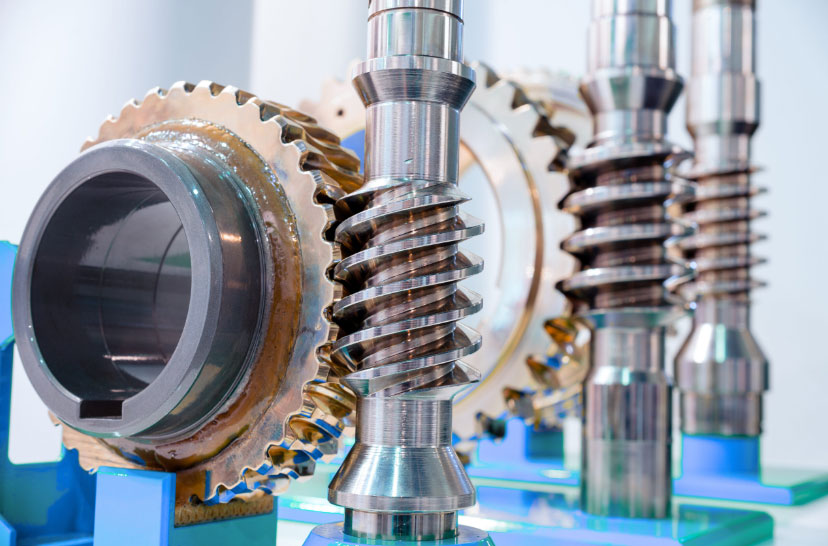
Wear detection in worm gear, especially in heavy machinery, is critical for maintaining optimal performance and preventing unexpected failures. Advanced methods for wear detection can be broadly categorized into direct and indirect techniques. Here’s a comprehensive overview:
Direct Methods
- Visual Inspection:
- Regular visual checks can help identify wear and tear, though it is labor-intensive and subjective.
- Advanced visual methods include using high-resolution cameras and image processing software to detect wear patterns.
- Surface Profilometry:
- This technique measures the surface roughness and wear by scanning worm gear surface with a stylus or optical sensor.
- 3D laser scanners provide detailed surface topography to identify wear.
- Microscopy:
- Scanning Electron Microscopy (SEM) and Atomic Force Microscopy (AFM) can provide high-resolution images of the wear surfaces.
- Useful for identifying micro-scale wear and understanding wear mechanisms.
Indirect Methods
- Vibration Analysis:
- Vibration sensors detect changes in the vibration patterns of the machinery, which can indicate wear or faults in worm gear.
- Signal processing techniques like Fast Fourier Transform (FFT) help analyze the frequency components related to wear.
- Acoustic Emission:
- Acoustic sensors detect high-frequency sound waves produced by the friction and impacts within worm gear system.
- Advanced signal processing is used to differentiate between normal operation and wear-related emissions.
- Oil Analysis:
- Analyzing the lubricant oil for metal particles and contaminants can indicate wear.
- Techniques include ferrography, spectrometry, and particle counting.
- Thermography:
- Infrared cameras detect temperature variations on worm gear surface.
- Increased temperature can be an indicator of increased friction due to wear.
- Electromagnetic Methods:
- Eddy current testing and magnetic flux leakage are used to detect changes in worm gear material properties due to wear.
Advanced Sensor Integration
- Smart Sensors:
- Embedded sensors within worm gear system provide real-time monitoring.
- Internet of Things (IoT) integration allows continuous data collection and analysis for predictive maintenance.
- Machine Learning and AI:
- Algorithms analyze data from various sensors to predict wear and schedule maintenance.
- AI models improve over time with more data, enhancing prediction accuracy.
Research and Development
- Non-Destructive Testing (NDT):
- Techniques like X-ray tomography and ultrasonic testing provide internal wear assessment without disassembling the machinery.
- Advanced Coatings:
- Research into wear-resistant coatings can prolong worm gear life and reduce wear rates.
- Material Science Innovations:
- Development of new materials with superior wear resistance for worm gear.
Practical Applications
- Condition Monitoring Systems:
- Integrated systems combining multiple detection methods provide comprehensive wear monitoring.
- Used in industries like mining, construction, and manufacturing where heavy machinery operates under extreme conditions.
These advanced wear detection methods help in timely identification and management of wear in worm gear, ensuring efficient operation and reducing the risk of unexpected failures. Continuous research and technological advancements in this field are enhancing the reliability and longevity of heavy machinery.