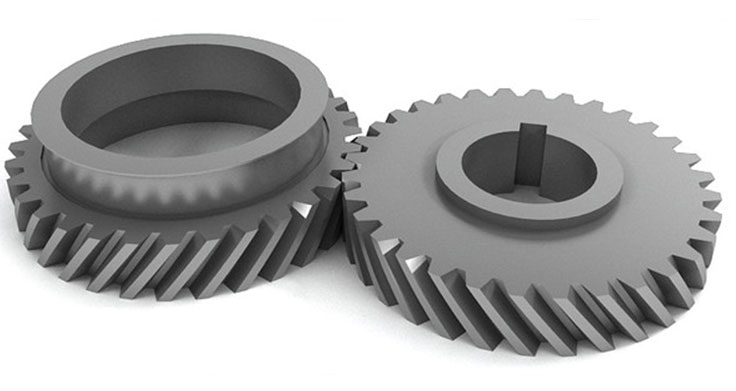
Advancements in helical gear technology have focused on enhancing load capacity and durability, allowing helical gears to withstand higher forces and operate under more demanding conditions. These advancements have been achieved through improved design, material selection, manufacturing techniques, and gear analysis. Here are some key advancements that have contributed to improving the load capacity and durability of helical gears:
1. Advanced Gear Design Software:
- The use of advanced gear design software allows engineers to optimize the gear geometry, tooth profile, and contact patterns. Finite element analysis (FEA) and computational fluid dynamics (CFD) simulations help evaluate stress distribution and load-carrying capacity, enabling the design of gears with enhanced durability.
2. Optimized Tooth Profiles:
- Advancements in tooth profile optimization have led to the development of new helical gear tooth forms that distribute loads more evenly. These optimized tooth profiles improve load-carrying capacity and reduce wear and contact stresses.
3. Enhanced Material Selection:
- The selection of high-performance materials with improved strength, toughness, and wear resistance has significantly contributed to the load capacity and durability of helical gears. The use of specialized gear steels and surface treatments enhances gear performance.
4. Improved Heat Treatment Techniques:
- Advanced heat treatment processes, such as carburizing, quenching, and tempering, ensure uniform hardness and case depth in the gear teeth. This results in increased wear resistance and fatigue strength, leading to greater durability.
5. Surface Coatings and Treatments:
- The application of advanced surface coatings, such as nitriding, diamond-like carbon (DLC) coating, or shot peening, enhances surface hardness and reduces friction, further improving gear durability.
6. Microgeometry Optimization:
- Microgeometry modifications, such as tooth flank crowning and lead corrections, optimize the gear meshing behavior and promote uniform load distribution, which contributes to improved load capacity and reduced wear.
7. Lubrication and Cooling Systems:
- Advancements in lubrication technology and cooling systems help maintain optimal operating conditions for helical gears. Proper lubrication ensures reduced friction and wear, while efficient cooling prevents overheating and extends gear life.
8. Precision Manufacturing:
- Advanced manufacturing techniques, including CNC machining, gear grinding, and gear shaving, ensure high precision in gear manufacturing, resulting in better gear meshing, reduced noise, and improved load-carrying capacity.
9. Gear Testing and Validation:
- Rigorous gear testing and validation processes have been improved, helping manufacturers verify gear performance under various operating conditions, ensuring that the gears meet the required load capacity and durability standards.
10. Gearbox Design Optimization:
- Integrated gear system design optimization, including the selection of appropriate bearings, housing, and lubrication systems, ensures that the entire gearbox is designed to handle the anticipated loads, leading to improved gear durability.
These advancements in helical gear technology have resulted in gears with increased load capacity, reduced wear, and improved overall durability. These gears can now withstand higher forces and operate reliably in demanding applications, making them essential components in various industries, including automotive, aerospace, industrial machinery, and robotics.