The transmission device of locomotive bogie is mostly a first-level spur gear reduction structure and the actual operating speed varies widely. Therefore, not only the actual overlap, the load distribution between teeth and the excitation force should be considered when designing the gear tooth trimming amount, but also the application requirements of different working conditions such as starting, continuous and high speed should be considered. Among many kinds of inspection indexes, the actual coincidence degree, as the average value describing the number of teeth simultaneously engaged, is of great significance for measuring the smoothness and load carrying capacity of spur gear transmission. Because of the special working environment of locomotive traction spur gear, the design of the trimming amount is usually based on the tooth deformation amount under the starting or continuous working conditions. When entering the high-speed operation, the output torque of the traction motor decreases. At this time, the reduction of the deformation amount leads to the shortening of the length of the meshing line, which greatly reduces the actual coincidence. Therefore, it is necessary to check the actual coincidence during the trimming design to avoid the phenomenon of meshing discontinuity.
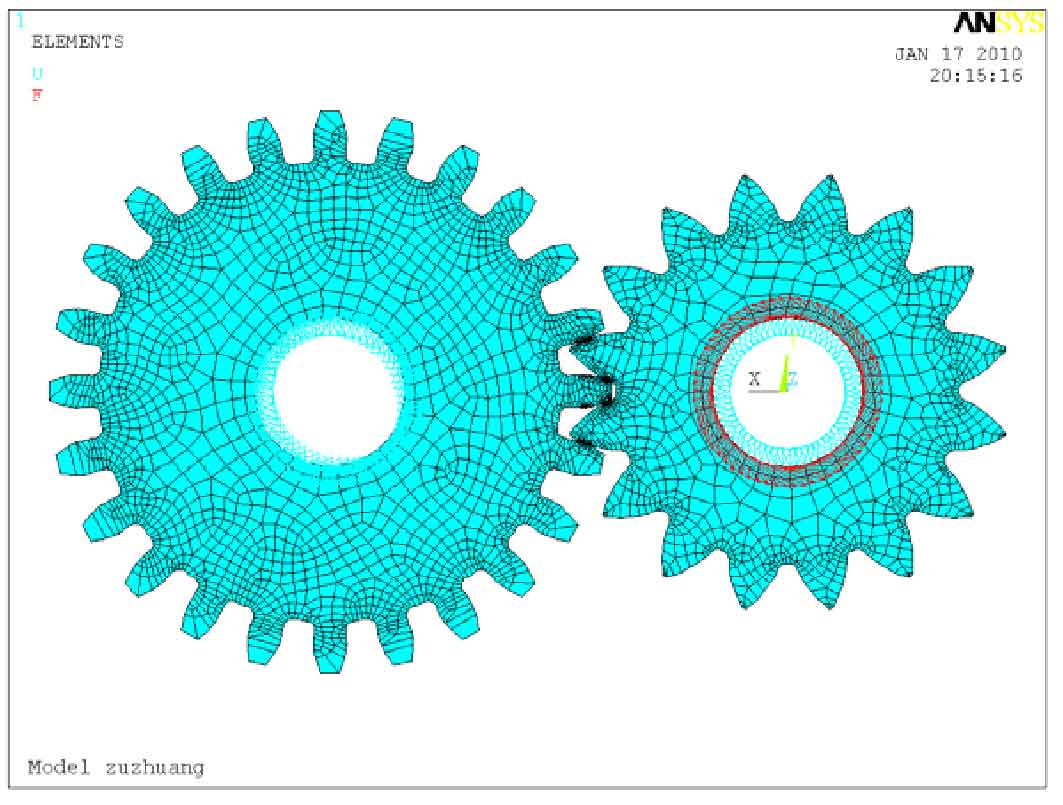
At present, the mainstream classical G. Niemann formula does not take the selection of gear tooth trimming amount into account when solving the actual coincidence degree, resulting in the accuracy of the solution model can not meet the actual use requirements. By analyzing the basic mechanism of spur gear trimming, based on the change law of the normal load direction of the gear teeth and the length of the actual meshing line before and after trimming, a calculation method of the actual coincidence after trimming is proposed, which improves the shortcomings of the classical coincidence calculation formula, and has certain practical value for improving the quality of trimming.
Based on the analysis of the basic mechanism of spur gear trimming, the calculation method of the actual coincidence degree after trimming is put forward on the basis of the variation of the normal load direction of the gear teeth and the length of the actual meshing line before and after trimming. The results show that the actual coincidence degree of locomotive traction spur gear under continuous working condition is improved after trimming, and the actual coincidence degree is less than the theoretical coincidence degree due to the reduction of meshing shape variable under high-speed working condition. Compared with G. Niemann formula, this calculation method improves the calculation accuracy of the coincidence degree and makes up for the shortcomings of the classical method. It is applicable to the calculation and analysis of the coincidence degree under different working conditions of the locomotive, and has certain practical value.