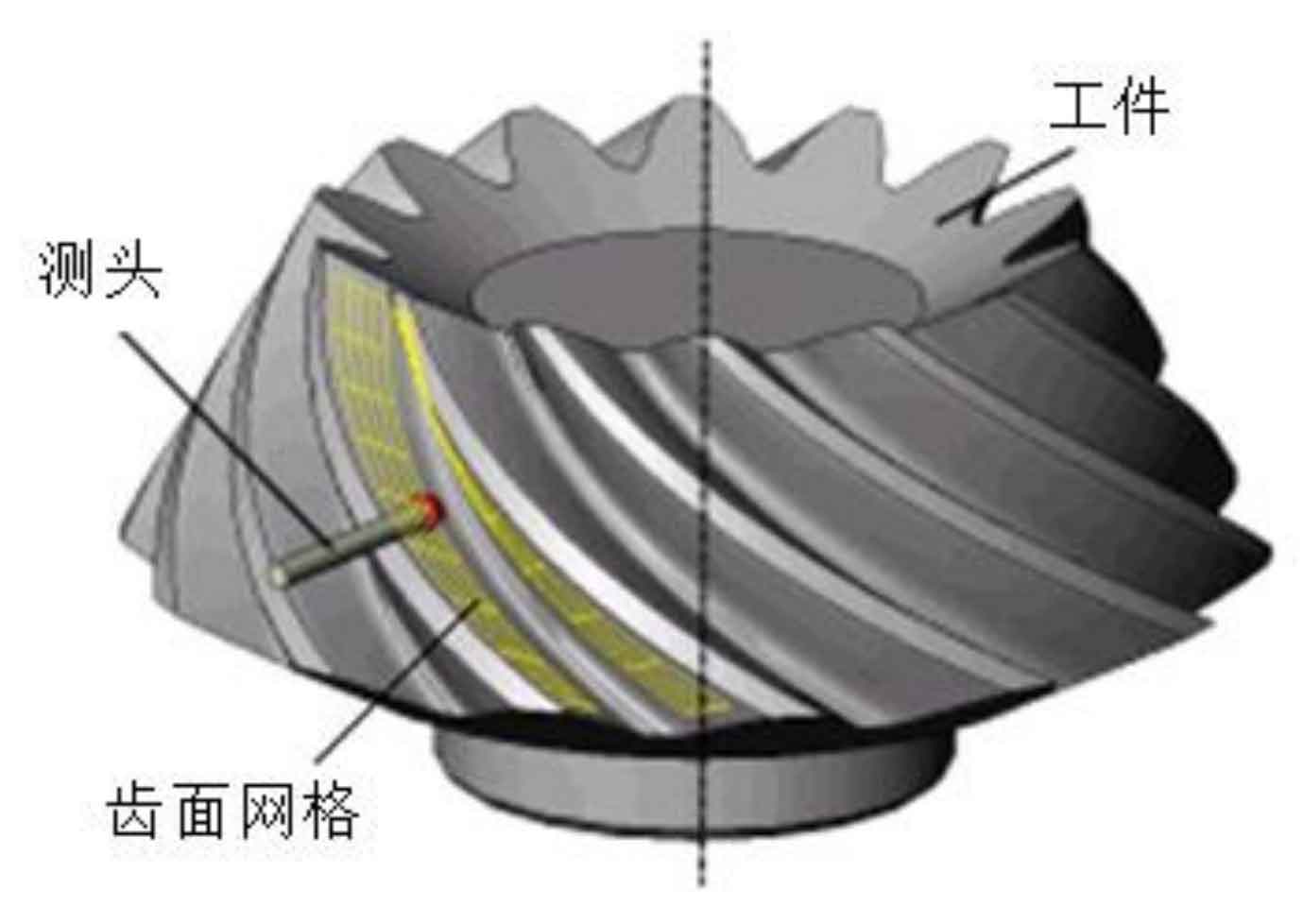
The local synthesis method proposed by Litvin can pre control the meshing performance near the reference point, but the meshing performance of the gear tooth surface far away from the reference point cannot be accurately controlled, which may lead to serious bending of the contact trace and distortion of the contact area of the gear tooth surface. Therefore, Fang Zongde and Cao Xuemei put forward the active design method of spiral bevel gear tooth surface. According to the requirements of the position, direction and transmission error amplitude of the impression on the gear tooth surface, a meshing point is designed at the small end, the middle end and the big end of the gear tooth surface respectively. Through the control of these three meshing points, the whole meshing quality of the gear tooth surface is controlled, and it is verified by the roll inspection test; On this basis, in order to meet different processing requirements, Fang Zongde and Cao Xuemei proposed to redesign the gear tooth surface according to the given vertical gear position. This design ensures that the amplitude of transmission error remains unchanged, while the contact trace changes only slightly, which provides a new method and way for the design of spiral bevel gear pairs, and is of great significance for the design of high-speed and heavy-duty gears and gears with special requirements. Wu Xuncheng et al. Proposed an active design method of point meshing tooth surface, and gave a detailed calculation process. This method designs the first-order and second-order parameters of the gear tooth surface by giving the equation of transmission error and contact trace, and directly designs the contact trace of the mating gear tooth surface, the size of the long axis of the contact ellipse and the high-order acceleration, so that the designer can design the gear tooth surface according to the required gear transmission performance. On the basis of flexible multi-body kinematics, Wang Sanmin decomposes the elastic deformation of meshing point into support deformation, wheel body deformation and contact deformation, and puts forward an active design method that can ensure the expected load contact performance of spiral bevel gear in the initial design stage, which is applied to the tooth surface design of spiral bevel gear in the central transmission of an aeroengine. Liu Guanglei used numerical control gear grinding to process spiral bevel gears. With the help of local synthesis method, the grinding parameters with specified meshing performance at the reference point of the gear tooth surface were obtained. By optimizing the variable coefficient of each order of the small wheel, the relative motion relationship between the small wheel and the shaking table was changed to ensure that the contact mark and transmission error curve of the gear tooth surface met the design requirements. With this method, the active optimization design of the tooth surface of an aviation spiral bevel gear was carried out. Peng Xianlong proposed a method of topological modification design for the tooth surface of face gear and pinion with given meshing performance. The topological modification tooth surface of the face gear is determined by using the rotation angle relationship between the face gear and the gear shaper, and then the topological modification tooth surface of the pinion is constructed by using the position and direction of the contact path and the size of the contact ellipse, and the linear equation between the topological modification tooth surface of the pinion and the machining parameters is established. Aiming at Gleason spiral bevel gear, Zhou kaihong proposed a theory and method of designing point meshing tooth surface according to the predetermined meshing characteristics. This method is the development and improvement of Gleason tooth surface design method under the condition of numerical control technology. Tang Jinyuan and Du Jin considered the influence of the position of the initial calculation point on the sensitivity of installation error, and improved the active design method of spiral bevel gear with preset transmission error curve. Through the calculation and comparison of the installation error sensitivity coefficient, the reasonable initial calculation point position is determined, and a set of small wheel processing adjustment parameters that meet the preset transmission error curve and have good tolerance are obtained by the local synthesis method.
All of the above are aimed at Gleason single-sided machining, while there are few reports on the active design of cycloid hypoid gear tooth surface machined by double-sided method. Su Jinzhan and ship put forward the tooth surface optimization design method of spiral bevel gear and hypoid gear based on ease off and sensitivity matrix, but there is no discussion on how to ensure the Meshing Effect of the tooth surface of both sides of the gear at the same time and how to selectively ensure the tooth surface of one side of the gear according to the actual working conditions.