When it comes to heat treatment for spur gears, helical gears, and bevel gears, there are several key considerations to keep in mind. Heat treatment is a crucial process that enhances the mechanical properties of gears, improving their strength, hardness, and wear resistance. Here are some important factors to consider:
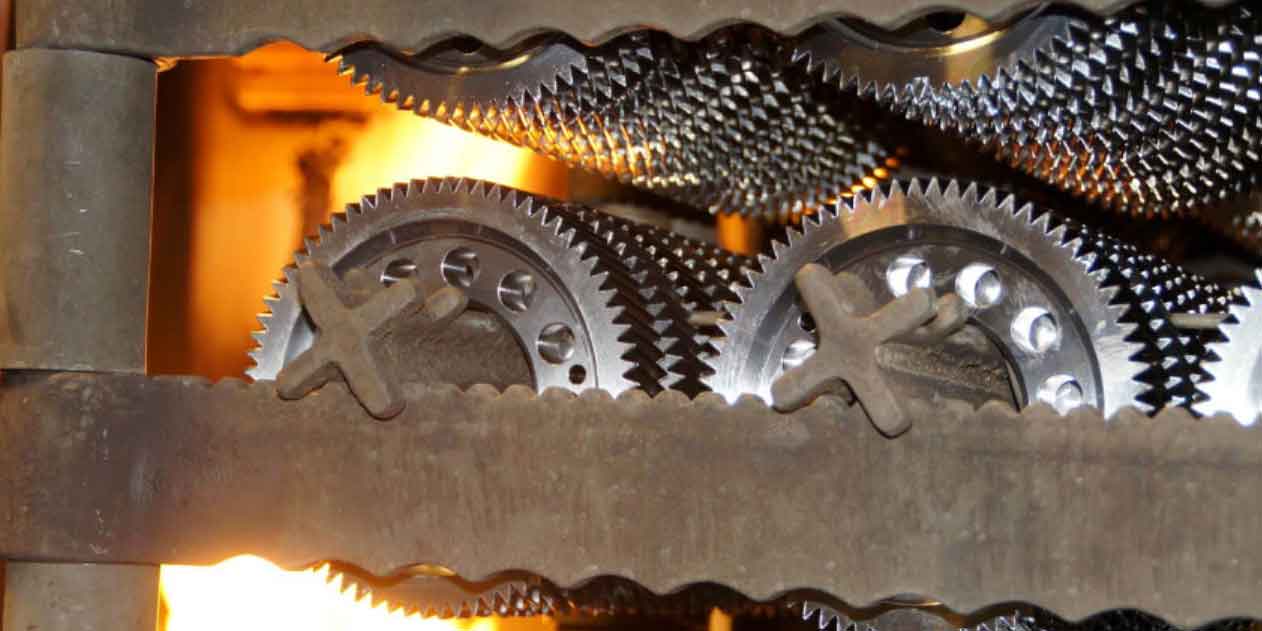
- Material Selection: The choice of material for gears is critical for heat treatment. Common materials include alloy steels such as 8620, 4140, or 4340, which offer good hardenability and strength. The material should have the ability to achieve the desired hardness after heat treatment.
- Heat Treatment Method: The most common heat treatment method for gears is quenching and tempering. This process involves heating the gears to a specific temperature, typically above the transformation range, and then rapidly cooling them (quenching) in a suitable medium like oil or water. After quenching, tempering is performed to relieve internal stresses and improve toughness.
- Case Depth: The case depth refers to the hardened layer thickness on the gear surface. It is crucial to achieve the right balance between a deep enough case to provide wear resistance and a soft enough core to maintain toughness. The case depth is typically specified in the gear design and should be carefully controlled during heat treatment.
- Surface Finish: Gears require a smooth and uniform surface finish for efficient operation and reduced wear. During heat treatment, it is important to minimize distortion or warping that could affect the final surface finish. Proper fixturing and heat treatment techniques can help maintain the required surface finish.
- Distortion Control: Heat treatment can induce distortion in gears due to non-uniform heating or cooling rates. Distortion can affect the gear’s dimensional accuracy and performance. Employing appropriate quenching techniques, such as using controlled cooling rates or specialized fixtures, can help minimize distortion and maintain gear integrity.
- Quality Control: Ensuring consistent quality during heat treatment is essential. It involves monitoring and controlling parameters such as temperature, time, quenchant composition, and cooling rates. Regular inspections, hardness testing, and metallurgical analysis should be conducted to verify that the gears meet the specified requirements.
- Post-Heat Treatment Operations: After heat treatment, gears may require additional processes like grinding, shot peening, or superfinishing to achieve the desired surface finish, dimensional accuracy, and residual stress distribution. These operations should be carefully planned and executed to avoid any detrimental effects on the heat-treated gears.
It is important to note that the specific heat treatment process and parameters may vary depending on the gear application, design requirements, and the material being used. Consulting with heat treatment experts or referring to industry standards and specifications for gear manufacturing can provide more detailed guidelines and recommendations.