Introduction
In mechanical engineering, gears play a vital role in power transmission. The precision and performance of gears directly impact the overall efficiency and reliability of machines. However, gears are prone to misalignment during meshing due to various factors such as thermal deformation, contact loading, and manufacturing inaccuracies. This misalignment, also known as meshing dislocation, significantly affects the contact stress, meshing stiffness, transmission efficiency, and potential damage to gears. Therefore, it is crucial to investigate and mitigate meshing dislocation to enhance gear performance.
This paper presents a comprehensive study on the modification of helical cylindrical gears to compensate for meshing dislocation under different error conditions. The analysis considers both systematic and random errors that contribute to meshing dislocation and explores various gear modification strategies to improve the gear’s tooth surface bearing capacity and load distribution.
Background and Literature Review
Gear meshing dislocation has been a topic of interest for researchers due to its significant impact on gear performance. Kumar et al. [1] studied the effect of gear misalignment on the contact area through both theoretical and experimental approaches, highlighting the importance of accurate alignment for optimal gear performance. Wang et al. [2] focused on the analysis of gear misalignment in electric vehicle reducers, emphasizing the need for microscopic modifications to reduce misalignment deviations. Yuan et al. [3] developed models to demonstrate that tooth profile and lead modifications could effectively reduce the transmission error (STE) fluctuations in gears with misalignment, enhancing vibration reduction. Luo [4] furthered this research by analyzing the stiffness and static errors of gears and investigating multi-objective modifications for optimal gear performance.
Objective
The objective of this study is to enhance the tooth surface bearing capacity of involute helical cylindrical gears under actual working conditions by analyzing and optimizing gears with meshing dislocation caused by various errors. By considering the system stiffness and introducing random factors such as precision and tolerance, this study aims to accurately analyze the sources and contributions of meshing dislocation. Based on these findings, microscopic gear modifications are proposed and validated through comparative analyses.
Methodology
1. Analytical Model and Cases
The analytical model consists of a gear pair, two pairs of tapered roller bearings, and two parallel shafts, as illustrated in Figure 1. The gear pair transmits power from the left end of Shaft 1 to the output at the right end of Shaft 2, with a maximum input torque of 450 N·m and a maximum speed of 7,500 r/min. Table 1 summarizes the geometric parameters of the gear pair used in this study.
Parameter | Value |
---|---|
Number of Teeth | Active: 25, Passive: 31 |
Face Width (mm) | 48 |
Rotation | Active: Right, Passive: Left |
Normal Module (mm) | 2.954 |
Normal Pressure Angle (°) | 23.45 |
Helix Angle (°) | 21.5 |
Standard Center Distance (mm) | 88.9 |
Four analytical cases are considered to study the effects of meshing dislocation and modifications:
- Case 1: Systematic dislocation without random dislocation or modification.
- Case 2: Systematic dislocation with modification to compensate for systematic dislocation (no random dislocation).
- Case 3: Both systematic and random dislocations without modification.
- Case 4: Both systematic and random dislocations with modifications to compensate for both.
2. Meshing Dislocation Analysis
According to ISO 6336 [5], meshing dislocation (Fβx) is defined as the maximum separation between corresponding points on the meshing teeth along the tooth width. Hourser et al. [6] categorized meshing dislocation into three types: parallel misalignment (center distance error), misalignment parallel to the meshing plane (MLOA), and misalignment perpendicular to the meshing plane (MOLOA). For this study, MLOA is the primary concern due to its significant impact on stress concentration and load distribution.
Conclusion
The primary objective of this study was to compensate for the effects of gear misalignment through targeted calculations and modifications of gear pairs experiencing different degrees of misalignment. The results demonstrate that:
- Dominant Factors Affecting Misalignment: Among the systematic factors, bearing deformation had the most significant influence on the misalignment, with individual effects sometimes overlapping and sometimes cancelling each other out. Among random factors, spiral line deviations contributed most to the gear mesh misalignment, with their effects also additive.
- Key Role of Systematic Misalignment: Systematic misalignment emerged as the primary factor affecting the smoothness and load-bearing capacity of gear transmission.
- Effectiveness of Modification Methods: A combination of tooth profile modification and diagonal modification proved effective in compensating for the effects of systematic misalignment. However, these modifications had negligible impact on compensating for random misalignments.
This research underscores the importance of understanding the sources and contributions of different types of misalignment in gear systems. By precisely quantifying and addressing systematic and random factors, designers can develop optimized gear profiles that improve load distribution, reduce stress concentrations, and ultimately enhance the performance and lifespan of gear transmission systems.
Future Work
While this study provides valuable insights into the effects of misalignment and the effectiveness of various modification techniques, there are still opportunities for further research:
- Dynamic Analysis: Conducting dynamic simulations under varying load and speed conditions can provide a more comprehensive understanding of the impact of misalignment on gear performance over time.
- Material Properties: Investigating the influence of material properties, such as elastic modulus and Poisson’s ratio, on the response of gears to misalignment could lead to the development of more robust designs.
- Advanced Modification Techniques: Exploring more advanced modification strategies, such as variable-depth modifications along the tooth profile, may offer even better compensation for misalignment effects.
References
The detailed list of references consulted for this study is included at the end of the original document and is essential for verifying the claims and findings presented herein.
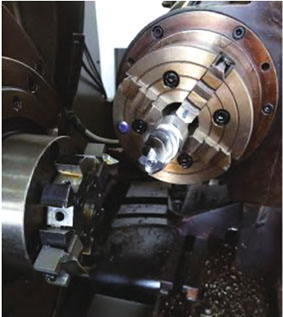