Advancements in material science have significantly enhanced the durability and performance of helical gear. These improvements are crucial in demanding applications where helical gear is subjected to high loads, speeds, and harsh environmental conditions. Let’s explore some of the key advancements in this field:
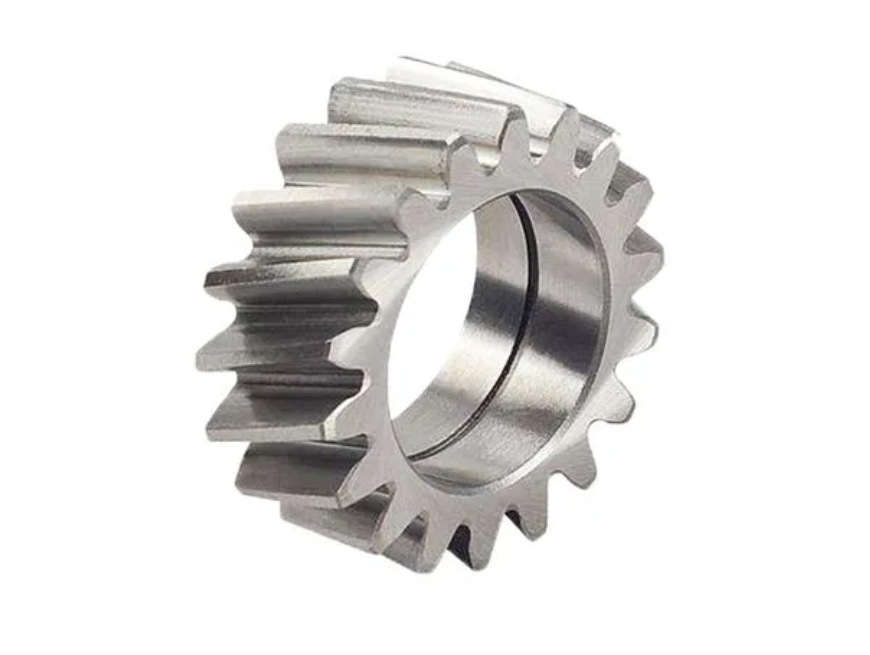
1. High-Performance Alloys
- Advanced Steel Alloys: New formulations of steel, such as ultra-high-strength steels, have been developed for higher fatigue resistance and strength-to-weight ratio.
- Titanium Alloys: Known for their high strength, low weight, and excellent corrosion resistance, titanium alloys are increasingly used for high-performance helical gear in aerospace and automotive applications.
2. Surface Hardening Techniques
- Case Hardening: This process, involving carburizing or nitriding, improves wear resistance while maintaining the toughness of the core material.
- Induction Hardening: Used to selectively harden areas of helical gear that are more prone to wear, thereby improving life span without compromising flexibility.
3. Coating Technologies
- Diamond-Like Carbon (DLC) Coatings: DLC coatings significantly reduce friction, wear, and tear, and protect against corrosion.
- Thermal Spray Coatings: Techniques like high-velocity oxygen fuel (HVOF) coating apply wear-resistant materials to helical gear surface, enhancing longevity.
4. Composite Materials
- Fiber-Reinforced Composites: Helical gears made from composites like carbon fiber-reinforced polymers offer high strength and reduced weight, which is particularly beneficial in aerospace applications.
- Metal Matrix Composites (MMCs): These combine the toughness of metal with the benefits of other materials like ceramics, leading to improved wear resistance and thermal properties.
5. Powder Metallurgy and Additive Manufacturing
- Powder Metallurgy: This process allows for the creation of very precise and complex helical gear geometries with excellent material properties.
- 3D Printing: Additive manufacturing is emerging as a powerful method for producing helical gear with optimized designs that are difficult or impossible to achieve with traditional methods.
6. Non-Metallic Materials
- Polymers and Plastics: High-grade polymers are being used for lower-load applications where noise reduction is a priority.
- Ceramics: In some specialized applications, ceramics offer outstanding heat resistance and durability.
7. Nanotechnology
- Nanocomposite Materials: Incorporating nanoparticles into helical gear materials can significantly enhance mechanical properties such as hardness and wear resistance.
8. Cryogenic Treatment
- Deep Cryogenic Treatment: This process stabilizes and increases the wear resistance of helical gear material.
Conclusion
These advancements in helical gear material science are pivotal in pushing the boundaries of gear performance, durability, and efficiency. They enable helical gear to operate under higher loads, at higher speeds, and in more challenging environments than ever before. As material science continues to evolve, we can expect further innovations that will enhance the capabilities of helical gear in various industrial applications.